e10vk
UNITED STATES
SECURITIES AND EXCHANGE COMMISSION
Washington, D.C. 20549
FORM 10-K
|
|
|
þ |
|
Annual report pursuant to Section 13 or 15(d) of the Securities Exchange Act of 1934 |
For the fiscal year ended June 29, 2008.
|
|
|
o |
|
Transition report pursuant to Section 13 or 15(d) of the Securities Exchange Act of 1934 |
Commission File Number 0-25150
STRATTEC SECURITY CORPORATION
(Exact name of registrant as specified in its charter)
|
|
|
Wisconsin
|
|
39-1804239 |
|
|
|
(State of Incorporation)
|
|
(I.R.S. Employer Identification No.) |
3333 West Good Hope Road, Milwaukee, WI 53209
(Address of principal executive offices)
(414) 247-3333
(Registrants telephone number, including area code)
Securities registered pursuant to Section 12(b) of the Act:
|
|
|
Title of each class
|
|
Name of exchange on which registered |
|
|
|
Common Stock, $.01 par value
|
|
The NASDAQ Stock Market |
Securities registered pursuant to Section 12(g) of the Act:
None
(Title of Class)
Indicate by check mark if the registrant is a well-known seasoned issuer, as defined in Rule 405.
o Yes þ No
Indicate by check mark if the registrant is not required to file reports pursuant to Section 13 or
Section 15(d) of the Act. o Yes þ No
Indicate by check mark whether the registrant (1) has filed all reports required to be filed by
Section 13 or 15(d) of the Securities Exchange Act of 1934 during the preceding 12 months (or for
such shorter period that the registrant was required to file such reports), and (2) has been
subject to such filing requirements for the past 90 days. þ Yes o No
Indicate by check mark if disclosure of delinquent filers pursuant to Item 405 of Regulation S-K is
not contained herein, and will not be contained, to the best of the registrants knowledge, in
definitive proxy or information statements incorporated by reference in Part III of this Form 10-K
or any amendment of this Form 10-K. þ
Indicate by check mark whether the registrant is a large accelerated filer, an accelerated filer, a
non-accelerated filer, or a smaller reporting company. See the definitions of large accelerated
filer, accelerated filer and smaller reporting company in Rule 12b-2 of the Exchange Act.
(Check one):
|
|
|
|
|
|
|
Large accelerated filer o
|
|
Accelerated filer þ
|
|
Non-accelerated filer o
|
|
Smaller reporting company o |
|
|
|
|
(Do not check if a smaller reporting company) |
|
|
Indicate by check mark whether the registrant is a shell company (as defined in Rule 12b-2 of the
Exchange Act). o Yes þ No
The aggregate market value of the voting Common Stock held by non-affiliates of the registrant as
of December 28, 2007 (the last business day of the Registrants most recently completed second
quarter), was approximately $144,350,000 (based upon the last reported sale price of the Common
Stock at December 28, 2007, on the NASDAQ Global Market). Shares of common stock held by any
executive officer or director of the registrant have been excluded from this computation because
such persons may be deemed to be affiliates. This determination of affiliate status is not a
conclusive determination for other purposes.
On August 8, 2008, there were outstanding 3,270,904 shares of $.01 par value Common Stock.
Documents Incorporated by Reference
|
|
|
|
|
Part of the Form 10-K |
Document |
|
into which incorporated |
Portions of the Annual Report to Shareholders for the
fiscal year ended June 29, 2008.
|
|
I, II, IV |
|
|
|
Portions of the Proxy Statement dated August 29, 2008, for the
Annual Meeting of Shareholders to be held on October 7, 2008.
|
|
III |
PROSPECTIVE INFORMATION
A number of the matters and subject areas discussed in this Form 10-K as well as in portions of the
Companys 2008 Annual Report to Shareholders and the Companys Proxy Statement, dated August 29,
2008, which are incorporated herein by reference, contain forward-looking statements within the
meaning of the Private Securities Litigation Reform Act of 1995. These statements may be
identified by the use of forward-looking words or phrases such as anticipate, believe, would,
expect, intend, may, planned, potential, should, will and could. These statements
include expected future financial results, product offerings, global expansion, liquidity needs,
financing ability, planned capital expenditures, managements or the Companys expectations and
beliefs, and similar matters discussed in this Form 10-K. The discussions of such matters and
subject areas are qualified by the inherent risks and uncertainties surrounding future expectations
generally, and also may materially differ from the Companys actual future experience.
The Companys business, operations and financial performance are subject to certain risks and
uncertainties, which could result in material differences in actual results from the Companys
current expectations. These risks and uncertainties include, but are not limited to, general
economic conditions, in particular relating to the automotive industry, customer demand for the
Companys and its customers products, competitive and technological developments, customer
purchasing actions, foreign currency fluctuations, costs of operations and other matters described
under Risk Factors in the Managements Discussion and Analysis section of the Companys 2008
Annual Report to Shareholders, which is incorporated herein by reference in Item 1A of this report
and in the Companys other filings with the Securities and Exchange Commission.
Shareholders, potential investors and other readers are urged to consider these factors carefully
in evaluating the forward-looking statements and are cautioned not to place undue reliance on such
forward-looking statements. The forward-looking statements made herein are only made as of the
date of this Form 10-K and the Company undertakes no obligation to publicly update such
forward-looking statements to reflect subsequent events or circumstances occurring after the date
of this Form 10-K.
2
TABLE OF CONTENTS
PART I
Item 1. Business
The information set forth under Company Description which appears on pages 5 through 10 of the
Companys 2008 Annual Report to Shareholders is incorporated herein by reference. For information
as to export sales, see the information set forth under Notes to Financial Statements-Export
Sales included on page 35 of the Companys 2008 Annual Report to Shareholders, which is
incorporated herein by reference.
Emerging Technologies
Automotive vehicle access systems, which are both theft deterrent and consumer friendly, are being
developed as electro-mechanical devices. Electronic companies are developing user identification
systems such as bio-systems, card holder (transmitter) systems, etc., while mechanical locks, keys,
housings, and latches are evolving to accommodate the electronics. This will result in more secure
vehicles and eventually accommodate passive entry and passive start systems. The Company believes
it is positioning itself as a vehicle access control supplier by building its product, engineering
and manufacturing expertise in the required electro-mechanical products, which include vehicle
access latches, keys with remote entry electronic systems, and housing-ignition systems with
passive start capabilities.
These technologies benefit the Company by increasing the potential customer base as a Tier 2
supplier while attaining Tier 1 status on some product lines and adding additional product line
availability.
Sources and Availability of Raw Materials
The Companys primary raw materials are high-grade zinc, brass, magnesium, aluminum and plastic
resins. These materials are generally available from a number of suppliers, but the Company has
chosen to concentrate the sourcing with one primary vendor for each commodity. The Company believes
its sources for raw materials are very reliable and adequate for our needs. The Company has not
experienced any significant long term supply problems in its operations and does not anticipate any
significant supply problems in the foreseeable future. See further discussion under Risk
Factors-Sources of and Fluctuations in Market Prices of Raw Materials included on pages 17 and 18
of the Companys 2008 Annual Report to Shareholders, which is incorporated herein by reference.
Patents, Trademarks and Other Intellectual Property
The Company believes that the success of its business will not only result from the technical
competence, creativity and marketing abilities of its employees but also from the protection of its
intellectual property through patents, trademarks and copyrights. As part of its ongoing research,
development and manufacturing activities, the Company has a policy of seeking patents on new
products, processes and improvements when appropriate.
Although, in the aggregate, the patents discussed above are of considerable importance to the
manufacturing and marketing of many of its products, the Company does not consider any single
patent or trademark or group of patents or trademarks to be material to its business as a whole,
except for the STRATTEC and STRATTEC with logo trademarks.
The Company also relies upon trade secret protection for its confidential and proprietary
information. The Company maintains confidentiality agreements with its key executives. In addition,
the Company enters into confidentiality agreements with selected suppliers, consultants and
associates as appropriate to evaluate new products or business relationships pertinent to the
success of the Company. However, there can be no assurance that others will not independently
obtain similar information and techniques or otherwise gain access to the Companys trade secrets
or that the Company can effectively protect its trade secrets.
Dependence Upon Significant Customers
A very significant portion of the Companys annual sales are to General Motors Corporation, Delphi
Corporation, Ford Motor Company, and Chrysler LLC. These four customers accounted for
approximately 75 percent of the Companys net sales in 2008 and 80 percent of the Companys net
sales in both 2007 and 2006. Further information regarding sales to the Companys largest
customers is set forth under the caption Risk Factors Loss of Significant Customers, Vehicle
Content, Vehicle Models and Market Share included on page 17 of the Companys 2008 Annual Report
to Shareholders and Notes to Financial Statements-Sales and Receivable Concentration included on
page 35 of the Companys 2008 Annual Report to Shareholders, both of which are incorporated herein
by reference.
3
The products sold to these customers are model specific, fitting only certain defined applications.
Consequently, the Company is highly dependent on its major customers for their business, and on
these customers ability to produce and sell vehicles which utilize the Companys products. The
Company has enjoyed relationships with General Motors Corporation, Chrysler LLC, Ford Motor
Company, Delphi Corporation and other customers in the past, and expects to do so in the future.
However, a significant change in the purchasing practices of, or a significant loss of volume from,
one or more of these customers could have a detrimental effect on the Companys financial
performance.
The Company has recently added resources and increased its emphasis on the New Domestic and the
Tier 1 customer base in order to lessen the Companys dependence upon its significant customers.
Sales and Marketing
The Company provides its customers with engineered locksets, steering column lock housings, latches
and other access products which are unique to specific vehicles. Any given vehicle will typically
take 1 to 3 years of development and engineering design time prior to being offered to the public.
The locksets, lock housings and latches are designed concurrently with the vehicle. Therefore,
commitment to the Company as the production source occurs 1 to 3 years prior to the start of
production. The Company employs an engineering staff that assists in providing design and
technical solutions to its customers. The Company believes that its engineering expertise is a
competitive advantage and contributes toward its strong market position. For example, the Company
believes it regularly provides innovative design proposals for new model ignition locks, door
locks, latches and ignition lock housings to its customers that will improve vehicle security
system quality, theft deterrence and system cost.
The typical process used by automotive manufacturers in selecting a lock, lock housing or latch
supplier is to offer the business opportunity to the Company and several of the Companys
competitors. Each competitor will pursue the opportunity, doing its best to provide the customer
with the most attractive proposal. Price pressure is strong during this process but once an
agreement is reached, a commitment is made for each year of the product program. Typically, price
reductions resulting from productivity improvement by the Company are included in the contract and
are estimated in evaluating each of these opportunities by the Company. A blanket purchase order, a
contract indicating a specified part will be supplied at a specified price during a defined time
period, is issued by customers for each model year. Production quantity releases or quantity
commitments are made to that purchase order for weekly deliveries to the customer. As a consequence
and because the Company is a Just-in-Time supplier to the automotive industry, it does not
maintain a backlog of orders in the classic sense for future production and shipment.
Competition
The Company competes with domestic and foreign-based competitors on the basis of custom product
design, engineering support, quality, delivery and price. While the number of direct competitors
is currently relatively small, the automotive manufacturers actively encourage competition between
potential suppliers. The Company has a large share of the North
American market for its lock and key products because of its
ability to provide total value, which is a beneficial combination of price, quality, technical
support, program management innovation and aftermarket support. In order to reduce lockset or
housing production costs while still offering a wide range of technical support, the Company
utilizes assembly and component manufacturing operations in Mexico, which results in lower labor
costs as compared to the United States.
As locks become more sophisticated and involve additional electronics, competitors with specific
electronic expertise may emerge to challenge the Company. To address this, the Company has
strengthened its electrical engineering knowledge and service. It is also working with several
electronics suppliers to jointly develop and supply these advanced products.
The Companys lockset and housing competitors include Huf North America, Ushin-Ortech, Tokai-Rika,
Alpha-Tech, Valeo, Honda Lock, Methode, and Shin Chang. For additional information related to
competition, see the information set forth under Risk Factors-Highly Competitive Automotive Supply
Industry included on page 18 of the Companys 2008 Annual Report to Shareholders, which is
incorporated herein by reference.
4
Research and Development
The Company engages in research and development activities pertinent to automotive access control.
A major area of focus for research is the expanding role of vehicle access via electronic
interlocks and modes of communicating authorization data between consumers and vehicles.
Development activities include new products, applications and product performance improvements. In
addition, specialized data collection equipment is developed to facilitate increased product
development efficiency and continuous quality improvements. For fiscal years 2008, 2007, and 2006,
the Company spent approximately $2,900,000, $2,200,000, and $2,300,000, respectively, on research
and development. The Company believes that, historically, it has committed sufficient resources to
research and development and anticipates increasing such expenditures in the future as required to
support additional product programs associated with both existing and new customers. Patents are
pursued and will continue to be pursued as appropriate to protect the Companys interests resulting
from these activities.
Customer Tooling
The Company incurs costs related to tooling used in component production and assembly. See the
information set forth under Notes to Financial Statements-Customer Tooling in Progress included
on page 24 of the Companys 2008 Annual Report to Shareholders, which is incorporated herein by
reference.
Environmental Compliance
As is the case with other manufacturers, the Company is subject to Federal, state, local and
foreign laws and other legal requirements relating to the generation, storage, transport, treatment
and disposal of materials as a result of its housing, lock and key manufacturing and assembly
operations. These laws include the Resource Conservation and Recovery Act (as amended), the Clean
Air Act (as amended), the Clean Water Act of 1990 (as amended) and the Comprehensive Environmental
Response, Compensation and Liability Act (as amended). The Company has an environmental management
system that is ISO-14001 certified. The Company believes that its existing environmental
management system is adequate and it has no current plans for substantial capital expenditures in
the environmental area.
As discussed in Notes to Financial Statements-Commitments and Contingencies included on pages 28
and 29 of the Companys 2008 Annual Report to Shareholders, which is incorporated herein by
reference, a site at the Companys Milwaukee facility is contaminated by a solvent spill from a
former above-ground solvent storage tank located on the east side of the facility, which occurred
in 1985. This situation is being monitored by the Company.
The Company does not currently anticipate any materially adverse impact on its financial statements
or competitive position as a result of compliance with Federal, state, local and foreign
environmental laws or other legal requirements. However, risk of environmental liability and
charges associated with maintaining compliance with environmental laws is inherent in the nature of
the Companys business and there is no assurance that material liabilities or charges could not
arise.
Employees
At June 29, 2008, the Company had approximately 2,000 full-time employees, of which approximately
217 or 10.9 percent were represented by a labor union, which accounts for all production associates
at the Companys Milwaukee facility. In June 2008, a new contract with the unionized associates
was ratified and is effective through June 30, 2012. During June 2001, there was a 16-day strike
by the represented employees at the Companys Milwaukee facility. Further information regarding the
strike, work stoppages and other labor matters are discussed under Risk Factors-Disruptions Due to
Work Stoppages and Other labor Matters included on page and 18 of the Companys 2008 Annual Report
to Shareholders, which is incorporated herein by reference.
Available Information
The Company maintains its corporate website at www.strattec.com and makes available, free of
charge, through this website its code of business ethics, annual report on Form 10-K, quarterly
reports on Form 10-Q, current reports on Form 8-K and amendments to those reports that the Company
files with, or furnishes to, the Securities and Exchange Commission (the Commission) as soon as
reasonably practicable after the Company electronically files such material with, or furnishes it
to, the Commission. The Company is not including the information contained on or available through
its website as a part of, or incorporating such information by reference into, this Annual Report
on Form 10-K. This report includes (or incorporated by reference) all material information about
the Company that is included on the Companys website and is otherwise required to be included in
this report.
5
Item 1A. Risk Factors
The information set forth under Risk Factors which appears on pages 17 and 18 of the Companys
2008 Annual Report to Shareholders is incorporated herein by reference.
Item 1B. Unresolved Staff Comments
None.
Item 2. Properties
The Company has three manufacturing plants, one warehouse, and a sales office. These facilities are
described as follows:
|
|
|
|
|
|
|
|
|
Location |
|
Type |
|
Sq. Ft. |
|
Owned or Leased |
Milwaukee, Wisconsin
|
|
Headquarters and General Offices; Component
Manufacturing, Assembly and Service Parts
Distribution
|
|
|
352,000 |
|
|
Owned |
Juarez, Chihuahua Mexico
|
|
Subsidiary Offices and Assembly
|
|
|
97,000 |
|
|
Owned |
Juarez, Chihuahua Mexico
|
|
Subsidiary Offices, Key Finishing Injection
Molding and Assembly Operations
|
|
|
62,000 |
|
|
Leased |
El Paso, Texas
|
|
Finished Goods Warehouse
|
|
|
38,000 |
|
|
Leased** |
Troy, Michigan
|
|
Sales and Engineering Office for Detroit
Customer Area
|
|
|
7,700 |
|
|
Leased** |
|
|
|
** |
|
Leased unit within a complex. |
The Company is currently constructing a new manufacturing facility in Juarez, Mexico. The land was
purchased in March 2008. The new facility will replace the current leased facility where key
finishing injection molding and assembly operations are located. The square footage of the new
facility will total 134,000. The Company believes that with the construction of the new plant, its
production facilities will be adequate for the foreseeable future.
Item 3. Legal Proceedings
In the normal course of business the Company may be involved in various legal proceedings from
time to time. The Company does not believe it is currently involved in any claim or action the
ultimate disposition of which would have a material adverse effect on the Companys financial
statements.
Item 4. Submission of Matters to a Vote of Security Holders
There were no matters submitted to a vote of shareholders during the fourth quarter of fiscal 2008.
6
PART II
Item 5. Market for Registrants Common Equity, Related Stockholder Matters and Issuer Purchases
of Equity Securities
The Companys Board of Directors authorized a stock repurchase program on October 16, 1996, and the
program was publicly announced on October 17, 1996. The Board of Directors has periodically
increased the number of shares authorized for repurchase under the
program. At June 29, 2008, the number of shares of the Companys
common stock authorized for repurchase under the program totaled
3,639,395. On August 19, 2008, the Board of Directors authorized an
additional 200,000 shares for repurchase under the program. The program
currently authorizes the repurchase of the Companys common stock from
time to time, directly or through brokers or agents, and has no expiration date. Over the life of
the repurchase program through June 29, 2008, a total of 3,461,333 shares have been repurchased at
a cost of approximately $130.2 million. Subsequent to June 29,
2008, an additional 172,500 shares were repurchased at a cost of
approximately $5.7 million.
Issuer Purchases of Equity Securities:
|
|
|
|
|
|
|
|
|
|
|
|
|
|
|
|
|
|
|
Total |
|
Average |
|
Total Number |
|
Maximum Number |
|
|
Number |
|
Price |
|
Of Shares Purchased |
|
Of Shares that May |
|
|
Of Shares |
|
Paid Per |
|
As Part of Publicly |
|
Yet be Purchased |
Period |
|
Purchased |
|
Share |
|
Announced Program |
|
Under the Program |
March 31, 2008 - May 4, 2008 |
|
|
18,928 |
|
|
$ |
38.27 |
|
|
|
18,928 |
|
|
|
179,462 |
|
May 5, 2008 - June 1, 2008 |
|
|
1,400 |
|
|
$ |
36.78 |
|
|
|
1,400 |
|
|
|
178,062 |
|
June 2, 2008 - July 29, 2008 |
|
|
|
|
|
|
|
|
|
|
|
|
|
|
178,062 |
|
|
|
|
|
|
|
|
|
|
|
|
|
|
|
|
|
|
Total |
|
|
20,328 |
|
|
$ |
38.16 |
|
|
|
20,328 |
|
|
|
178,062 |
|
|
|
|
|
|
|
|
|
|
|
|
|
|
|
|
|
|
The Companys common stock is traded on the NASDAQ Global Market under the symbol STRT.
The information set forth under Financial Summary Quarterly Financial Data (Unaudited) included
on page 39 of the Companys 2008 Annual Report to Shareholders is incorporated herein by reference.
Item 6. Selected Financial Data
The information set forth under Five Year Financial Summary which appears on page 39 of the
Companys 2008 Annual Report to Shareholders is incorporated herein by reference. Such
information should be read along with the Companys financial statements and the notes to those
financial statements and with Managements Discussion and Analysis of Financial Condition and
Results of Operations incorporated by reference elsewhere herein.
Item 7. Managements Discussion and Analysis of Financial Condition and Results of Operations
The information set forth under Managements Discussion and Analysis which appears on pages 11
through 18 of the Companys 2008 Annual Report to Shareholders is incorporated herein by reference.
Item 7A. Quantitative and Qualitative Disclosures About Market Risk
The Company did not hold any market risk sensitive instruments during the period covered by this
report.
Item 8. Financial Statements and Supplementary Data
The financial statements, together with the report thereon of Grant Thornton LLP dated August 19,
2008, the report of management on internal control over financial reporting and the report of Grant
Thornton LLP on internal control over financial reporting dated August 19, 2008, which appear on
pages 19 through 38 of the Companys 2008 Annual Report to Shareholders, are incorporated herein by
reference.
Our quarterly results of operations included under Financial Summary-Quarterly Financial Data
(Unaudited) which appears on page 39 of the Companys 2008 Annual Report to Shareholders is
incorporated herein by reference.
Item 9. Changes In and Disagreements with Accountants on Accounting and Financial Disclosure
None.
7
Item 9A. Controls and Procedures
As of the end of the period covered by this report, the Company carried out an evaluation under the
supervision and with the participation of the Companys management, including the Companys Chief
Executive Officer and Chief Financial Officer, of the Companys disclosure controls and procedures
(as defined in Rules 13a 15(e) and 15d 15(e) under the Securities Exchange Act of 1934, as
amended). Based on this evaluation, the Companys Chief Executive Officer and Chief Financial
Officer concluded that, as of the end of such period, the Companys disclosure controls and
procedures were effective in recording, processing, summarizing and reporting, on a timely basis,
information required to be disclosed by the Company in reports that the Company files with or
submits to the Commission. It should be noted that in designing and evaluating the disclosure
controls and procedures, management recognized that any controls and procedures, no matter how well
designed and operated, can provide only reasonable assurance of achieving the desired control
objectives, and management was necessarily required to apply its judgment in evaluating the
cost-benefit relationship of possible controls and procedures. The Company has designed its
disclosure controls and procedures to reach a level of reasonable assurance of achieving the
desired control objectives and based on the evaluation described above, the Companys Chief
Executive Officer and Chief Financial Officer concluded that the Companys disclosure controls and
procedures were effective at reaching that level of reasonable assurance.
There was no change in the Companys internal control over financial reporting (as defined in
Rules 13a-15(f) and 15d-15(f) under the Exchange Act) that occurred during the quarter ended June
29, 2008 that has materially affected, or is reasonably likely to materially affect, the Companys
internal control over financial reporting.
The report of management required under this Item 9A is included on page 36 of the Companys 2008
Annual Report to Shareholders under the heading Report on Managements Assessment of Internal
Control over Financial Reporting and is incorporated herein by reference.
The attestation report required under this Item 9A is included on page 37 of the Companys 2008
Annual Report to Shareholders under the heading Report of Independent Registered Public Accounting
Firm and is incorporated herein by reference.
Item 9B. Other Information
Not applicable.
8
PART III
Item 10. Directors and Executive Officers and Corporate Governance
The information included in the Companys Proxy Statement, dated August 29, 2008, under Proposal:
Election of Directors, Code of Business Ethics, Audit Committee Financial Expert, Executive
Officers, Section 16(a) Beneficial Ownership Reporting Compliance, and Director Nominations
is incorporated herein by reference.
The Audit Committee of the Companys Board of Directors is an audit committee for purposes of
Section 3(a)(58)(A) of the Securities Exchange Act of 1934. The members of the Audit Committee
consist of four outside independent Directors, Michael J. Koss, Audit Committee Chairman, Robert
Feitler, Frank J. Krejci and David R. Zimmer.
Item 11. Executive Compensation
The information included in the Companys Proxy Statement, dated August 29, 2008, under Director
Compensation and Executive Compensation is incorporated herein by reference.
The information incorporated by reference from Report of Compensation Committee in the Companys
Proxy Statement, dated August 29, 2008, shall not be deemed Filed for purposes of Section 18 of
the Securities Exchange Act of 1934, nor shall it be deemed incorporated by reference in any filing
under the Security Exchange Act of 1933, except as shall be expressly set forth by specific
reference in such filing.
Item 12. Security Ownership of Certain Beneficial Owners and Management and Related Shareholder
Matters
The information included in the Companys Proxy Statement, dated August 29, 2008, under Security
Ownership is incorporated herein by reference.
Equity Compensation Plan Information
The following table summarizes share information, as of June 29, 2008, for the Companys Stock
Incentive Plan.
|
|
|
|
|
|
|
|
|
|
|
|
|
|
|
Number of |
|
|
|
|
|
|
Number of |
|
|
|
common shares to be |
|
|
|
|
|
|
common shares |
|
|
|
issued upon exercise |
|
|
Weighted-average |
|
|
available for future |
|
|
|
of outstanding |
|
|
exercise price of |
|
|
issuance under |
|
|
|
options, |
|
|
outstanding options, |
|
|
equity |
|
Plan Category |
|
warrants, and rights |
|
|
warrants, and rights |
|
|
compensation plans |
|
Equity compensation
plans approved by
shareholders |
|
|
187,780 |
|
|
$ |
58.74 |
|
|
|
380,463 |
|
Equity compensation
plans not approved
by shareholders |
|
|
|
|
|
|
|
|
|
|
|
|
|
|
|
|
|
|
|
|
|
|
Total |
|
|
187,780 |
|
|
$ |
58.74 |
|
|
|
380,463 |
|
|
|
|
|
|
|
|
|
|
|
Item 13. Certain Relationships and Related Transactions and Director Independence
The information included in the Companys Proxy Statement, dated August 29, 2008, under Executive
Compensation, Transactions With Related Personsand Director Independence is incorporated
herein by reference.
Item 14. Principal Accountant Fees and Services
The information included in the Companys Proxy Statement, dated August 29, 2008, under Fees of
Independent Registered Public Accounting Firm is incorporated herein by reference.
9
PART IV
Item 15. Exhibits and Financial Statement Schedules
(a) |
|
The following documents are filed as part of this report: |
|
(1)(i) |
|
Financial Statements The following financial statements of the Company, included on pages 19 through 38 of the Companys 2008 Annual Report to Shareholders,
are incorporated by reference in Item 8 of this Form 10-K annual
report: |
|
|
|
|
Reports of Independent Registered Public Accounting Firm |
|
|
|
|
Consolidated Balance Sheets as of June 29, 2008 and July 1, 2007 |
|
|
|
|
Consolidated Statements of Income years ended June 29, 2008, July 1, 2007 and July 2, 2006 |
|
|
|
|
Consolidated Statements of Shareholders Equity years ended June 29, 2008, July 1,
2007 and July 2, 2006 |
|
|
|
|
Consolidated Statements of Cash Flows years ended June 29, 2008, July 1, 2007 and July 2,
2006 |
|
|
|
|
Notes to Financial Statements |
|
(2) |
|
Financial Statement Schedule |
|
|
|
|
All schedules have been omitted because they are not applicable or are not required, or
because the required information has been included in the Financial Statements or Notes thereto. |
|
|
(3) |
|
Exhibits. See Exhibit Index beginning on page 12. |
(b) |
|
Exhibits |
|
|
|
See Exhibit Index and the exhibits attached
hereto or previously filed as described on the Exhibit
Index beginning on page 12. |
|
(c) |
|
Financial Statement Schedules |
|
|
|
Not required. |
10
SIGNATURES
Pursuant to the requirements of Section 13 of the Securities Exchange Act of 1934, the Registrant
has duly caused this report to be signed on its behalf by the undersigned thereunto duly
authorized.
|
|
|
|
|
|
STRATTEC SECURITY CORPORATION
|
|
|
By: |
/s/ Harold M. Stratton II
|
|
|
Harold M. Stratton II |
|
|
Chairman, President and Chief Executive Officer |
|
|
Date: August 29, 2008
Pursuant to the requirement of the Securities Exchange Act of 1934, this report has been signed
below by the following persons on behalf of the Registrant and in the capacities and on the dates
indicated.
|
|
|
|
|
Signature |
|
Title |
|
Date |
|
|
|
|
|
/s/ Harold M. Stratton II
|
|
Chairman, President, Chief Executive
Officer, and Director
|
|
August 29, 2008 |
Harold M. Stratton II
|
|
(Principal Executive Officer) |
|
|
|
|
|
|
|
|
|
Director
|
|
August 19, 2008 |
Frank J. Krejci |
|
|
|
|
|
|
|
|
|
|
|
Director
|
|
August 19, 2008 |
Michael J. Koss |
|
|
|
|
|
|
|
|
|
|
|
Director
|
|
August 19, 2008 |
Robert Feitler |
|
|
|
|
|
|
|
|
|
|
|
Director
|
|
August 19, 2008 |
David R. Zimmer |
|
|
|
|
|
|
|
|
|
|
|
Senior Vice President, Chief
Financial Officer, Secretary and Treasurer
|
|
August 29, 2008 |
Patrick J. Hansen
|
|
(Principal Financial and Accounting Officer) |
|
|
11
EXHIBIT INDEX TO ANNUAL REPORT
ON FORM 10-K
|
|
|
|
|
Exhibit |
|
|
|
|
3.1 (2)
|
|
Amended and Restated Articles of Incorporation of the Company
|
|
* |
|
|
|
|
|
3.2 (9)
|
|
By-laws of the Company
|
|
* |
|
|
|
|
|
4.1 (11)
|
|
Promissory Note dated November 1, 2007 by and between the Company and M&I Bank
|
|
* |
|
|
|
|
|
10.1 (9) **
|
|
Amended STRATTEC SECURITY CORPORATION Stock Incentive Plan
|
|
* |
|
|
|
|
|
10.2 (9) **
|
|
Form of Restricted Stock Grant Agreement
|
|
* |
|
|
|
|
|
10.3 (3)(4)(5)(6)(7)(8)(12)**
|
|
Employment Agreements between the Company and the identified executive officers
|
|
* |
|
|
|
|
|
10.4 (1)(3)(4)(5)(6)(7)(8)(12)**
|
|
Change In Control Agreements between the Company and the identified executive officers
|
|
* |
|
|
|
|
|
10.5 (13) **
|
|
Amended STRATTEC SECURITY CORPORATION Economic Value Added Plan for
Executive Officers and Senior Managers
|
|
* |
|
|
|
|
|
10.6 (13) **
|
|
Amended STRATTEC SECURITY CORPORATION Economic Value Added Plan for
Non-employee Members of the Board of Directors
|
|
* |
|
|
|
|
|
10.7 (10) **
|
|
Amended STRATTEC SECURITY
CORPORATION Supplemental Executive Retirement Plan
|
|
* |
|
|
|
|
|
13
|
|
Annual Report to Shareholders for the year ended June 29, 2008 |
|
|
|
|
|
|
|
21 (13)
|
|
Subsidiaries of the Company
|
|
* |
|
|
|
|
|
23.1
|
|
Consent of Independent Registered Public Accounting Firm dated August 19, 2008 |
|
|
|
|
|
|
|
31.1
|
|
Rule 13a-14(a) Certification for Harold M. Stratton II, Chairman and Chief
Executive Officer |
|
|
|
|
|
|
|
31.2
|
|
Rule 13a-14(a) Certification for Patrick J. Hansen, Chief Financial Officer |
|
|
|
|
|
|
|
32 (14)
|
|
18 U.S.C. Section 1350 Certifications |
|
|
|
|
|
* |
|
Previously filed |
|
** |
|
Management contract or compensatory plan or arrangement |
|
(1) |
|
Incorporated by reference from Amendment No. 1 to the Form 10 filed on January 20,
1995. |
|
(2) |
|
Incorporated by reference from Amendment No. 2 to the Form 10 filed on February 6,
1995. |
|
(3) |
|
Incorporated by reference from the June 27, 1999 Form 10-K filed on September
17, 1999. |
|
(4) |
|
Incorporated by reference from the July 1, 2001 Form 10-K filed on September 4,
2001. |
|
(5) |
|
Incorporated by reference from the June 30, 2002 Form 10-K filed on August 28,
2002.
|
|
(6) |
|
Incorporated by reference from the June 29, 2003 Form 10-K filed on August 28,
2003. |
|
(7) |
|
Incorporated by reference from the September 26, 2004 Form 10-Q filed on
November 2, 2004. |
|
(8) |
|
Incorporated by reference from the March 27, 2005 Form 10-Q filed on April 29,
2005.
|
|
(9) |
|
Incorporated by reference from the Form 8-K filed on October 7, 2005. |
|
(10) |
|
Incorporated by reference from the January 1, 2006 Form 10-Q filed on February
7, 2006. |
|
(11) |
|
Incorporated by reference from the September 30, 2007 Form 10-Q filed on
November 6, 2007. |
|
(12) |
|
Incorporated by reference from the April 1, 2007 Form 10-Q filed on May 8,
2007. |
|
(13) |
|
Incorporated by reference from the July 1, 2007 Form 10-K filed on August 30,
2007. |
|
(14) |
|
This certification is not filed for purposes of Section 18 of the Securities
Exchange Act of 1934, as amended, or incorporated by reference into any filing under the
Securities Act of 1933, as amended, or the Securities Exchange Act of 1934, as amended. |
12
exv13
Opening New Doors
2008 ANNUAL REPORT
Opening New Doors
A new era has begun for STRATTEC and our worldwide partners. Furthering our efforts to succeed
in todays challenging global marketplace, we are pleased to announce an acquisition that will add
power access devices to open and close sliding doors, liftgates and trunk lids to our core product
lineup. This represents a meaningful expansion of our product line, customer base and
electromechanical engineering capability. Literally and figuratively, we are opening new doors to
expanded opportunities and crossing the threshold into a new era.
2008 ANNUAL REPORT
STRATTEC SECURITY CORPORATION designs, develops, manufactures and markets
mechanical locks and keys, electronically enhanced locks and keys, steering column and
instrument panel ignition lock housings, latches, door handles and related access
control products for North American automotive customers, and for global automotive
manufacturers through the VAST Alliance in which we participate with WITTE Automotive of
Velbert, Germany and ADAC Automotive of Grand Rapids, Michigan. Our products are shipped
to customer locations in the United States, Canada, Mexico, Europe, South America and
China, and we provide full service and aftermarket support.
CONTENTS
|
|
|
|
|
|
|
|
|
2 |
|
|
|
|
|
4 |
|
|
|
|
|
5 |
|
|
|
|
|
10 |
|
|
|
|
|
11 |
|
|
|
|
|
19 |
|
|
|
|
|
36 |
|
|
|
|
|
37 |
|
|
|
|
|
39 |
|
|
|
|
|
40 |
|
|
|
|
|
41 |
|
|
PROSPECTIVE INFORMATION
A number of the matters and subject areas discussed in this Annual Report (see above
Contents section) contain forward-looking statements within the meaning of the
Private Securities Litigation Reform Act of 1995. These statements may be identified by
the use of forward-looking words or phrases such as anticipate, believe, would,
expect, intend, may, planned, potential, should, will and could. These
include expected future financial results, product offerings, global expansion, liquidity
needs, financing ability, planned capital expenditures, managements or the Companys
expectations and beliefs, and similar matters discussed in the Letter to the
Shareholders, Companys Managements Discussion and Analysis, etc. The discussions of
such matters and subject areas are qualified by the inherent risks and uncertainties
surrounding future expectations generally, and also may materially differ from the
Companys actual future experience.
The Companys business, operations and financial performance are subject to certain
risks and uncertainties, which could result in material differences in actual results
from the Companys current expectations. These risks and uncertainties include, but are
not limited to, general economic conditions, in particular relating to the automotive
industry, customer demand for the Companys and its customers products, competitive and
technological developments, customer purchasing actions, foreign currency fluctuations,
costs of operations and other matters described under Risk Factors in the Managements
Discussion and Analysis section of this report.
Shareholders, potential investors and other readers are urged to consider these
factors carefully in evaluating the forward-looking statements and are cautioned not to
place undue reliance on such forward-looking statements. The forward-looking statements
made herein are only made as of the date of this Annual Report and the Company undertakes
no obligation to publicly update such forward-looking statements to reflect subsequent
events or circumstances occurring after the date of this Annual Report.
LETTER TO THE SHAREHOLDERS
AUGUST, 2008
Fellow Shareholders:
Fiscal 2008 proved to be a very challenging year for our company. Our expectations
for a good year were eroded each quarter with the persistently bad news emanating from
our customer base in Detroit. While there were some positive developments for us, the
year was dominated by the bad news from Detroit and its effects on our operating and
financial performance.
The major elements of the bad news were: 1) The general decline of the US economy
and credit crunch which kept many consumers from making vehicle purchases; 2) the
significant escalation in the price of oil and the resultant run-up of gas prices to
$4-plus per gallon which caused a major shift in consumer preferences away from mid and
full-size trucks and SUVs to smaller, more fuel-efficient vehicles; 3) a twelve week
strike at a major supplier to General Motors starting in the latter portion of our third
quarter and continuing through most of our fourth quarter which caused a reduction in
production volumes across multiple vehicle lines at GM; and 4) severe cut-backs in
production at all of our customers during our fourth quarter in response to the shifts
in demand resulting from the first two elements. The combination of these four elements
came together in a perfect storm in our fourth quarter, leading to our first quarterly
loss since becoming STRATTEC in 1995.
The automotive industry is going through major changes, some of which are permanent,
and some transient. Until there is more stability in the economy and the automotive sector
in particular, we will be balancing near-term financial results with long-term strategic
initiatives. Common wisdom would tell us that, given the instability, we should be making
significant cost reductions in all areas of our business. However, we believe that given
the current industry adversity, there are opportunities for a capable supplier with a
strong financial base to gain future business. Consequently, we have elected not to reduce
costs that we see as critical to strategically positioning ourselves for the future. Over
the past few years we have been expanding our engineering capabilities outside our
traditional lock and key capability. These additional engineering resources have primarily
been focused on latch products and electrical/electronic capabilities to support all of
our products. In addition, we have added program management personnel to help us bring new
product programs online smoothly and efficiently. While minor adjustments to these
resources will always be a possibility, it is our intent to maintain the momentum we have
gained in developing new products and new customers.
The resources we have added over the last couple of years and other strategic
initiatives we are pursuing have worked well for us, and this brings me to the positive
developments that occurred during the year. For the second year in a row, we took over
additional lock and key business from a competitor at General Motors. This was
particularly important to us because most of this additional business is for passenger
cars, thus helping us reduce our dependence on truck and SUV production. Unfortunately,
due to market conditions the benefit of this additional business came late in our fiscal
year, and had only a minor impact on 2008. We also secured the take-over of some ignition
lock housing business from a competing supplier servicing Chrysler LLC. This business was
not expected to have much of an impact on fiscal 2008, and although it too is late, it
will be in production for most of fiscal 2009.
For 2010 and beyond, we were awarded a seat-back latch program for General Motors as
a Tier 2 supplier, and we are actively negotiating several additional latch opportunities
as a Tier 1 supplier. During the latter part of the year, substantive negotiations began
with a
LETTER TO THE SHAREHOLDERS
Japanese OEM for lock set and ignition lock housing business. These negotiations are
continuing as I write this letter and if successful, will represent our first business
with a major Japanese OEM.
During the last half of the year, we were awarded business that will have us supply
an electronic bladeless key as a Tier 2 supplier to a major electronics firm for a future
Chrysler product. We designed the key (which resembles a remote entry fob) and the
interface with the portion of the system that will be in the vehicle. This is significant
for several reasons, not the least of which is that it regains some vehicle content that
we lost on Chrysler vehicles using this type of bladeless system. It also reinforces our
belief that we have a role in providing the electrical/mechanical interface required in
electronic access control devices.
We made a commitment to expand our capacity in Mexico with the purchase of land in
Juarez, a few miles from our existing owned facility. Before the end of the fiscal year,
we broke ground for a new building on this land that will house STRATTEC Componentes
Automotrices which currently operates out of a leased facility we will be vacating. This
new building will allow us to also provide increased space for ADAC-STRATTEC de Mexico,
which we expect to grow in volume over the next few years.
Finally, the big event of the year was our announcement on May 27th of our agreement
to acquire, along with our Vehicle Access System Technologies LLC partners, the global
Power Products business unit of Delphi Corporation. STRATTECs portion of this
transaction is the North American engineering and assembly operations. To do this, we are
creating a new subsidiary of which we will own 80% and WITTE Automotive will own 20%. In
addition to their minority interest in the North American portion of the Power Products
business, WITTE will take over the European engineering and assembly operations. VAST LLC
will take over the Asian operations, which include a sales and engineering liaison office
in Korea primarily to support Hyundai/Kia, and an assembly line in China. We anticipate
that the transaction with Delphi will be completed on or before December 31, 2008.
Power Products consists of power actuation devices to open and close sliding doors
for vans and minivans, liftgates for SUVs and cross-over utility vehicles, and trunk lids
for passenger cars. Included in this product portfolio are electronic control units to
operate the power devices. This business provides us with new products, new customers and
new growth potential, as well as some electronics experience; all things which fit quite
well with our strategic intent to grow our access control product line. Please read the
Managements Discussion and Analysis and Notes to Financial Statements sections of
this report for additional information concerning this acquisition. The majority of the
Power Products business is in North America, and we anticipate the new subsidiary will
contribute up to $45 million in revenue for fiscal 2009. We are very excited about this
new business and the many things it brings to STRATTEC and our VAST partners.
Despite the ugliness of the current automotive business in North America, we have
been working hard to keep moving the company in a positive direction. We believe we are
positioning ourselves for a strong future, and that the progress to date has been
positive. It is hard to predict just how or when the current situation will resolve, but
we are confident that it will. And when it does, the companies which have taken this
opportunity to position themselves properly will enjoy the benefits. I believe we are one
of those companies.
Sincerely,
Harold M. Stratton II
Chairman, President and Chief Executive Officer
FINANCIAL HIGHLIGHTS
(IN MILLIONS)
|
|
|
|
|
|
|
|
|
|
|
|
|
|
|
2008 |
|
2007 |
|
2006 |
|
|
|
Net Sales |
|
$ |
159.6 |
|
|
$ |
167.7 |
|
|
$ |
181.2 |
|
Gross Profit |
|
|
25.6 |
|
|
|
26.5 |
|
|
|
37.0 |
|
Income from Operations |
|
|
1.6 |
|
|
|
6.3 |
|
|
|
13.4 |
|
Net Income |
|
|
3.3 |
|
|
|
8.2 |
|
|
|
12.5 |
|
Total Assets |
|
|
141.7 |
|
|
|
148.4 |
|
|
|
154.3 |
|
Total Debt |
|
|
|
|
|
|
|
|
|
|
|
|
Shareholders Equity |
|
|
95.4 |
|
|
|
103.0 |
|
|
|
110.3 |
|
ECONOMIC VALUE ADDED (EVA
®)
All U.S. associates and many of our Mexico-based salaried associates participate in
incentive plans that are based upon our ability to add economic value to the enterprise.
During 2008, our EVA® Plan was modified to include cash and cash equivalents
as part of the Companys net capital employed in the business. The EVA®
performance for 2008 was a negative $6.3 million. We believe that EVA®
represents STRATTECs ultimate measure of performance and shareholder value.
|
|
|
|
|
|
|
|
|
Net Operating Profit After Cash-Basis Taxes |
|
|
|
|
|
$ |
4.1 |
|
Average Net Capital Employed |
|
$ |
104.1 |
|
|
|
|
|
Capital Cost |
|
|
10% |
|
|
|
|
|
|
|
|
|
|
|
|
10.4 |
|
|
|
|
|
|
|
|
|
Economic Value Added |
|
|
|
|
|
$ |
(6.3 |
) |
|
|
|
|
|
|
|
|
EVA® is not a traditional financial measurement under U.S. GAAP and may
not be similar to EVA® calculations used by other companies. However,
STRATTEC believes the reporting of EVA® provides investors with greater
visibility of economic profit. The following is a reconciliation of the relevant GAAP
financial measures to the non-GAAP measures used in the calculation of STRATTECs
EVA®.
Net Operating Profit After Cash-Basis Taxes:
|
|
|
|
|
2008 Net Income as Reported |
|
$ |
3.3 |
|
Deferred Tax Provision |
|
|
.9 |
|
Other |
|
|
(.1 |
) |
|
|
|
|
Net Operating Profit After
Cash-Basis Taxes |
|
$ |
4.1 |
|
|
|
|
|
Average Monthly Net Capital Employed:
|
|
|
|
|
Total Shareholders Equity as Reported at June 29, 2008 |
|
$ |
95.4 |
|
Long-Term Liabilities |
|
|
12.4 |
|
Prepaid Pension Obligations |
|
|
(.7 |
) |
Long-Term Deferred Tax Asset |
|
|
(6.9 |
) |
Other |
|
|
(.3 |
) |
|
|
|
|
Net Capital Employed at June 29, 2008 |
|
$ |
99.9 |
|
Impact of 12 Month Average |
|
|
4.2 |
|
|
|
|
|
Average Monthly Net Capital Employed |
|
$ |
104.1 |
|
|
|
|
|
EVA® is a registered trademark of Stern, Stewart & Co.
|
|
|
|
|
COMPANY DESCRIPTION
BASIC BUSINESS
STRATTEC SECURITY CORPORATION designs, develops, manufactures and markets mechanical
locks and keys, electronically enhanced locks and keys, steering column and instrument
panel ignition lock housings, latches, door handles and related access control products
for North American automotive customers, and for global automotive manufacturers through
the VAST Alliance in which we participate with WITTE Automotive of Velbert, Germany and
ADAC Automotive of Grand Rapids, Michigan. Our products are shipped to customer locations
in the United States, Canada, Mexico, Europe, South America and China, and we provide
full service and aftermarket support.
HISTORY
STRATTEC formerly was a division of Briggs & Stratton Corporation. In 1995, STRATTEC was spun
off from Briggs & Stratton through a tax-free distribution to the then-existing Briggs & Stratton
shareholders and has since been an independent public company for thirteen years.
Our history in the automotive security business spans 100 years. STRATTEC has been the worlds
largest producer of automotive locks and keys since the late 1920s, and we currently maintain a
dominant share of the North American markets for these products.
PRODUCTS
Our traditional products are locks and keys for cars and light trucks. A typical new car uses
a set of two to three locks. A typical 3-way lockset contains a steering column/ignition lock, a
drivers door lock and a rear compartment (trunk, hatch or liftgate) lock. Pickup trucks also use
two to three locks, while sport utility vehicles and vans use three to five locks. Some vehicles
have additional locks for consoles, storage compartments or folding rear seats. Pickup truck
tailgate locks and spare tire locks are offered as options. Usually, two keys are provided with
each vehicle lockset. Most of the vehicles we currently supply are using keys with sophisticated radio
frequency identification technology for theft prevention. However, keys with remote entry devices
integrated into a single unit have been added to our product line.
A relatively new and growing product line for us is ignition lock housings. These housings are
the mating part for our ignition locks and typically are part of the steering column structure,
although there are instrument panel-mounted versions for certain vehicle applications. These
housings are typically zinc or magnesium die castings and can include electronic components for
theft deterrent systems.
We are also developing business for additional access control products, including trunk latches,
liftgate latches, tailgate latches, hood latches, side door latches and related hardware for this
product category. With a planned acquisition in 2009, we will be supplying power access devices for
sliding side doors, liftgates and trunk lids. Through a joint venture formed with ADAC Automotive
during fiscal 2007, we are also pursuing door handles and related vehicle access hardware.
MARKETS
We are a direct supplier to OEM auto and light truck manufacturers as well as other
transportation-related manufacturers. For the 2008 model year, our lock and key products
enjoyed a 43% market share in the North American automotive industry, supplying over 75%
of General Motors production, 50% of Fords production and 100% of Chryslers
production. Our growing ignition lock housing business captured an estimated 22% share
|
|
|
|
|
|
COMPANY DESCRIPTION
in 2008. Our housings and OEM components are also sold to other Tier 1 automotive
suppliers and industrial manufacturers.
Direct sales to various OEMs represented approximately 71% of our total sales for
fiscal 2008. The remainder of our revenue is received primarily through sales to the OEM
service channels, the aftermarket and Tier 1 customers.
Sales to our major automotive customers, both OEM and Tier 1, are coordinated through direct
sales personnel located in our Detroit-area office. Sales are also facilitated through daily
interaction between our customer Program Managers and Application Engineers located in Detroit and
product engineering departments. Sales to other OEM customers are accomplished through a
combination of our own sales personnel located in Detroit and personnel in our Milwaukee
headquarters office. STRATTECs products are supported by an extensive staff of experienced lock,
housing and latch engineers. This staff, which includes product design, quality and manufacturing
engineers, is capable of providing complete design, development and testing services of new
products for our customers. This staff also is available for customer problem solving, warranty
analysis, and other activities that arise during a products life cycle. Our customers receive
after-sales support in the form of special field service kits, service manuals, and specific
in-plant production repair programs.
The majority
of our OEM products are sold in North America. While a modest amount of exporting
is done to automotive assembly plants in Europe and South America, we are in the process of
expanding our presence in these markets and elsewhere through our Vehicle Access Systems Technology
(VAST) Alliance with WITTE-Automotive GmbH and ADAC Automotive, which is described in more detail
on page 8.
OEM service and replacement parts are sold to the OEMs own service operations. In
addition, we distribute our components and security products to the automotive aftermarket
through approximately 50 authorized wholesale distributors, as well as other marketers and
users of component parts, including export customers. Increasingly, our products find
their way into the retail channel, specifically the hardware store channel. Our ability to
provide a full line of keys to that channel has been accomplished through the introduction
of the STRATTEC XL key line. This extension to our line includes keys that we currently
do not supply on an OE basis, including keys for Toyota, Honda and other popular domestic
and import vehicles. This extended line of keys enable automotive repair specialists to
satisfy consumer needs for repair or replacement parts. Our aftermarket activities are
serviced through a warehousing operation integral to our Milwaukee headquarters and
manufacturing facility.
CUSTOMER FOCUS
To bring the proper focus to the relationships with our major customers, we have
seven customer-focused teams, each with a Director of Sales, a Product Business Manager,
one or two Engineering Program Managers and Customer Application Engineers. In addition to
customer teams for General Motors, Ford and Chrysler, we currently have teams for New
Domestic Vehicle Manufacturers, Driver Control/Ignition Lock Housing customers, Tiered
Products, and for Service and Aftermarket customers. In 2009, we will add a team for Power
Access Products.
Each Sales Director is responsible for the overall relationship between STRATTEC
and a specific customer group. Engineering Program Managers report to their respective
teams and are responsible for coordinating engineering resources and managing new
product programs for their customers.
To serve our customers product needs, STRATTECs engineering resources are organized
|
|
|
|
|
|
COMPANY DESCRIPTION
by product type. We currently have four product groups: Locks and Keys, Latches, Driver
Control/Ignition Lock Housings and Electrical. Assuming completion of the Delphi Power Products
acquisition described in this Annual Report, in 2009 we will be adding Power Access Devices,
including electronic control module capability. Each group has an Engineering Manager and a
complement of skilled engineers who design and develop products for specific applications. In doing
this, each engineering group works closely with the Product Business Managers, team Engineering
Program Managers, sales personnel and application engineers.
Underlying this organization is a formalized product development process to identify and meet
customer needs in the shortest possible time. By following this streamlined development system, we
shorten product lead times, tighten our response to market changes and provide our customers with
the optimum value solution to their security/access control requirements. STRATTEC is also ISO/TS
16949 and ISO 14001 certified. This means we embrace the philosophy that quality should exist not
only in the finished product, but in every step of our processes as well.
OPERATIONS
A significant number of the components that go into our products are manufactured at our main
facility and headquarters in Milwaukee, Wisconsin. This facility produces zinc die cast components,
stampings and key blanks. Key finishing takes place at STRATTEC Componentes Automotrices in Juarez,
Mexico along with assembly activities for ADAC-STRATTEC de Mexico. The majority of our assembly
operations take place at STRATTEC de Mexico, also located in Juarez. Warehousing and distribution
of aftermarket product is accomplished at the Milwaukee facility.
ADVANCED DEVELOPMENT
Research and development activities are centered around a dedicated research engineering staff
we call our Advanced Development Group. This group has the responsibility for developing future
products and processes that will keep us in the forefront of the markets we serve. Projects we are
pursuing focus on electronic and mechanical access control products, modularization of related
access/security control components and new manufacturing processes to reduce costs for ourselves
and our customers. Once our Advanced Development Group establishes a proof-of-concept product
utilizing new technology, further product development shifts to our engineering groups for
commercialization and product applications.
|
COMPANY DESCRIPTION
VAST ALLIANCE
In fiscal 2001, we entered into a formal Alliance with WITTE-Velbert GmbH, an
automotive supplier based in Germany, which designs, develops, manufactures and markets
automotive access control products for European-based customers. This Alliance consisted
of two initiatives. The first was a cross licensing agreement which allowed STRATTEC to
manufacture and market WITTEs core products in North America, and WITTE to manufacture
and market STRATTECs core products in Europe. The second initiative was a 50-50 joint
venture to invest in operations with local partners in strategic markets outside of Europe
and North America.
In February of 2006, we announced the expansion of the Alliance and related joint
venture with the addition of ADAC Plastics, Inc. ADAC, of Grand Rapids, Michigan adds
North American expertise in door handles, a part of WITTEs core product line that
STRATTEC did not support, and an expertise in color-matched painting of these components
which we believe is unique in the world.
With the expansion of the Alliance, we now have a full range of access control
related products available on a global basis to support customer programs. To identify
this powerful combination of independent companies focused on working together, we renamed
the joint venture Vehicle Access Systems Technology LLC, and the Alliance is now called
the VAST Alliance. WITTE is now called WITTE Automotive, and ADAC is now doing business as
ADAC Automotive. We have adopted a common graphic image in which we share a logo mark and
colors, and a specific logo for the Alliance itself to be used on the partners printed
and electronic presentation materials. Our VAST LLC partners in China and Brazil adopted
the name and image change so that VAST now truly has a global brand awareness.
ADAC-STRATTEC de MEXICO
During fiscal 2007, we formed a joint venture with ADAC Automotive called
ADAC-STRATTEC LLC including a wholly owned Mexican subsidiary ADAC-STRATTEC de MEXICO
(ASdM). The purpose of this joint venture is to produce certain ADAC and STRATTEC products
utilizing ADACs plastic molding expertise and STRATTECs assembly capability. ASdM
currently operates out of defined space in our STRATTEC Componentes Automotrices facility
in Juarez, Mexico. Initial products from this joint venture include door handle components
and
COMPANY DESCRIPTION
exterior trim components for customers producing in Mexico. Financial results for this
JV are consolidated into STRATTECs financial statements. As a start-up operaton, ASdM
had a minimal financial impact on STRATTECs fiscal 2007 and 2008 operating results.
However, beginning in our fiscal 2009, we expect there will be growing activity in this
joint venture.
SEASONAL NATURE OF THE BUSINESS
The manufacturing of components used in automobiles is driven by the normal peaks
and valleys associated with the automotive industry. Typically, the months of July and
August are relatively slow as summer vacation shutdowns and model year changeovers occur
at the automotive assembly plants. September volumes increase rapidly as the new model
year begins. This volume strength continues through October and into early November. As
the holiday and winter seasons approach, the demand for automobiles slows as does
production. March usually brings a major sales and production increase, which then
continues through most of June. This results in our first fiscal quarter (ending in
September) sales and operating results typically being our weakest, with the remaining
quarters being more consistent.
GLOBAL PRESENCE
1. STRATTEC Milwaukee, Wisconsin1
2. STRATTEC de Mexico Juarez, Mexico1
3. STRATTEC Componentes Automotrices Juarez, Mexico1
4. ADAC-STRATTEC de Mexico Juarez, Mexico
5. ADAC Automotive Grand Rapids and Muskegan, Michigan1
6. WITTE Automotive Velbert, Germany1
7. WITTE Automotive Nejdek, Czech Republic1
8.
VAST do Brasil Sao Paulo, Brazil 2
9.
VAST Fuzhou Fuzhou, China 2
10.
VAST Great Shanghai Co. Shanghai, China 2
11.
VAST Japan Tokyo, Japan (Branch Office) 2
12.
VAST Korea Anyang, Korea (Branch Office) 2
|
|
|
1
Members of the VAST Alliance. 2 Units of VAST LLC joint venture. |
ECONOMIC VALUE COMMITMENT
The underlying philosophy of our business, and the means by which we measure our
performance, is Economic Value Added (EVA®). Simply stated, economic value is
created when our business enterprise yields a return greater than the cost of capital we
and our shareholders have invested in STRATTEC. The amount by which our return exceeds the
cost of our capital is EVA®. In line with this philosophy, EVA®
bonus plans are in effect for all our U.S. associates, outside directors and many of
our Mexico-based salaried associates as an incentive to help positively drive the
business.
STRATTECs significant market presence is the result of a 100-year commitment to
creating quality products and systems that are responsive to changing needs. As
technologies advance and markets grow, STRATTEC retains that commitment to meeting and
exceeding the expectations of our customers, and providing economic value to our
shareholders.
VEHICLE LIST
2009 VEHICLES
We are proud to be associated with many of the quality vehicles produced in North America and
elsewhere. The following model year 2009 cars and light trucks are equipped with STRATTEC products.
CARS AND CARBASED UTILITY VEHICLES
Buick AllureChrysler PT CruiserJeep Compass
(Canada only) Chrysler SebringJeep Patriot
Buick EnclaveDodge AvengerLincoln MKS
Buick LaCrosseDodge CaliberLincoln Town Car
Buick LucerneDodge ChallengerMercury Grand Marquis
Cadillac XLRDodge ChargerMercury Sable
Cadillac CTSDodge JourneyOpel GT (Europe only)
Cadillac DTSDodge ViperPontiac G5
Cadillac SRXFord Crown VictoriaPontiac G6
Chevrolet CobaltFord MustangPontiac G8
Chevrolet EquinoxFord TaurusPontiac Solstice
Chevrolet CorvetteFord Taurus XPontiac Torrent
Chevrolet HHRGMC AcadiaSaturn Aura
Chevrolet ImpalaHolden CommodoreSaturn Outlook
Chevrolet Malibu (Australia only) Saturn Sky
Chevrolet TraverseHonda CivicSuzuki XL7
Chrysler 300/300CHyundai Veracruz
LIGHT TRUCKS, VANSAND SPORT UTILITYVEHICLES
Cadillac EscaladeDodge Ram PickupHyundai Entourage
Cadillac Escalade ESVFord ExpeditionJeep Commander
Cadillac Escalade EXTFord Expedition ELJeep Grand Cherokee
Chevrolet AvalancheFord ExplorerJeep Liberty
Chevrolet Express VanFord Explorer Sport TracJeep Wrangler/Wrangler
Chevrolet Silverado PickupFord F-Series PickupUnlimited
Chevrolet SuburbanFord F-Series SupercrewKia Sedona
Chevrolet TahoeFord F-Series Super DutyLincoln Navigator
Chevrolet TrailblazerFord Ranger PickupLincoln Navigator L
Chrysler AspenGMC EnvoyMazda B-Series Pickup
Chrysler Town & CountryGMC SavanaMercury Mountaineer
Dodge Grand CaravanGMC Sierra PickupNissan Titan
Dodge Dakota PickupGMC YukonSaab 9-7X
Dodge DurangoGMC Yukon XLVolkswagen Routan
Dodge NitroHummer H2
2008 STRATTEC Annual Report |
MANAGEMENTS DISCUSSION AND ANALYSIS
The following Discussion and Analysis should be read in conjunction with STRATTEC
SECURITY CORPORATIONs Financial Statements and Notes thereto. Unless otherwise
indicated, all references to years or quarters refer to fiscal years or fiscal
quarters.
RESULTS OF OPERATIONS
2008 Compared to 2007
Net sales were $159.6 million in 2008 compared to $167.7 million in 2007. The lower
sales primarily resulted from a 12-week strike against a major supplier to General Motors
Corporation and a dramatic shift in vehicle demand by consumers. The strike, which
occurred over the last four weeks of our third quarter and eight weeks of our fourth
quarter, affected General Motors production, resulting in the temporary closure of
several vehicle plants we supply. These are normally high-volume production plants. Most
of these plants have been producing large pickup trucks and SUVs. During our fourth
quarter gasoline prices reached and then exceeded $4.00 per gallon, significantly
accelerating a shift in consumer preferences away from large vehicles. The resulting glut
of large vehicles at retail outlets has caused all of our major customers to re-align
their production schedules and mix, emphasizing smaller vehicles. The volume of vehicles
produced by our customers during this re-alignment has declined, resulting in lower sales
and production. While the effect of the strike was a one-time event, we believe the
re-alignment of production to reflect changing consumer preferences is a long-term issue.
With this outlook for the industry, and overall weakness in the US economy, we expect to
experience reduced sales levels and operating results for our traditional business over
the next fiscal year.
Sales to our largest customers overall decreased in 2008 as compared to 2007. Sales
to General Motors increased to $45.0 million in the current year from $35.7 million in the
prior year. The increase was due to higher product content on certain General Motors
vehicles, the takeover of certain passenger car lockset production from another supplier
and price adjustments received to partially recover raw material cost increases, which we
experienced last year. These increases were partially offset by production reductions as a
direct result of a strike called by the UAW against a major General Motors supplier and
lower vehicle production volumes for trucks and SUVs. Sales to Ford Motor Company were
$19.4 million during 2008 compared to $21.0 million during 2007 due to lower Ford vehicle
production volumes. Sales to Chrysler LLC decreased to $40.2 million during the current
year from $58.1 million during the prior year due to a combination of reduced component
content in the products we supply and lower vehicle production volumes. Sales to Delphi
Corporation were $14.9 million during 2008 compared to $18.4 million during 2007. This
decrease was primarily due to reduced component content and lower production volumes,
somewhat offset by price adjustments received to partially recover raw material cost
increases experienced last year. The impact of the above mentioned strike reduced sales to
General Motors and Delphi Corporation by approximately $3.5 million in our current year.
Sales of ignition lock housings to other Tier 1 suppliers increased $4.3 million in the
current year compared to the prior year. Sales related to our joint venture with ADAC
Automotive totaled $5.2 million in the current year, which includes $3.3 million of sales
to our largest customers discussed above. This joint venture was not in full operation
during all of 2007.
Gross profit as a percentage of net sales was 16.0 percent in the current year
compared to 15.8 percent in the prior year. The gross profit margin was favorably impacted
by lower purchased raw material costs for zinc, cost reductions resulting from the move of
our service product assembly operation from our Milwaukee, Wisconsin facility to our
Juarez, Mexico facilities and price increases received from some of our customers to
recover the higher purchased raw material costs we experienced last year as discussed
above in connection with our net sales. In addition, the prior year included a charge for
severance and separation costs related to the service product assembly operation move
which reduced the gross profit margin by $366,000. The move of the service product
assembly operation took place in January 2007. The overall increase in the gross profit
margin was mostly offset by reductions
in our customers vehicle production volumes during the last six months of 2008 which
lowered overhead absorption of our manufacturing costs. In addition, the current year
included a lump sum bonus totaling $243,000 paid to our Milwaukee represented hourly
workers resulting from a new four-year labor contract ratified on June 22, 2008 as well as
the disposal of a customer specific fixed asset resulting in a fixed asset disposal loss
of $382,000. The average zinc price paid per pound decreased to $1.53 in the current year
from $1.77 in the prior year. During the current year, we used approximately 7.7 million
pounds of zinc. This resulted in decreased zinc costs of approximately $1.8 million in the
current year compared to the prior year.
MANAGEMENTS DISCUSSION AND ANALYSIS
Engineering, selling and administrative expenses were $24.0 million in 2008 compared
to $20.2 million in 2007. The increased expense was attributed to hiring additional
engineers to support new product development and new customer programs that are currently
under launch.
Income from operations decreased to $1.6 million in 2008 from $6.3 million in
2007. This decrease was primarily the result of reductions in our net sales and
increases in our operating expenses as discussed above.
Other income, net, decreased $485,000 to $230,000 in 2008. The reduction was
primarily due to a loss of $174,000 related to our Rabbi Trust during 2008 compared to a
gain of $450,000 in 2007. The Rabbi Trust funds our supplemental executive retirement
plan. In addition, the gain generated from our joint ventures increased to $561,000 during
2008 from $394,000 during 2007.
Our effective tax rate in both the current year and prior year was not our normal
effective income tax rate of 37.0 percent. Our effective income tax rate for 2008 was
27.3 percent compared to 23.6 percent in 2007. The 2008 provision included a favorable
tax adjustment primarily related to Mexican tax benefits allowed for our Mexican
subsidiaries. The favorable adjustment totaled $573,000. In addition, reduced 2008
earnings resulted in a larger percentage of our consolidated taxable income being taxed
in Mexico, which has a lower effective rate as compared to the US rate. The 2007
provision included a state refund claim recovery and a favorable tax adjustment primarily
related to foreign tax adjustments. The claim recovery, net of the Federal income tax
impact, was $329,000. The favorable tax adjustment totaled $1.1 million.
RESULTS OF OPERATIONS
2007 Compared to 2006
Net sales were $167.7 million in 2007 compared to $181.2 million in 2006. Sales to
our largest customers overall declined in 2007 as compared to 2006. Sales to Chrysler LLC
were essentially flat between years at $58.1 million in 2007 compared to $58.6 million in
2006. Sales to General Motors Corporation were $35.7 million in 2007 compared to $32.9
million in 2006 due to a combination of higher product content on certain General Motors
vehicles, takeover of certain passenger car lockset production from another supplier and
price adjustments received to partially recover raw material cost increases. Sales to
Ford Motor Company were $21.0 million in 2007 compared to $27.3 million in 2006 due to
pre-programmed price reductions and lower Ford vehicle production volumes. Sales to Delphi
Corporation were $18.4 million in 2007 compared to $26.7 million in 2006 due primarily to
lower levels of production and lower component content. This was partially offset by
price adjustments received to partially recover raw material cost increases. Sales to
Mitsubishi Motor Manufacturing of America, Inc. were $1.9 million in 2007 compared to
$5.4 million in 2006 due to the previously announced phase-out of this customer
relationship. The impact of the reduction in sales to our largest customers was partially
offset by increased sales to our industrial and aftermarket customers. The sales increase
to our industrial and aftermarket customers was primarily due to increased volumes and
price adjustments received from some of these customers to partially recover raw material
cost increases.
Gross profit as a percentage of net sales was 15.8 percent in 2007 compared to 20.4
percent in 2006. The lower profitability in 2007 was primarily the result of higher
purchased raw material costs for zinc and brass, the primary raw materials used in our
business. The 2006 gross margin also included a $580,000 customer reimbursement received
and recorded in 2006 relating to production capacity constraint issues expensed during
2005. The 2007 gross profit impact of the increased zinc and brass costs was partially
offset by price adjustments received from some of our customers to recover a portion of
the material cost
increases as discussed above in connection with our net sales. In addition, cost
reduction activities, including the move of our service products assembly operation from
our Milwaukee, Wisconsin facility to our Juarez, Mexico facilities, further reduced the
impact of the 2007 increased raw material costs. The increased raw material costs and the
related price adjustments from our customers reduced gross margins by approximately 3.3
percent in 2007 as compared to 2006. The average zinc price paid per pound increased to
$1.77 in 2007 from $1.01 in 2006. During 2007, we used approximately 8.3 million pounds of
zinc. This resulted in increased zinc costs of approximately $6.3 million in 2007 over
2006. The average brass price paid per pound increased to $3.74 in 2007 from $2.81 in
2006. During 2007, we used approximately 1.3 million pounds of brass. This resulted in
increased brass costs of approximately $1.2 million in 2007 over 2006. Total price
adjustments received from some of our customers to partially cover these cost increases,
which are reflected in our net
MANAGEMENTS DISCUSSION AND ANALYSIS
sales, totaled approximately $2.5 million in 2007.
Engineering, selling and administrative expenses were $20.2 million in 2007,
compared to $22.1 million in 2006. This reduction was primarily the result of reduced
spending in new product development, reduced benefit costs primarily related to the
actuarially calculated pension expense and reduced bonus expense, and reduced stock-based
compensation expense resulting from previously issued stock options becoming fully
vested. No additional stock options were issued during fiscal 2007.
The provision for bad debts of $1.6 million in 2006 reflects a write-off of
uncollectible pre-petition Chapter 11 accounts receivable due from Delphi Corporation.
During 2006, approximately $3.4 million of pre-petition Chapter 11 accounts receivable
due from Delphi Corporation were sold to a third party for $1.8 million.
Income from operations decreased to $6.3 million in 2007 from $13.4 million in 2006.
This decrease was primarily the result of reductions in our net sales and gross profit
margins as discussed above.
Other income, net, decreased to $715,000 in 2007 from $960,000 in 2006. The
decrease was primarily due to a decrease in transaction gains related to foreign
currency transactions entered into by our Mexican subsidiaries.
Our effective income tax rate for 2007 was 23.6 percent compared to 26.1 percent in
2006. The 2007 provision included a state refund claim recovery and a favorable tax
adjustment primarily related to foreign tax adjustments. The claim recovery, net of the
Federal income tax impact, was $329,000. The favorable tax adjustment totaled $1.1
million. The 2006 income tax provision included a state refund claim recovery and a
favorable state income tax adjustment. The 2006 claim recovery and tax adjustment, net of
the Federal income tax impact, was approximately $1.2 million. The 2006 income tax
provision also includes a favorable foreign tax adjustment related to the operation of our
Mexican subsidiaries of $664,000.
LIQUIDITY AND CAPITAL RESOURCES
Cash flow generated from operating activities was $3.8 million in 2008 compared to
$9.8 million in 2007. The change in cash flow generated from operating activities was
mostly impacted by overall financial results, an increase in LIFO inventory balances
during the current year compared to a reduction during 2007 and pension contributions. Net
income adjusted for non-cash items such as depreciation and stock-based compensation
expense decreased $3.3 million between years. Inventory balances increased $3.1 million
during 2008 compared to a decrease of $2.2 million during 2007. The current year increase
was due to the industry slowdown and to the new operation of ADAC-STRATTEC LLC. The 2007
decrease in inventory balances was the result of a concentrated effort to manage
inventories at lower levels. Pension contributions to our qualified plan totaled $5.0
million in 2008 compared to $7.0 million in 2007.
Our accounts receivable balance decreased $3.4 million in 2008 and decreased $1.4
million in 2007. The 2008 decrease was primarily due to the sales decrease experienced in
2008. The 2007 decrease was primarily due to a reduction in outstanding customer tooling
billings.
Our prepaid pension obligations relate to our qualified pension plan. The balance
decreased $3.6 million during 2008 and decreased $6.0 million during 2007. The reductions
are the result of the net impact of pension contributions, the actuarially calculated
pension expense for each year and the impact of the recognition of the funded status of
the plan. The pre-tax funded status adjustment reduced our prepaid pension obligations by $7.8
million at June 29, 2008 and by $11.7 million at July 1, 2007.
Capital expenditures were $10.9 million in 2008 compared to $5.7 million in 2007.
Expenditures were primarily in support of requirements for new product programs, the
upgrade and replacement of existing equipment and the construction of a new building in
Juarez, Mexico to replace our existing leased facility.
Our Board of Directors has authorized a stock repurchase program to buy back
outstanding shares of our common stock. Shares authorized for repurchase under the
program totaled 3,639,395 at June 29, 2008. On August 19, 2008 our Board of Directors
authorized an additional 200,000 shares for repurchase under the program. Over the life
of the repurchase program through June 29, 2008, a total of 3,461,333 shares have been
repurchased at a cost of approximately $130.2 million. Subsequent to June 29, 2008, an
additional 172,500 shares were repurchased at a cost of approximately $5.7 million.
Additional repurchases may occur from time to time and are expected to continue to be
funded by cash flow from operations and current cash balances.
We have a $50.0 million unsecured line of credit (the Line of Credit), which expires
MANAGEMENTS DISCUSSION AND ANALYSIS
October 31, 2008. There were no outstanding borrowings under the Line of Credit at June
29, 2008 or at July 1, 2007. Interest on borrowings under the Line of Credit are at
varying rates based on the London Interbank Offering Rate or the banks prime rate. We
believe the Line of Credit is adequate, along with cash flow from operations, to meet our
anticipated capital expenditure, working capital and operating expenditure requirements.
Over the past two years, we have been impacted by rising health care costs, which
have increased our cost of employee medical coverage. We have also been impacted by
increases in the market price of zinc, brass and magnesium and inflation in Mexico,
which impacts the U.S. dollar costs of our Mexican operations. We do not hedge against
our Mexican peso exposure.
CONTRACTUAL OBLIGATIONS
Contractual obligations are as follows as of June 29, 2008 (thousands of dollars):
|
|
|
|
|
|
|
|
|
|
|
|
|
|
|
|
|
|
|
|
|
|
|
Payments Due By Period |
|
|
|
|
|
|
Less Than |
|
|
|
|
|
|
|
|
|
More Than |
Contractual Obligation |
|
Total |
|
1 Year |
|
1-3 Years |
|
3-5 Years |
|
5 Years |
|
Operating Leases |
|
|
$ 1,621 |
|
|
|
$ 478 |
|
|
|
$ 554 |
|
|
|
$383 |
|
|
|
$206 |
|
Capital Purchase Obligations |
|
|
5,422 |
|
|
|
5,422 |
|
|
|
|
|
|
|
|
|
|
|
|
|
Other Purchase Obligations |
|
|
11,900 |
|
|
|
10,090 |
|
|
|
1,810 |
|
|
|
|
|
|
|
|
|
Pension and Postretirement
Obligations (a) |
|
|
4,182 |
|
|
|
4,182 |
|
|
|
|
|
|
|
|
|
|
|
|
|
|
|
|
|
|
|
|
|
|
|
|
|
|
|
|
|
|
|
|
|
|
Total |
|
|
$23,125 |
|
|
|
$20,172 |
|
|
|
$2,364 |
|
|
|
$383 |
|
|
|
$206 |
|
|
|
|
|
|
|
|
|
|
|
|
|
|
|
|
|
|
|
|
|
|
(a) As disclosed in our Notes to Financial Statements, estimated cash funding
related to our pension and postretirement benefit plans totals $4.2 million in 2009.
Because the timing of funding related to these plans beyond 2009 is uncertain, and is
dependent on future movements in interest rates and investment returns, changes in laws
and regulations, and other variables, pension and postretirement outflows beyond 2009 have
not been included in the table above.
Liabilities recognized for uncertain tax benefits of $1.2 million are not presented
in the table above due to uncertainty as to amounts and timing regarding future
payments.
JOINT VENTURES
We participate in certain Alliance Agreements with WITTE Automotive (WITTE) and
ADAC Automotive (ADAC). WITTE, of Velbert, Germany, is a privately held automotive
supplier. WITTE designs, manufactures and markets components including locks and keys,
hood latches, rear compartment latches, seat back latches, door handles and specialty
fasteners. WITTEs primary market for these products has been Europe. ADAC, of Grand
Rapids, Michigan, is a privately held automotive supplier and manufactures engineered
products, including door handles and other automotive trim parts, utilizing plastic
injection molding, automated painting and various assembly processes.
The Alliance provides a set of cross-licensing agreements for the manufacture,
distribution and sale of WITTE products by STRATTEC and ADAC in North America, and the
manufacture, distribution and sale of STRATTEC and ADAC products by WITTE in Europe.
Additionally, a joint venture company, Vehicle Access Systems Technology LLC (VAST
LLC), in which WITTE, STRATTEC and ADAC each hold a one-third interest, exists to seek
opportunities to manufacture and sell the companies products in areas of the world
outside of North America and Europe.
VAST LLC participates in joint ventures in Brazil and China. VAST do Brasil, a
joint venture between VAST LLC and Ifer do Brasil Ltda., was formed to service customers
in South America. VAST Fuzhou and VAST Great Shanghai, joint ventures between VAST
LLC, Fortitude Corporation and a unit of Elitech Technology Co. Ltd. of Taiwan, are
the base of operations to service our automotive customers in the Asian market.
The VAST investments are accounted for using the equity method of accounting. The
activities related to the VAST joint ventures resulted in a gain of approximately
$561,000 in 2008 and $394,000 in 2007. A capital contribution of $100,000 was made to the
VAST LLC joint venture in 2007 primarily in support of general operating expenses. No
capital contributions were made in 2008.
In 2007, we entered into a joint venture with ADAC, in which STRATTEC holds a 50.1
percent interest and ADAC holds a 49.9 percent interest. The joint venture was created
to establish injection molding and door handle assembly operations in Mexico.
ADAC-STRATTEC LLC, a Delaware limited liability company, was formed on October 27, 2006.
An additional Mexican entity, ADAC-STRATTEC de Mexico, which is wholly owned by
ADAC-STRATTEC LLC, was formed on February 21, 2007. ADAC-STRATTEC de Mexico production
activities began in July 2007. ADAC-STRATTEC LLCs financial results are consolidated
with the financial results of STRATTEC and resulted in increased net income to STRATTEC
of $26,000 in 2008 and reduced
MANAGEMENTS DISCUSSION AND ANALYSIS
net income of $75,000 in 2007.
In combination with WITTE and VAST LLC, we have reached a definitive agreement to
acquire certain assets, primarily equipment and inventory, and assume certain employee
liabilities of Delphi Corporations Power Products business for $7.8 million, subject to
closing agreements. SRATTEC will acquire the North American portion of Delphis Power
Products business. WITTE will participate in the North American portion as a minority
investor. WITTE will acquire the European portion and VAST LLC will acquire the Asian
portion. The transaction is subject to both customary and other closing conditions
relating to Delphis bankruptcy court proceedings. We expect to complete the transaction
before the end of calendar year 2008.
Delphis Power Products business designs, develops, tests, manufactures, markets and
sells power systems to operate vehicle sliding doors, and rear compartment access points
such as liftgates and trunk lids. In addition, the product line includes power cinching
latches and power cinching strikers used in these systems. Current customers for these
products supplied from North America include Chrysler LLC, Hyundai/Kia Motor Company,
General Motors Corporation and Ford Motor Company.
RECENTLY ISSUED ACCOUNTING STANDARDS
In December 2007, the Financial Accounting Standards Board (FASB) issued Statement
of Financial Accounting Standards (SFAS) No. 160, Noncontrolling Interests in
Consolidated Financial Statements an amendment to ARB No. 51. SFAS No. 160
establishes accounting and reporting standards that require the ownership interest in
subsidiaries held by parties other than the parent be clearly identified and presented in
the consolidated balance sheets within equity, but separate from the parents equity, the
amount of consolidated net income attributable to the parent and the noncontrolling
interest be clearly identified and presented on the face of the consolidated statements
of income, and changes in a parents ownership interest while the parent retains its
controlling financial interest in its subsidiary be accounted for consistently. This
statement is effective for fiscal years beginning after December 15, 2008 and will be
effective for us beginning in fiscal 2010. We do not expect the new standard to have a
material impact on our financial position or results of operations.
In December 2007, the FASB issued SFAS No. 141(R), Business Combinations. SFAS No.
141(R) retains the underlying concepts of SFAS No. 141 in that all business combinations
are required to be accounted for at fair value under the acquisition method of accounting,
but SFAS No. 141(R) changed the method of applying the acquisition method in a number of
aspects. SFAS No. 141(R) will require that (1) for all business combinations, the acquirer
records all assets and liabilities of the acquired business, including goodwill, generally
at their fair values; (2) certain contingent assets and liabilities acquired be recognized
at their fair value on the acquisition date; (3) contingent consideration be recognized at
its fair value on the acquisition date and, for certain arrangements, changes in fair
value will be recognized in earnings when settled; (4) acquisition related transaction and
restructuring costs be expensed rather than treated as part of the cost of the acquisition
and included in the amount recorded for assets acquired; (5) in step acquisitions,
previous equity interests in an acquiree held prior to obtaining control be remeasured to
their acquisition date fair values, with any gain or loss recognized in earnings; and (6)
when making adjustments to finalize initial accounting, companies revise any previously
issued post-acquisition financial information in future financial statements to reflect
any adjustments as if they had been recorded on the acquisition date. SFAS No. 141(R) is
effective on a prospective basis for all business combinations for which the acquisition
date is on or after the beginning of the first annual period subsequent to December 15,
2008, with the exception of the accounting for valuation allowances on deferred taxes and
acquired tax contingencies. SFAS No. 141(R) amends SFAS No. 109 such that the adjustments
made to valuation allowances on deferred taxes and acquired tax contingencies
associated with acquisitions that closed prior to the effective date of this
statement should also apply the provisions of SFAS No. 141(R). This standard will be
applied to all future business combinations in accordance with the effective dates.
CRITICAL ACCOUNTING POLICIES
We believe the following represents our critical accounting policies:
Pension
and Postretirement Health Benefits Pension and postretirement health
obligations and costs are developed from actuarial valuations. The determination of the
obligation and expense for pension and postretirement health benefits is dependent on the
selection of certain assumptions used by actuaries in calculating such amounts. Those
assumptions are described in the Notes to Financial Statements and include, among others,
the discount rate, expected long-term rate of return on plan assets, retirement age and
rates of increase in compensation and health care costs. We evaluate and update all of the
assumptions annually on June 30, the measurement date. Refer to Notes to Financial
Statements for the impact of the pension and postretirement plans on the financial
statements.
We determine the discount rate used to measure plan liabilities using prevailing
market rates of a large population of high-quality, non-callable, corporate bonds
currently available that, if the obligation was settled at the measurement date, would
provide the necessary future cash
MANAGEMENTS DISCUSSION AND ANALYSIS
flows to pay the benefit obligation when due. Using this methodology, we determined a
discount rate of 7.13 percent to be appropriate as of June 30, 2008, which is an increase
of .72 percentage points from the rate used at June 30, 2007. The impact of this change
decreased our year-end 2008 projected pension benefit obligations by approximately $6.5
million, the year-end 2008 accumulated pension benefit obligations by approximately $5.7
million and the year-end 2008 accumulated postretirement obligation by approximately
$415,000. This change is also expected to decrease our 2009 pension expense by $700,000
and postretirement expense by $12,000.
As of June 30, 2008, we increased the assumed probability of early retirement for
eligible associates with at least 30 years of service. The impact of this change
increased our year-end 2008 projected pension benefit obligations by approximately $2.2
million, the year-end 2008 accumulated pension benefit obligations by approximately $2.8
million and the year-end 2008 accumulated postretirement obligation by approximately
$470,000. This change is also expected to increase our 2009 pension expense by $370,000
and postretirement expense by $120,000.
As of June 30, 2005, we converted to the RP (Retirement Plans) 2000 Mortality Table
for calculating the year-end 2005 pension and postretirement obligations and 2006 expense.
The impact of this change increased our 2006 pension expense by $250,000 and
postretirement expense by $17,000. As of June 30, 2007, we converted to the RP 2000
Mortality Table projected to 2014 for annuitants and 2022 for non-annuitants for
calculating the year-end 2007 pension and postretirement obligations. The impact of this
change increased our year-end 2007 projected pension benefit obligations by $2.4 million,
the year-end 2007 accumulated pension benefit obligations by $2.1 million and the year-end
2007 accumulated postretirement obligation by $85,000. This change increased our 2008
pension expense by $462,000 and postretirement expense by $10,000.
A significant element in determining the pension expense in accordance with SFAS No.
87 and SFAS No. 158 is the expected return on plan assets. Our assumption for the expected
return on plan assets is based on historical results for similar allocations among asset
classes and was 8.5 percent for 2008 and will be reduced to 8.25 percent for 2009. This
will reduce the expected return on plan assets by approximately $200,000 in 2009. Refer to
Notes to Financial Statements for additional information on how this rate was determined.
The difference between the expected return and actual return on plan assets is
deferred and, under certain circumstances, amortized over future years of service.
Therefore, the deferral of past asset gains and losses ultimately affects future pension
expense. This is also the case with changes to actuarial assumptions. As of June 30, 2008,
we had $18.4 million of net unrecognized pension actuarial losses, which includes deferred
asset losses of $7.9 million. As of June 30, 2008, we had unrecognized postretirement
actuarial losses of $10.3 million. These amounts represent potential future pension and
postretirement expenses that would be amortized over average future service periods. The
average remaining service period is about 11 years for the pension plans and 13 years for
the postretirement plan.
During fiscal years 2008, 2007 and 2006, we contributed $5 million, $7 million and $6
million, respectively, to our qualified pension plan. Future pension contributions are
expected to be $2 to $3 million annually depending on market conditions. We have evaluated
the potential impact of the Pension Protection Act (the Act), which was passed into law
on August 17, 2006, on future pension plan funding requirements based on current market
conditions. The Act is not anticipated to have a material effect on our level of future
funding requirements or on our liquidity and capital resources.
A significant element in determining the postretirement health expense in accordance
with SFAS No. 106 is the health care cost trend rates. We develop these rates based on
historical cost data, the near-term outlook and an assessment of likely long-term trends.
Changes in the health care cost trend rate assumption will have a significant effect
on the postretirement benefit amounts reported. Refer to Notes to Financial Statements
for an analysis of the impact of a one percent change in the trend rate.
While we believe that the assumptions used are appropriate, significant differences
in the actual experience or significant changes in the assumptions may materially affect
our pension and postretirement health obligations and future expense.
Other
Reserves We have reserves such as an environmental reserve, an incurred
but not reported claim reserve for self-insured health plans, a workers compensation
reserve, an allowance for doubtful accounts related to trade accounts receivable and a
repair and maintenance supply parts reserve. These reserves require the use of
estimates and judgment with regard to risk exposure, ultimate liability and net
realizable value. We believe such reserves are estimated using consistent and
appropriate methods. However, changes to the assumptions could materially affect the
recorded reserves.
Stock-Based
Compensation We account for stock-based compensation in accordance
with SFAS No. 123(R), Share Based Payments. Under the fair value recognition provisions
of this statement, share-based compensation cost is measured at the grant date based on
the value of the award and is recognized as expense over the vesting period. Determining
the fair value of share-based awards at the grant date requires judgment, including
estimating future volatility of our stock, the amount of share-based awards that are
expected to be forfeited and
MANAGEMENTS DISCUSSION AND ANALYSIS
the expected term of awards granted. We estimate the fair value of stock options granted
using the Black-Scholes option valuation model. We amortize the fair value of all awards
on a straight-line basis over the vesting periods. The expected term of awards granted
represents the period of time they are expected to be outstanding. We determine the
expected term based on historical experience with similar awards, giving consideration to
the contractual terms and vesting schedules. We estimate the expected volatility of our
common stock at the date of grant based on the historical volatility of our common stock.
The volatility factor used in the Black-Scholes option valuation model is based on our
historical stock prices over the most recent period commensurate with the estimated
expected term of the award. We base the risk-free interest rate used in the Black-Scholes
option valuation model on the implied yield currently available on U.S. Treasury
zero-coupon issues with a remaining term commensurate with the expected term of the award.
We use historical data to estimate pre-vesting option forfeitures. We record stock-based
compensation only for those awards that are expected to vest. If actual results differ
significantly from these estimates, stock-based compensation expense and our results of
operations could be materially impacted.
RISK FACTORS
We understand we are subject to the following risk factors based on our
operations and the nature of the automotive industry in which we operate:
Loss of Significant Customers, Vehicle Content, Vehicle Models and Market Share
Sales to General Motors Corporation, Ford Motor Company, Chrysler LLC and Delphi
Corporation represent approximately 75 percent of our annual net sales. The contracts
with these customers provide for supplying the customers requirements for a particular
model. The contracts do not specify a specific quantity of parts. The contracts
typically cover the life of a model, which averages approximately four to five years.
Components for certain customer models may also be market tested annually. Therefore,
the loss of any one of these customers, the loss of a contract for a specific vehicle
model, reduction in vehicle content, early cancellation of a specific vehicle model,
technological changes or a significant reduction in demand for certain key models could
occur, and if so, could have a material adverse effect on our existing and future
revenues and net income.
Our major customers also have significant underfunded legacy liabilities related to
pension and postretirement health care obligations. The future impact of these items
along with a continuing loss in their North American automotive market share to the New
Domestic automotive manufacturers (primarily the Japanese automotive manufacturers) may
have a significant impact on our future sales and collectibility risks. For example, on
October 8, 2005, Delphi Corporation filed for Chapter 11 bankruptcy protection. As a
result, we wrote-off $1.6 million of uncollectible pre-petition Chapter 11 accounts
receivable due from Delphi Corporation. This directly reduced our pre-tax net income
during fiscal 2006.
Cost Reduction There is continuing pressure from our major customers to reduce the
prices we charge for our products. This requires us to generate cost reductions, including
reductions in the cost of components purchased from outside suppliers. If we are unable to
generate sufficient production cost savings in the future to offset pre-programmed price
reductions, our gross margin and profitability will be adversely affected.
Cyclicality and Seasonality in the Automotive Market The automotive market is
highly cyclical and is dependent on consumer spending and to a certain extent on customer
sales incentives. Economic factors adversely affecting consumer demand for automobiles and
automotive production, such as rising fuel costs, could adversely impact our net sales and
net income. We typically experience decreased sales and operating income during the first
fiscal quarter of each year due to the impact of scheduled customer plant shut-downs in
July and new model changeovers.
Foreign Operations As discussed under Joint Ventures, we have joint venture
investments in Mexico, Brazil and China. These operations are currently not material.
However, as these operations expand, their success will depend, in part, on our and
our partners ability to anticipate and effectively manage certain risks inherent in
international operations including: enforcing agreements and collecting receivables
through certain
foreign legal systems, payment cycles of foreign customers, compliance with
foreign tax laws, general economic and political conditions in these countries and
compliance with foreign laws and regulations.
Currency Exchange Rate Fluctuations We incur a portion of our expenses in
Mexican pesos. Exchange rate fluctuations between the U.S. dollar and the Mexican peso
could have an adverse effect on our financial results.
Sources of and Fluctuations in Market Prices of Raw Materials Our primary raw
materials are high-grade zinc, brass, magnesium, aluminum, steel and plastic resins. These
materials are generally available from a number of suppliers, but we have chosen to
concentrate our sourcing with one primary vendor for each commodity or purchased
component. We believe our sources of raw materials are reliable and adequate for our
needs. However, the development of future sourcing issues related to using existing or
alternative raw materials and the global availability of these materials as well as
significant fluctuations in the market prices of these materials may have
MANAGEMENTS DISCUSSION AND ANALYSIS
an adverse affect on our financial results if the increased raw material costs cannot
be recovered from our customers.
Disruptions Due to Work Stoppages and Other Labor Matters Our major customers and
many of their suppliers have unionized work forces. Work stoppages or slow-downs
experienced by our customers or their suppliers could result in slow-downs or closures of
assembly plants where our products are included in assembled vehicles. For example, a
strike by the United Auto Workers against a major General Motors Corporation supplier led
to extended shut-downs of several General Motors Corporations North American assembly
plants in March 2008. A material work stoppage experienced by one or more of our customers
could have an adverse effect on our business and our financial results. In addition, all
production associates at our Milwaukee facility are unionized. A sixteen-day strike by
these associates in June 2001 resulted in increased costs as all salaried associates
worked with additional outside resources to produce the components necessary to meet
customer requirements. The current contract with the unionized associates is effective
through June 30, 2012. We may encounter further labor disruption after the expiration date
of this contract and may also encounter unionization efforts in our other plants or other
types of labor conflicts, any of which could have an adverse effect on our business and
our financial results.
Environmental and Safety Regulations We are subject to Federal, state, local and
foreign laws and other legal requirements related to the generation, storage, transport,
treatment and disposal of materials as a result of our manufacturing and assembly
operations. These laws include the Resource Conservation and Recovery Act (as amended),
the Clean Air Act (as amended) and the Comprehensive Environmental Response, Compensation
and Liability Act (as amended). We have an environmental management system that is
ISO-14001 certified. We believe that our existing environmental management system is
adequate for current and anticipated operations and we have no current plans for
substantial capital expenditures in the environmental area. An environmental reserve was
established in 1995 for estimated costs to remediate a site at our Milwaukee facility. The
site was contaminated by a former above-ground solvent storage tank, located on the east
side of the facility. The contamination occurred in 1985. This is being monitored in
accordance with Federal, state and local requirements. We do not currently anticipate any
material adverse impact on our results of operations, financial condition or competitive
position as a result of compliance with Federal, state, local and foreign environmental
laws or other legal requirements. However, risk of environmental liability and changes
associated with maintaining compliance with environmental laws is inherent in the nature
of our business and there is no assurance that material liabilities or changes could not
arise.
Highly Competitive Automotive Supply Industry The automotive component supply
industry is highly competitive. Some of our competitors are companies, or divisions or
subsidiaries of companies, that are larger than STRATTEC and have greater financial and
technology capabilities. Our products may not be able to compete successfully with the
products of these other companies, which could result in loss of customers and, as a
result, decreased sales and profitability. Some of our major customers have also announced
that they will be reducing their supply base. This could potentially result in the loss of
these customers and consolidation within the supply base. The loss of any of our major
customers could have a material adverse effect on our existing and future net sales and
net income.
In addition, our competitive position in the North American automotive component
supply industry could be adversely affected in the event that we are unsuccessful in
making strategic acquisitions, alliances or establishing joint ventures that would enable
us to expand globally. We principally compete for new business at the beginning of the
development of new models and upon the redesign of existing models by our major customers.
New model development generally begins two to five years prior to the marketing of such
new models to the public. The failure to obtain new business on new models or to retain or
increase business on redesigned existing models could adversely affect our business and
financial results. In addition, as a result of relatively long lead times for many of our
components, it may be difficult in the short-term for us to obtain new sales to replace
any unexpected decline in the sale of existing products. Finally, we may incur significant
product development expense in preparing to meet anticipated customer requirements which
may not be recovered.
Program Volume and Pricing Fluctuations We incur costs and make capital
expenditures for new program awards based upon certain estimates of production volumes
over the anticipated program life for certain vehicles. While we attempt to establish the
price of our products for variances in production volumes, if the actual production of
certain vehicle models is significantly less than planned, our net sales and net income
may be adversely affected. We cannot predict our customers demands for the products we
supply either in the aggregate or for particular reporting periods.
Investments in Customer Program Specific Assets We make investments in machinery
and equipment used exclusively to manufacture products for specific customer programs.
This machinery and equipment is capitalized and depreciated over the expected useful life
of each respective asset. Therefore, the loss of any one of our major customers, the loss
of specific vehicle models or the early cancellation of a vehicle model could result in
impairment in the value of these assets and may have a material adverse effect on our
financial results.
CONSOLIDATED STATEMENTS OF INCOME
(IN THOUSANDS, EXCEPT PER SHARE AMOUNTS)
|
|
|
|
|
|
|
|
|
|
|
|
|
|
|
Years Ended |
|
|
June 29, 2008 |
|
|
July 1, 2007 |
|
|
July 2, 2006 |
|
|
|
|
|
|
|
|
|
|
|
|
|
|
NET SALES |
|
|
$ 159,642 |
|
|
|
$ 167,707 |
|
|
|
$ 181,197 |
|
Cost of goods sold |
|
|
134,091 |
|
|
|
141,213 |
|
|
|
144,151 |
|
|
|
|
|
|
|
|
|
|
|
|
|
|
|
|
|
|
|
|
|
|
|
|
|
|
|
GROSS PROFIT |
|
|
25,551 |
|
|
|
26,494 |
|
|
|
37,046 |
|
Engineering, selling, and administrative expenses |
|
|
23,962 |
|
|
|
20,189 |
|
|
|
22,067 |
|
Provision for doubtful accounts, net |
|
|
|
|
|
|
|
|
|
|
1,622 |
|
|
|
|
|
|
|
|
|
|
|
|
|
|
|
|
|
|
|
|
|
|
|
|
|
|
|
INCOME FROM OPERATIONS |
|
|
1,589 |
|
|
|
6,305 |
|
|
|
13,357 |
|
Interest income |
|
|
2,749 |
|
|
|
3,611 |
|
|
|
2,563 |
|
Interest expense |
|
|
|
|
|
|
|
|
|
|
|
|
Other income, net |
|
|
230 |
|
|
|
715 |
|
|
|
960 |
|
Minority interest |
|
|
(76 |
) |
|
|
75 |
|
|
|
|
|
|
|
|
|
|
|
|
|
|
|
|
|
|
|
|
|
|
|
|
|
|
|
|
|
|
|
INCOME BEFORE PROVISION FOR
INCOME TAXES |
|
|
4,492 |
|
|
|
10,706 |
|
|
|
16,880 |
|
Provision for income taxes |
|
|
1,225 |
|
|
|
2,523 |
|
|
|
4,403 |
|
|
|
|
|
|
|
|
|
|
|
|
|
|
|
|
|
|
|
|
|
|
|
|
|
|
|
NET INCOME |
|
|
$ 3,267 |
|
|
|
$ 8,183 |
|
|
|
$ 12,477 |
|
|
|
|
|
|
|
|
|
|
|
|
|
|
|
|
|
|
|
|
|
|
|
|
|
|
|
EARNINGS PER SHARE: |
|
|
|
|
|
|
|
|
|
|
|
|
BASIC |
|
|
$ 0.94 |
|
|
|
$ 2.30 |
|
|
|
$ 3.36 |
|
|
|
|
|
|
|
|
|
|
|
|
|
|
DILUTED |
|
|
$ 0.94 |
|
|
|
$ 2.30 |
|
|
|
$ 3.35 |
|
|
|
|
|
|
|
|
|
|
|
|
|
|
|
|
|
|
|
|
|
|
|
|
|
|
|
AVERAGE SHARES OUTSTANDING: |
|
|
|
|
|
|
|
|
|
|
|
|
BASIC |
|
|
3,487 |
|
|
|
3,552 |
|
|
|
3,716 |
|
DILUTED |
|
|
3,494 |
|
|
|
3,555 |
|
|
|
3,720 |
|
The accompanying Notes to Financial Statements are an integral part of these Consolidated Statements of Income.
CONSOLIDATED BALANCE SHEETS
(IN THOUSANDS, EXCEPT SHARE AMOUNTS AND PER SHARE AMOUNTS)
|
|
|
|
|
|
|
|
|
|
|
June 29, 2008 |
|
|
July 1, 2007 |
|
|
|
|
|
|
|
|
|
|
ASSETS |
|
|
|
|
|
|
|
|
CURRENT ASSETS: |
|
|
|
|
|
|
|
|
Cash and cash equivalents |
|
|
$ 51,501 |
|
|
|
$ 65,491 |
|
Receivables, less allowance for doubtful accounts
of $250 at June 29, 2008 and July 1, 2007 |
|
|
23,518 |
|
|
|
26,890 |
|
Inventories |
|
|
10,269 |
|
|
|
7,166 |
|
Customer tooling in progress |
|
|
3,914 |
|
|
|
1,824 |
|
Deferred income taxes |
|
|
3,252 |
|
|
|
2,729 |
|
Income taxes recoverable |
|
|
1,815 |
|
|
|
|
|
Other current assets |
|
|
8,997 |
|
|
|
8,464 |
|
|
|
|
|
|
|
|
|
|
Total current assets |
|
|
103,266 |
|
|
|
112,564 |
|
|
|
|
|
|
|
|
|
|
DEFERRED INCOME TAXES |
|
|
3,684 |
|
|
|
2,117 |
|
INVESTMENT IN JOINT VENTURES |
|
|
3,642 |
|
|
|
2,813 |
|
PREPAID PENSION OBLIGATIONS |
|
|
758 |
|
|
|
4,385 |
|
OTHER LONG-TERM ASSETS |
|
|
27 |
|
|
|
41 |
|
PROPERTY, PLANT AND EQUIPMENT, NET |
|
|
30,336 |
|
|
|
26,526 |
|
|
|
|
|
|
|
|
|
|
|
|
|
$141,713 |
|
|
|
$148,446 |
|
|
|
|
|
|
|
|
|
|
|
|
|
|
|
|
|
|
|
LIABILITIES AND SHAREHOLDERS EQUITY |
|
|
|
|
|
|
|
|
CURRENT LIABILITIES: |
|
|
|
|
|
|
|
|
Accounts payable |
|
|
$ 15,974 |
|
|
|
$ 16,575 |
|
Accrued liabilities: |
|
|
|
|
|
|
|
|
Payroll and benefits |
|
|
7,319 |
|
|
|
6,280 |
|
Environmental |
|
|
2,648 |
|
|
|
2,655 |
|
Income taxes |
|
|
|
|
|
|
664 |
|
Other |
|
|
6,998 |
|
|
|
5,307 |
|
|
|
|
|
|
|
|
|
|
Total current liabilities |
|
|
32,939 |
|
|
|
31,481 |
|
|
|
|
|
|
|
|
|
|
COMMITMENTS AND CONTINGENCIES see note on page 28 |
|
|
|
|
|
|
|
|
|
|
|
|
|
|
|
|
|
BORROWINGS UNDER LINE OF CREDIT |
|
|
|
|
|
|
|
|
ACCRUED PENSION OBLIGATIONS |
|
|
2,606 |
|
|
|
2,855 |
|
ACCRUED POSTRETIREMENT OBLIGATIONS |
|
|
9,783 |
|
|
|
10,576 |
|
MINORITY INTEREST |
|
|
953 |
|
|
|
574 |
|
SHAREHOLDERS EQUITY: |
|
|
|
|
|
|
|
|
Common stock, authorized 12,000,000 shares, $.01 par value,
issued 6,887,757 shares at June 29, 2008 and at July 1, 2007 |
|
|
69 |
|
|
|
69 |
|
Capital in excess of par value |
|
|
78,885 |
|
|
|
78,122 |
|
Retained earnings |
|
|
163,889 |
|
|
|
165,928 |
|
Accumulated other comprehensive loss |
|
|
(17,495 |
) |
|
|
(14,341 |
) |
Less: Treasury stock at cost (3,444,548 shares at
June 29, 2008 and 3,368,619 shares at July 1, 2007) |
|
|
(129,916 |
) |
|
|
(126,818 |
) |
|
|
|
|
|
|
|
|
|
Total shareholders equity |
|
|
95,432 |
|
|
|
102,960 |
|
|
|
|
|
|
|
|
|
|
|
|
|
$141,713 |
|
|
|
$148,446 |
|
|
|
|
|
|
|
|
|
|
The Accompanying Notes to Financial Statements are an integral part of these Consolidated Balance Sheets.
CONSOLIDATED STATEMENTS OF
SHAREHOLDERS EQUITY (IN THOUSANDS, EXCEPT PER SHARE AMOUNTS)
|
|
|
|
|
|
|
|
|
|
|
|
|
|
|
|
|
|
|
|
|
|
|
|
|
|
|
|
|
|
|
|
|
|
|
|
|
|
|
Accumulated |
|
|
|
|
|
|
|
|
|
|
Capital in |
|
|
|
|
|
Other |
|
|
|
|
|
|
Common |
|
Excess of |
|
Retained |
|
Comprehensive |
|
Treasury |
|
Comprehensive |
|
|
Stock |
|
Par Value |
|
Earnings |
|
Loss |
|
Stock |
|
Income |
|
|
|
|
|
|
|
|
|
|
|
|
|
|
|
|
|
|
|
|
|
|
|
|
|
|
|
|
BALANCE JULY 3, 2005 |
|
|
$69 |
|
|
|
$74,924 |
|
|
|
$145,268 |
|
|
|
$(12,047 |
) |
|
|
$(116,463 |
) |
|
|
|
|
|
|
|
|
|
|
|
|
|
|
|
|
|
|
|
|
|
|
|
|
|
|
|
|
|
Net Income |
|
|
|
|
|
|
|
|
|
|
12,477 |
|
|
|
|
|
|
|
|
|
|
|
$12,477 |
|
Translation adjustments |
|
|
|
|
|
|
|
|
|
|
|
|
|
|
(317 |
) |
|
|
|
|
|
|
(317 |
) |
Minimum pension liability,
net of tax of $5,765 |
|
|
|
|
|
|
|
|
|
|
|
|
|
|
9,406 |
|
|
|
|
|
|
|
9,406 |
|
|
|
|
|
|
|
|
|
|
|
|
|
|
|
|
|
|
|
|
|
|
|
|
|
|
Comprehensive income |
|
|
|
|
|
|
|
|
|
|
|
|
|
|
|
|
|
|
|
|
|
|
$21,566 |
|
|
|
|
|
|
|
|
|
|
|
|
|
|
|
|
|
|
|
|
|
|
|
|
|
|
Purchase of common stock |
|
|
|
|
|
|
|
|
|
|
|
|
|
|
|
|
|
|
(5,306 |
) |
|
|
|
|
Stock-Based Compensation |
|
|
|
|
|
|
1,118 |
|
|
|
|
|
|
|
|
|
|
|
|
|
|
|
|
|
Exercise of stock options
and employee stock
purchases, including
tax benefit of $62 |
|
|
|
|
|
|
1,133 |
|
|
|
|
|
|
|
|
|
|
|
13 |
|
|
|
|
|
|
|
|
|
|
|
|
|
|
|
|
|
|
|
|
|
|
|
|
|
|
|
|
|
|
|
|
|
|
|
|
|
|
|
|
|
|
|
|
|
|
|
|
|
|
|
|
|
|
|
BALANCE JULY 2, 2006 |
|
|
$69 |
|
|
|
$77,175 |
|
|
|
$157,745 |
|
|
|
$ (2,958 |
) |
|
|
$(121,756 |
) |
|
|
|
|
|
|
|
|
|
|
|
|
|
|
|
|
|
|
|
|
|
|
|
|
|
|
|
|
|
Net Income |
|
|
|
|
|
|
|
|
|
|
8,183 |
|
|
|
|
|
|
|
|
|
|
|
8,183 |
|
Translation adjustments |
|
|
|
|
|
|
|
|
|
|
|
|
|
|
449 |
|
|
|
|
|
|
|
449 |
|
Minimum pension liability,
net of tax of $14 |
|
|
|
|
|
|
|
|
|
|
|
|
|
|
24 |
|
|
|
|
|
|
|
24 |
|
|
|
|
|
|
|
|
|
|
|
|
|
|
|
|
|
|
|
|
|
|
|
|
|
|
Comprehensive income |
|
|
|
|
|
|
|
|
|
|
|
|
|
|
|
|
|
|
|
|
|
|
$ 8,656 |
|
|
|
|
|
|
|
|
|
|
|
|
|
|
|
|
|
|
|
|
|
|
|
|
|
|
Purchase of common stock |
|
|
|
|
|
|
|
|
|
|
|
|
|
|
|
|
|
|
(5,075 |
) |
|
|
|
|
Stock-Based Compensation |
|
|
|
|
|
|
698 |
|
|
|
|
|
|
|
|
|
|
|
|
|
|
|
|
|
Exercise of stock options
and employee stock
purchases, including tax
benefit of $69 |
|
|
|
|
|
|
249 |
|
|
|
|
|
|
|
|
|
|
|
13 |
|
|
|
|
|
Adjustments to initially adopt
SFAS No. 158: |
|
|
|
|
|
|
|
|
|
|
|
|
|
|
|
|
|
|
|
|
|
|
|
|
Prior service costs, net of tax
of $1,363 |
|
|
|
|
|
|
|
|
|
|
|
|
|
|
2,224 |
|
|
|
|
|
|
|
|
|
Net losses, net of tax of $8,629 |
|
|
|
|
|
|
|
|
|
|
|
|
|
|
(14,080 |
) |
|
|
|
|
|
|
|
|
|
|
|
|
|
|
|
|
|
|
|
|
|
|
|
|
|
|
|
|
|
|
|
|
|
|
|
|
|
|
|
|
|
|
|
|
|
|
|
|
|
|
|
|
|
|
|
|
|
|
BALANCE JULY 1, 2007 |
|
|
$69 |
|
|
|
$78,122 |
|
|
|
$165,928 |
|
|
|
$(14,341 |
) |
|
|
$(126,818 |
) |
|
|
|
|
|
|
|
|
|
|
|
|
|
|
|
|
|
|
|
|
|
|
|
|
|
|
|
|
|
Net Income |
|
|
|
|
|
|
|
|
|
|
3,267 |
|
|
|
|
|
|
|
|
|
|
|
$ 3,267 |
|
Translation adjustments |
|
|
|
|
|
|
|
|
|
|
|
|
|
|
714 |
|
|
|
|
|
|
|
714 |
|
Pension and postretirement
funded status adjustment,
net of tax of $2,371 |
|
|
|
|
|
|
|
|
|
|
|
|
|
|
(3,868 |
) |
|
|
|
|
|
|
(3,868 |
) |
|
|
|
|
|
|
|
|
|
|
|
|
|
|
|
|
|
|
|
|
|
|
|
|
|
Comprehensive income |
|
|
|
|
|
|
|
|
|
|
|
|
|
|
|
|
|
|
|
|
|
|
$ 113 |
|
|
|
|
|
|
|
|
|
|
|
|
|
|
|
|
|
|
|
|
|
|
|
|
|
|
Purchase of common stock |
|
|
|
|
|
|
|
|
|
|
|
|
|
|
|
|
|
|
(3,109 |
) |
|
|
|
|
Cash dividends declared
($1.60 per share) |
|
|
|
|
|
|
|
|
|
|
(5,652 |
) |
|
|
|
|
|
|
|
|
|
|
|
|
Stock-Based
Compensation, including
tax benefit on restricted stock
dividends of $13 |
|
|
|
|
|
|
745 |
|
|
|
|
|
|
|
|
|
|
|
|
|
|
|
|
|
Adoption of FIN 48 |
|
|
|
|
|
|
|
|
|
|
346 |
|
|
|
|
|
|
|
|
|
|
|
|
|
Employee stock purchases |
|
|
|
|
|
|
18 |
|
|
|
|
|
|
|
|
|
|
|
11 |
|
|
|
|
|
|
|
|
|
|
|
|
|
|
|
|
|
|
|
|
|
|
|
|
|
|
|
|
|
|
|
|
|
|
|
|
|
|
|
|
|
|
|
|
|
|
|
|
|
|
|
|
|
|
|
BALANCE JUNE 29, 2008 |
|
|
$69 |
|
|
|
$78,885 |
|
|
|
$163,889 |
|
|
|
$(17,495 |
) |
|
|
$(129,916 |
) |
|
|
|
|
|
|
|
|
|
|
|
|
|
|
|
|
|
|
|
|
|
|
|
|
|
|
|
|
|
The accompanying Notes to Financial Statements are an integral part of these
Consolidated Statements of Shareholders Equity.
CONSOLIDATED STATEMENTS OF CASH FLOWS
(IN THOUSANDS)
|
|
|
|
|
|
|
|
|
|
|
|
|
|
|
Years Ended |
|
|
|
|
|
|
|
June 29, 2008 |
|
|
July 1, 2007 |
|
|
July 2, 2006 |
|
|
|
|
|
|
|
|
|
|
|
|
|
|
CASH FLOWS FROM OPERATING ACTIVITIES |
|
|
|
|
|
|
|
|
|
|
|
|
Net Income |
|
|
$ 3,267 |
|
|
|
$ 8,183 |
|
|
|
$12,477 |
|
Adjustments to reconcile net income to
net cash provided by operating activities: |
|
|
|
|
|
|
|
|
|
|
|
|
Minority Interest |
|
|
26 |
|
|
|
(75 |
) |
|
|
|
|
Depreciation |
|
|
6,830 |
|
|
|
6,988 |
|
|
|
7,155 |
|
Loss on disposition of property,
plant and equipment |
|
|
434 |
|
|
|
58 |
|
|
|
320 |
|
Deferred income taxes |
|
|
920 |
|
|
|
(359 |
) |
|
|
350 |
|
Tax benefit from options exercised |
|
|
|
|
|
|
23 |
|
|
|
61 |
|
Stock-based compensation expense |
|
|
741 |
|
|
|
738 |
|
|
|
1,118 |
|
Provision for doubtful accounts |
|
|
|
|
|
|
|
|
|
|
1,622 |
|
Change in operating assets and liabilities: |
|
|
|
|
|
|
|
|
|
|
|
|
Receivables |
|
|
3,465 |
|
|
|
1,434 |
|
|
|
(3,870 |
) |
Inventories |
|
|
(3,103 |
) |
|
|
2,171 |
|
|
|
2,317 |
|
Other assets |
|
|
(8,413 |
) |
|
|
(7,277 |
) |
|
|
(3,953 |
) |
Accounts payable and accrued liabilities |
|
|
163 |
|
|
|
(1,937 |
) |
|
|
2,184 |
|
Other, net |
|
|
(576 |
) |
|
|
(153 |
) |
|
|
(485 |
) |
|
|
|
|
|
|
|
|
|
|
|
|
|
Net cash provided by operating activities |
|
|
3,754 |
|
|
|
9,794 |
|
|
|
19,296 |
|
|
|
|
|
|
|
|
|
|
|
|
|
|
|
|
|
|
|
|
|
|
|
|
|
|
|
CASH FLOWS FROM INVESTING ACTIVITIES |
|
|
|
|
|
|
|
|
|
|
|
|
Investment in joint ventures |
|
|
|
|
|
|
(100 |
) |
|
|
(569 |
) |
Additions to property, plant and equipment |
|
|
(10,930 |
) |
|
|
(5,748 |
) |
|
|
(5,766 |
) |
Proceeds received on sale of property,
plant and equipment |
|
|
|
|
|
|
21 |
|
|
|
22 |
|
|
|
|
|
|
|
|
|
|
|
|
|
|
Net cash used in investing activities |
|
|
(10,930 |
) |
|
|
(5,827 |
) |
|
|
(6,313 |
) |
|
|
|
|
|
|
|
|
|
|
|
|
|
|
|
|
|
|
|
|
|
|
|
|
|
|
CASH FLOWS FROM FINANCING ACTIVITIES |
|
|
|
|
|
|
|
|
|
|
|
|
Purchase of common stock |
|
|
(3,109 |
) |
|
|
(5,075 |
) |
|
|
(5,306 |
) |
Exercise of stock options and employee stock purchases |
|
|
29 |
|
|
|
238 |
|
|
|
1,085 |
|
Dividends paid |
|
|
(5,133 |
) |
|
|
|
|
|
|
|
|
Loan from minority interest |
|
|
1,050 |
|
|
|
|
|
|
|
|
|
Contribution from minority interest |
|
|
349 |
|
|
|
649 |
|
|
|
|
|
|
|
|
|
|
|
|
|
|
|
|
|
|
Net cash used in financing activities |
|
|
(6,814 |
) |
|
|
(4,188 |
) |
|
|
(4,221 |
) |
|
|
|
|
|
|
|
|
|
|
|
|
|
|
|
|
|
|
|
|
|
|
|
|
|
|
NET (DECREASE) INCREASE IN CASH
AND CASH EQUIVALENTS |
|
|
(13,990 |
) |
|
|
(221 |
) |
|
|
8,762 |
|
|
|
|
|
|
|
|
|
|
|
|
|
|
CASH AND CASH EQUIVALENTS |
|
|
|
|
|
|
|
|
|
|
|
|
Beginning of year |
|
|
65,491 |
|
|
|
65,712 |
|
|
|
56,950 |
|
|
|
|
|
|
|
|
|
|
|
|
|
|
End of year |
|
|
$51,501 |
|
|
|
$65,491 |
|
|
|
$65,712 |
|
|
|
|
|
|
|
|
|
|
|
|
|
|
|
|
|
|
|
|
|
|
|
|
|
|
|
SUPPLEMENTAL DISCLOSURE OF
CASH FLOW INFORMATION |
|
|
|
|
|
|
|
|
|
|
|
|
Income taxes paid |
|
|
$ 3,238 |
|
|
|
$ 3,231 |
|
|
|
$ 3,120 |
|
Interest paid |
|
|
|
|
|
|
|
|
|
|
|
|
The accompanying Notes to Financial Statements are an integral part of these Consolidated Statements of Cash Flows.
NOTES TO FINANCIAL STATEMENTS
ORGANIZATION AND SUMMARY OF SIGNIFICANT ACCOUNTING POLICIES
STRATTEC SECURITY CORPORATION designs, develops, manufactures and markets mechanical
locks and keys, electronically enhanced locks and keys, steering column and instrument
panel ignition lock housings, latches, door handles and related access control products
for North American automotive customers, and for global automotive manufacturers through
the VAST Alliance in which we participate with WITTE Automotive of Velbert, Germany and
ADAC Automotive of Grand Rapids, Michigan. STRATTECs history in the automotive business
spans 100 years.
The accompanying consolidated financial statements reflect the consolidated results
of STRATTEC SECURITY CORPORATION, its wholly owned Mexican subsidiaries, STRATTEC de
Mexico and STRATTEC Componentes Automotrices, and its majority owned subsidiary,
ADAC-STRATTEC LLC. STRATTEC SECURITY CORPORATION is located in Milwaukee, Wisconsin.
STRATTEC de Mexico and STRATTEC Componentes Automotrices are located in Juarez, Mexico.
ADAC-STRATTEC LLC has operations in El Paso, Texas and Juarez, Mexico. STRATTEC has only
one reporting segment.
The significant accounting policies followed in the preparation of these financial
statements, as summarized in the following paragraphs, are in conformity with accounting
principles generally accepted in the United States of America (U.S. GAAP).
Principles of Consolidation and Presentation: The accompanying consolidated
financial statements include the accounts of STRATTEC SECURITY CORPORATION, its
wholly owned Mexican subsidiaries, and its majority owned subsidiary. Equity
investments for which STRATTEC exercises significant influence but does not control
and is not the primary beneficiary are accounted for using the equity method. All
intercompany transactions and balances have been eliminated.
Reclassifications: Certain reclassifications have been made to the 2006 and
2007 financial statements to conform to the 2008 presentation.
Fiscal Year: Our fiscal year ends on the Sunday nearest June 30. The years ended
June 29, 2008, July 1, 2007 and July 2, 2006 are each comprised of 52 weeks.
Use of Estimates: The preparation of financial statements in conformity with U.S.
GAAP requires management to make estimates and assumptions that affect the reported
amounts of assets, liabilities, revenues and expenses for the periods presented. These
estimates and assumptions could also affect the disclosure of contingencies. Actual
results and outcomes may differ from managements estimates and assumptions.
Cash and Cash Equivalents: Cash and cash equivalents include all short-term
investments with an original maturity of three months or less due to the short-term nature
of the instruments. Excess cash balances are placed in a money market account at a high
quality financial institution and in short-term commercial paper.
Fair Value of Financial Instruments: The fair value of our cash and cash
equivalents, accounts receivable and accounts payable approximated book value as of
June 29, 2008 and July 1, 2007.
Receivables: Receivables consist primarily of trade receivables due from Original
Equipment Manufacturers in the automotive industry and locksmith distributors relating to
our service and aftermarket business. We evaluate the collectibility of receivables based
on a number of factors. An allowance for doubtful accounts is recorded for significant
past due receivable balances based on a review of the past due items, general economic
conditions and the industry as a whole. In connection with the filing for Chapter 11
bankruptcy protection by Delphi Corporation on October 8, 2005, $3.4 million of
pre-petition Chapter 11 accounts receivable was sold to a third party for $1.78 million.
This resulted in a write-off of $1.62 million of accounts receivable during fiscal 2006.
Changes in the allowance for doubtful accounts are as follows (thousands of dollars):
|
|
|
|
|
|
|
|
|
|
|
|
|
|
|
|
|
|
|
Balance, |
|
Provision |
|
|
|
|
|
Balance, |
|
|
Beginning |
|
Charged to |
|
Balances |
|
End of |
|
|
of Year |
|
Expense |
|
Written Off |
|
Year |
|
|
|
Year ended June 29, 2008 |
|
$ |
250 |
|
|
$ |
|
|
|
$ |
|
|
|
$ |
250 |
|
Year ended July 1, 2007 |
|
$ |
250 |
|
|
$ |
|
|
|
$ |
|
|
|
$ |
250 |
|
Year ended July 2, 2006 |
|
$ |
250 |
|
|
$ |
1,622 |
|
|
$ |
1,622 |
|
|
$ |
250 |
|
Inventories: Inventories are comprised of material, direct labor and manufacturing
overhead, and are stated at the lower of cost or market. The last-in, first-out (LIFO)
method is used for determining the cost of the inventories at the end of each period for
approximately 94 percent of the consolidated balance. Inventories consist of the
following (thousands of dollars):
|
|
|
|
|
|
|
|
|
|
|
June 29, 2008 |
|
July 1, 2007 |
Finished products |
|
|
$ 2,521 |
|
|
|
$ 2,660 |
|
Work in process |
|
|
4,379 |
|
|
|
4,522 |
|
Purchased materials |
|
|
7,414 |
|
|
|
4,813 |
|
LIFO reserve |
|
|
(4,045 |
) |
|
|
(4,829 |
) |
|
|
|
|
|
|
|
|
|
|
|
|
$10,269 |
|
|
|
$ 7,166 |
|
|
|
|
|
|
|
|
|
|
Inventory quantities were reduced during 2007 and 2006 which resulted in a
liquidation of LIFO inventory layers carried at lower costs. The effect of the
liquidations decreased cost of goods sold by approximately $292,000 in 2007 and
$106,000 in 2006.
NOTES TO FINANCIAL STATEMENTS
Customer Tooling in Progress: We incur costs related to tooling used in component
production and assembly. Costs for development of certain tooling, which will be directly
reimbursed by the customer whose parts are produced from the tool, are accumulated on the
balance sheet and are then billed to the customer. The accumulated costs are billed upon
formal acceptance by the customer of products produced with the individual tool. Other
tooling costs are not directly reimbursed by the customer. These costs are capitalized
and amortized over the life of the related product based on the fact that the related
tool will be used over the life of the supply arrangement.
Repair and Maintenance Supply Parts: We maintain an inventory of repair and
maintenance supply parts in support of operations. This inventory includes critical
repair parts for all production equipment as well as general maintenance items. The
inventory of critical repair parts is required to avoid disruptions in our customers
just-in-time production schedules due to a lack of spare parts when equipment break-downs
occur. All required critical repair parts are on hand when the related production
equipment is placed in service and maintained to satisfy the customer model life
production and service requirements, which may be 12 to 15 years. As repair parts are
used, additional repair parts are purchased to maintain a minimum level of spare parts
inventory. Depending on maintenance requirements during the life of the equipment, excess
quantities of repair parts arise. Excess quantities are kept on hand and are not disposed
of until the equipment is no longer in service. A repair and maintenance supply parts
reserve is maintained to recognize the normal adjustment of inventory for obsolete and
slow moving supply and maintenance parts. The adequacy of the reserve is reviewed
periodically in relation to the repair parts inventory balances. The gross balance of the
repair and maintenance supply parts inventory was approximately $1.9 million at June 29,
2008, $1.8 million at July 1, 2007, and $1.9 million at July 2, 2006. The repair and
maintenance supply parts inventory balance is included in other current assets in the
Consolidated Balance Sheets. The activity related to the repair and maintenance supply
parts reserve is as follows (thousands of dollars):
|
|
|
|
|
|
|
|
|
|
|
|
|
|
|
|
|
|
|
Balance, |
|
Provision |
|
|
|
|
|
Balance, |
|
|
Beginning |
|
Charged to |
|
Amounts |
|
End of |
|
|
of Year |
|
Expense |
|
Written Off |
|
Year |
|
|
|
Year ended June 29, 2008 |
|
$ |
640 |
|
|
$ |
145 |
|
|
$ |
135 |
|
|
$ |
650 |
|
Year ended July 1, 2007 |
|
$ |
650 |
|
|
$ |
32 |
|
|
$ |
42 |
|
|
$ |
640 |
|
Year ended July 2, 2006 |
|
$ |
650 |
|
|
$ |
49 |
|
|
$ |
49 |
|
|
$ |
650 |
|
Property, Plant and Equipment: Property, plant and equipment are stated at cost.
Plant and equipment are depreciated on a straight-line basis over the estimated useful
lives of the assets as follows:
|
|
|
|
|
Classification |
|
Expected Useful Lives |
|
Land improvements |
|
20 years |
Buildings and improvements |
|
|
20 to 35 years |
|
Machinery and equipment |
|
|
3 to 10 years |
|
Property, plant and equipment consist of the following (thousands of dollars):
|
|
|
|
|
|
|
|
|
|
|
June 29, 2008 |
|
July 1, 2007 |
Land and improvements |
|
|
$ 3,349 |
|
|
|
$ 1,405 |
|
Buildings and improvements |
|
|
12,913 |
|
|
|
12,712 |
|
Machinery and equipment |
|
|
103,183 |
|
|
|
98,803 |
|
|
|
|
|
|
|
|
|
|
|
|
|
119,445 |
|
|
|
112,920 |
|
Less: accumulated depreciation |
|
|
(89,109 |
) |
|
|
(86,394 |
) |
|
|
|
|
|
|
|
|
|
|
|
|
$ 30,336 |
|
|
|
$ 26,526 |
|
|
|
|
|
|
|
|
|
|
Long-lived assets are reviewed for impairment whenever events or changes in
circumstances indicate that the carrying amount of an asset may not be recoverable.
Recoverability of assets to be held and used is measured by a comparison of the carrying
amount of an asset to future net undiscounted cash flows expected to be generated by the
asset. If such assets are considered to be impaired, the impairment recognized is
measured by the excess of the carrying amount of the assets over the fair value of the
assets. Assets to be disposed of are reported at the lower of the carrying amount or fair
value, less estimated costs to sell. In 2008, a loss was recognized on a customer program
specific fixed asset in the amount of $382,000.
Expenditures for repairs and maintenance are charged to expense as incurred.
Expenditures for major renewals and betterments, which significantly extend the useful
lives of existing plant and equipment, are capitalized and depreciated. Upon retirement
or disposition of plant and equipment, the cost and related accumulated depreciation are
removed from the accounts and any resulting gain or loss is recognized in income.
Supplier Concentrations: Approximately 25 percent, 31 percent, and 35 percent of
all inventory purchases were made from three major suppliers during 2008, 2007 and 2006,
respectively. We have long-term contracts or arrangements with most of our suppliers to
guarantee the availability of merchandise.
NOTES TO FINANCIAL STATEMENTS
Labor Concentrations: We had approximately 2,000 full-time employees of which
approximately 217 or 10.9 percent were represented by a labor union at June 29, 2008. The
employees represented by a labor union account for all production associates at our
Milwaukee facility. The current contract with the unionized associates is effective
through June 30, 2012.
Revenue Recognition: Revenue is recognized upon the shipment of products, which
is when title passes, payment terms are final, we have no remaining obligations and
the customer is required to pay. Revenue is recognized net of estimated returns and
discounts, which is recognized as a deduction from revenue at the time of the
shipment.
Research and Development Costs: Expenditures relating to the development of new
products and processes, including significant improvements and refinements to existing
products, are expensed as incurred. Research and development expenditures were
approximately $2.9 million in 2008, $2.2 million in 2007, and $2.3 million in 2006.
Self Insurance and Loss Sensitive Plans: We have self-insured medical and dental
plans covering all eligible U.S. associates. The claims handling process for the
self-insured plans is managed by a third party administrator. Stop-loss insurance coverage
limits our liability on a per individual per calendar year basis. The per individual per
calendar year stop-loss limit was $150,000 in each calendar year 2006 through 2008. In
calendar 2005, we also maintained stop-loss insurance coverage on an aggregate per
calendar year basis. The aggregate stop-loss limit was approximately $6.1 million in
calendar year 2005. Each covered individual can receive up to $2 million in total benefits
during his or her lifetime. Once an individuals medical claims reach $2 million, we are
no longer liable for any additional claims for that individual.
We maintain an insured workers compensation program covering all U.S. associates.
The insurance is renewed annually, with a renewal date of February 27. The policy may be
a guaranteed cost policy or a loss sensitive policy. Under a guaranteed cost policy, the
ultimate cost is known at the beginning of the policy period and is subject to change
only as a result of changes in payrolls. Under a loss sensitive policy, the ultimate cost
is dependent upon losses incurred during each policy period. The incurred loss amount for
loss sensitive policies will continue to change as claims develop and are settled in
future reporting periods.
The expected ultimate cost for claims incurred under the self-insured medical and
dental plans and loss sensitive workers compensation plan as of the balance sheet date is
not discounted and is recognized as an expense. The expected ultimate cost of claims is
estimated based upon the aggregate liability for reported claims and an estimated
liability for claims incurred but not reported, which is based on analysis of historical
data, current trends and information available from the insurance carrier. The expected
ultimate cost for claims incurred under the self-insured medical and dental plans that has
not been paid as of the balance sheet date is included in the accrued payroll and benefits
liabilities amount in our Consolidated Balance Sheets. The schedule of premium payments
due under the workers compensation plan requires a larger percentage of the estimated
premium dollars to be paid during the beginning of the policy period. The excess of the
premium payments over the expected ultimate cost for claims incurred as of the balance
sheet date is included in other current assets in our Consolidated Balance Sheets.
Changes in the balance sheet amounts for self-insured and loss sensitive
plans are as follows (thousands of dollars):
|
|
|
|
|
|
|
|
|
|
|
|
|
|
|
|
|
|
|
Balance, |
|
Provision |
|
|
|
|
|
Balance, |
|
|
Beginning |
|
Charged to |
|
|
|
|
|
End of |
|
|
of Year |
|
Expense |
|
Payments |
|
Year |
|
|
|
Year ended June 29, 2008 |
|
|
|
|
|
|
|
|
|
|
|
|
|
|
|
|
Incurred but not reported claims
reserve for self-insured plans |
|
|
$300 |
|
|
$ |
2,408 |
|
|
$ |
2,408 |
|
|
|
$300 |
|
Workers Compensation |
|
|
(251 |
) |
|
|
254 |
|
|
|
143 |
|
|
|
(140 |
) |
Year ended July 1, 2007 |
|
|
|
|
|
|
|
|
|
|
|
|
|
|
|
|
Incurred but not reported claims
reserve for self-insured plans |
|
|
$400 |
|
|
$ |
2,250 |
|
|
$ |
2,350 |
|
|
|
$300 |
|
Workers Compensation |
|
|
(185 |
) |
|
|
331 |
|
|
|
397 |
|
|
|
(251 |
) |
Year ended July 2, 2006 |
|
|
|
|
|
|
|
|
|
|
|
|
|
|
|
|
Incurred but not reported claims
reserve for self-insured plans |
|
|
$500 |
|
|
$ |
2,733 |
|
|
$ |
2,833 |
|
|
|
$400 |
|
Workers Compensation |
|
|
(202 |
) |
|
|
314 |
|
|
|
297 |
|
|
|
(185 |
) |
Product Warranty: We provide a specific accrual for known product issues.
Historical activity for product issues has not been significant.
NOTES TO FINANCIAL STATEMENTS
Foreign Currency Translation: The financial statements of our foreign subsidiaries
and equity investees are translated into U.S. dollars using the exchange rate at each
balance sheet date for assets and liabilities and the average exchange rate for each
applicable period for sales, costs and expenses. Foreign currency translation gains and
losses are included as a component of other accumulated comprehensive loss. Foreign
currency transaction gains and losses are included in other income, net in the
Consolidated Income Statements and are not significant for any period presented.
Accumulated Other Comprehensive Loss: Accumulated other comprehensive loss is
comprised of the following (thousands of dollars):
|
|
|
|
|
|
|
|
|
|
|
|
|
|
|
June 29, 2008 |
|
July 1, 2007 |
|
July 2, 2006 |
Minimum pension liability, net of tax |
|
|
$ |
|
|
|
$ |
|
|
|
$ 62 |
|
Unrecognized pension and postretirement
benefit liabilities, net of tax |
|
|
15,762 |
|
|
|
11,894 |
|
|
|
|
|
Foreign currency translation |
|
|
1,733 |
|
|
|
2,447 |
|
|
|
2,896 |
|
|
|
|
|
|
|
|
|
|
|
|
|
|
|
|
|
$17,495 |
|
|
|
$14,341 |
|
|
|
$ 2,958 |
|
|
|
|
|
|
|
|
|
|
|
|
|
|
Deferred taxes have not been provided for the foreign currency translation adjustments in
accordance with Statement of Financial Accounting Standards (SFAS) No. 109, Accounting for Income
Taxes.
Accounting For Stock-Based Compensation: We maintain an omnibus stock incentive plan. This
plan provides for the granting of stock options, shares of restricted stock and stock appreciation
rights. The Board of Directors has designated 1,700,000 shares of common stock available for the
grant of awards under the plan. Remaining shares available to be granted under the plan as of June
29, 2008 were 380,463. Awards that expire or are cancelled without delivery of shares become
available for re-issuance under the plan. We issue new shares of common stock to satisfy stock
option exercises.
Nonqualified and incentive stock options and shares of restricted stock have been
granted to our officers and specified employees under the stock incentive plan. Stock
options granted under the plan may not be issued with an exercise price less than the
fair market value of the common stock on the date the option is granted. Stock options
become exercisable as determined at the date of grant by the Compensation Committee of
the Board of Directors. The options expire 5 to 10 years after the grant date unless an
earlier expiration date is set at the time of grant. The options vest 1 to 3 years after
the date of grant. Shares of restricted stock granted under the plan are subject to
vesting criteria determined by the Compensation Committee of the Board of Directors at
the time the shares are granted. Restricted shares granted have voting and dividend
rights. The restricted stock granted vests 3 years after the date of grant.
The fair value of each stock option grant was estimated as of the date of grant using
the Black-Scholes pricing model. The resulting compensation cost for fixed awards with
graded vesting schedules is amortized on a straight-line basis over the vesting period for
the entire award. The expected term of awards granted is determined based on historical
experience with similar awards, giving consideration to the expected term and vesting
schedules. The expected volatility is determined based on our historical stock prices over
the most recent period commensurate with the expected term of the award. The risk-free
interest rate is based on U.S. Treasury zero-coupon issues with a remaining term
commensurate with the expected term of the award. Expected pre-vesting option forfeitures
are based primarily on historical data. The fair value of each restricted stock grant was
based on the market price of the underlying common stock as of the date of grant. The
resulting compensation cost is amortized on a straight line basis over the vesting period.
We record stock based compensation only for those awards that are expected to vest.
As of June 29, 2008, there was $7,000 of total unrecognized compensation cost
related to stock options granted under the plan. This cost is expected to be recognized
over a weighted average period of 1 month. As of June 29, 2008, there was $450,000 of
total unrecognized compensation cost related to restricted stock grants under the plan.
This cost is expected to be recognized over a weighted average period of 11 months. Total
unrecognized compensation cost will be adjusted for any future changes in estimated and
actual forfeitures.
No stock options were exercised during fiscal 2008.
The intrinsic value of stock options exercised and the fair value of stock options
vested are as follows (in thousands of dollars):
|
|
|
|
|
|
|
|
|
|
|
|
|
|
|
Years Ended |
|
|
June 29, 2008 |
|
July 1, 2007 |
|
July 2, 2006 |
Intrinsic value of options exercised |
|
|
$ 0 |
|
|
$ |
186 |
|
|
$ |
188 |
|
Fair value of stock options vesting |
|
|
$ 273 |
|
|
$ |
762 |
|
|
$ |
1,480 |
|
NOTES TO FINANCIAL STATEMENTS
No options were granted during 2008 or 2007. The grant date fair values and
assumptions used to determine compensation expense in 2006 are as follows:
|
|
|
|
|
Options Granted During
|
|
|
2006 |
|
Weighted average grant date fair value: |
|
|
|
|
Options issued at grant date market value
|
|
|
n/a |
|
Options issued above grant date market value
|
|
|
$11.92 |
|
Assumptions: |
|
|
|
|
Risk free interest rates
|
|
|
4.08% |
|
Expected volitilty
|
|
|
31.77% |
|
Expected term (in years)
|
|
|
4.00 |
|
No dividends were assumed in the grant date fair value calculations as we did not
intend to pay cash dividends on our common stock as of the grant date.
The range of options outstanding as of June 29, 2008, is as follows:
|
|
|
|
|
|
|
|
|
|
|
|
|
|
|
Weighted Average Remaining |
|
|
Number of Options |
|
Weighted Average Exercise |
|
Contractual Life Outstanding |
|
|
Outstanding/Exercisable |
|
Price Outstanding/Exercisable |
|
(In Years) |
|
|
|
$31.95-$44.93
|
|
5,100/5,100
|
|
$39.25/$39.25
|
|
|
3.7 |
|
$53.07-$56.08
|
|
56,500/56,500
|
|
$53.87/$56.87
|
|
|
5.4 |
|
Over $61.21
|
|
126,180/86,840
|
|
$61.72/$61.94
|
|
|
2.4 |
|
|
|
|
|
$58.74/$58.09 |
|
|
|
|
Recent Accounting Pronouncements: In December 2007, the Financial Accounting
Standards Board issued Statement of Financial Accounting Standards (SFAS) No. 160,
Noncontrolling Interests in Consolidated Financial Statements an amendment to ARB No.
51. SFAS No. 160 establishes accounting and reporting standards that require the
ownership interest in subsidiaries held by parties other than the parent be clearly
identified and presented in the consolidated balance sheets within equity, but separate
from the parents equity, the amount of consolidated net income attributable to the parent
and the noncontrolling interest be clearly identified and presented on the face of the
consolidated statements of income, and changes in a parents ownership interest while the
parent retains its controlling financial interest in its subsidiary be accounted for
consistently. This statement is effective for fiscal years beginning after December 15,
2008 and will be effective for us beginning in fiscal 2010. We do not expect the new
standard to have a material impact on our financial position or results of operations.
In December 2007, the FASB issued SFAS No. 141(R), Business Combinations. SFAS No.
141(R) retains the underlying concepts of SFAS No. 141 in that all business combinations
are required to be accounted for at fair value under the acquisition method of accounting,
but SFAS No. 141(R) changed the method of applying the acquisition method in a number of
aspects. SFAS No. 141(R) will require that (1) for all business combinations, the acquirer
records all assets and liabilities of the acquired business, including goodwill, generally
at their fair values; (2) certain contingent assets and liabilities acquired be recognized
at their fair value on the acquisition date; (3) contingent consideration be recognized at
its fair value on the acquisition date and, for certain arrangements, changes in fair
value will be recognized in earnings when settled; (4) acquisition related transaction and
restructuring costs be expensed rather than treated as part of the cost of the acquisition
and included in the amount recorded for assets acquired; (5) in step acquisitions,
previous equity interests in an acquiree held prior to obtaining control be remeasured to their acquisition date fair values, with any
gain or loss recognized in earnings; and (6) when making adjustments to finalize initial
accounting, companies revise any previously issued post-acquisition financial information
in future financial statements to reflect any adjustments as if they had been recorded on
the acquisition date. SFAS No. 141(R) is effective on a prospective basis for all business
combinations for which the acquisition date is on or after the beginning of the first
annual period subsequent to December 15, 2008, with the exception of the accounting for
valuation allowances on deferred taxes and acquired tax contingencies. SFAS No. 141(R)
amends SFAS No. 109 such that the adjustments made to valuation allowances on deferred
taxes and acquired tax contingencies associated with acquisitions that closed prior to the
effective date of this statement should also apply the provisions of SFAS No. 141(R). This
standard will be applied to all future business combinations in accordance with the
effective dates.
NOTES TO FINANCIAL STATEMENTS
INVESTMENT IN JOINT VENTURES
We participate in certain Alliance Agreements with WITTE Automotive (WITTE) and
ADAC Automotive (ADAC). WITTE, of Velbert, Germany, is a privately held automotive
supplier. WITTE designs, manufactures and markets components including locks and keys,
hood latches, rear compartment latches, seat back latches, door handles and specialty
fasteners. WITTEs primary market for these products has been Europe. ADAC, of Grand
Rapids, Michigan, is a privately held automotive supplier and manufactures engineered
products, including door handles and other automotive trim parts, utilizing plastic
injection molding, automated painting and various assembly processes.
The Alliance provides a set of cross-licensing agreements for the manufacture,
distribution and sale of WITTE products by STRATTEC and ADAC in North America, and the
manufacture, distribution and sale of STRATTEC and ADAC products by WITTE in Europe.
Additionally, a joint venture company, Vehicle Access Systems Technology LLC (VAST
LLC), in which WITTE, STRATTEC and ADAC each hold a one-third interest, exists to seek
opportunities to manufacture and sell the companies products in areas of the world
outside of North America and Europe.
VAST LLC participates in joint ventures in Brazil and China. VAST do Brasil, a joint
venture between VAST LLC and Ifer do Brasil Ltda., was formed to service customers in
South America. VAST Fuzhou and VAST Great Shanghai, joint ventures between VAST LLC,
Fortitude Corporation and a unit of Elitech Technology Co. Ltd. of Taiwan, are the base of
operations to service our automotive customers in the Asian market.
The VAST investments are accounted for using the equity method of accounting. The
activities related to the VAST joint ventures resulted in a gain of approximately
$561,000 in 2008 and $394,000 in 2007. A capital contribution of $100,000 was made to
the VAST LLC joint venture in 2007 primarily in support of general operating expenses.
No capital contributions were made in 2008.
In 2007, we entered into a joint venture with ADAC, in which STRATTEC holds a 50.1
percent interest and ADAC holds a 49.9 percent interest. The joint venture was created to
establish injection molding and door handle assembly operations in Mexico. ADAC-STRATTEC
LLC, a Delaware limited liability company, was formed on October 27, 2006. An additional
Mexican entity, ADAC-STRATTEC de Mexico, which is wholly owned by ADAC-STRATTEC LLC, was
formed on February 21, 2007. ADAC-STRATTEC de Mexico production activities began in July
2007. ADAC-STRATTEC LLCs financial results are consolidated with the financial results
of STRATTEC and resulted in increased net income to STRATTEC of $26,000 in 2008 and
reduced net income of $75,000 in 2007.
In combination with WITTE and VAST LLC, we have reached a definitive agreement to
acquire certain assets, primarily equipment and inventory, and assume certain employee
liabilities of Delphi Corporations Power Products business for $7.8 million, subject to
closing agreements. STRATTEC will acquire the North American portion of Delphis Power
Products business. WITTE will participate in the North American portion as a minority
investor. WITTE will acquire the European portion and VAST LLC will acquire the Asian
portion. The transaction is subject to both customary and other closing conditions
relating to Delphis bankruptcy court proceedings. We expect to complete the transaction
before the end of calendar 2008.
Delphis Power Products business designs, develops, tests, manufactures, markets and
sells power systems to operate vehicle sliding doors, and rear compartment access points
such as liftgates and trunk lids. In addition the product line includes power cinching
latches and power cinching strikers used in these systems. Current customers for these
products supplied from North America include Chrysler LLC, Hyundai/Kia Motor Company,
General Motors Corporation and Ford Motor Company.
LINE OF CREDIT
We have a $50.0 million unsecured line of credit (the Line of Credit), which
expires October 31, 2008. Interest on borrowings under the Line of Credit are at varying
rates based on the London Interbank Offering Rate or the banks prime rate. There were no
outstanding borrowings at June 29, 2008 or July 1, 2007. There were no borrowings under the Line
of Credit during 2008, 2007 or 2006.
COMMITMENTS AND CONTINGENCIES
In 1995, we recorded a provision of $3.0 million for estimated costs to remediate a
site at our Milwaukee facility. The site was contaminated by a solvent spill, which
occurred in 1985, from a former above-ground solvent storage tank located on the east side
of the facility. The reserve was established based on third party estimates to adequately
cover the cost for active remediation of the contamination. We continue to monitor and
evaluate the site with the use of groundwater monitoring wells that are installed on the
property. An environmental consultant samples these wells one to two times a year to
determine the status of the
NOTES TO FINANCIAL STATEMENTS
contamination and the potential for remediation of the contamination by natural
attenuation, the dissipation of the contamination over time to concentrations below
applicable standards. If such sampling evidences a sufficient degree of and trend toward
natural attenuation of the contamination, we may be able to obtain a closure letter from
the regulatory authorities resolving the issue without the need for active remediation.
If a sufficient degree and trend toward natural attenuation is not evidenced by
sampling, a more active form of remediation beyond natural attenuation may be required.
The sampling has not yet satisfied all of the requirements for closure by natural
attenuation. As a result sampling continues and the reserve remains. The reserve is not
measured on a discounted basis. Management believes, based upon findings-to-date and
known environmental regulations, that the environmental reserve at June 29, 2008, is
adequate to cover any future developments.
At June 29, 2008, we had purchase commitments for zinc, aluminum, other purchased
parts and natural gas totaling approximately $10.1 million payable in 2009 and $1.8
million payable in 2010. Capital purchase obligations for the construction of a new
manufacturing facility in Juarez, Mexico total $5.4 million payable in 2009. The new
facility will replace our current leased facility. Minimum rental commitments under all
non-cancelable operating leases with a term in excess of one year are payable as follows:
2009-$478,000; 2010-$293,000; 2011-$261,000; 2012-$248,000; 2013-$135,000; 2014-$137,000;
2015-$69,000. Rental expense under all non-cancelable operating leases totaled
approximately $622,000 in 2008 and $595,000 in both 2007 and 2006.
INCOME TAXES
The provision for income taxes consists of the following (thousands of dollars):
|
|
|
|
|
|
|
|
|
|
|
|
|
|
|
2008 |
|
|
2007 |
|
|
2006 |
|
Currently payable: |
|
|
|
|
|
|
|
|
|
|
|
|
Federal |
|
|
$ 62 |
|
|
|
$2,624 |
|
|
|
$5,089 |
|
State |
|
|
226 |
|
|
|
485 |
|
|
|
738 |
|
State refund claim recovery |
|
|
|
|
|
|
(506 |
) |
|
|
(1,814 |
) |
Foreign |
|
|
17 |
|
|
|
279 |
|
|
|
40 |
|
|
|
|
|
|
|
|
|
|
|
|
|
|
|
|
|
305 |
|
|
|
2,882 |
|
|
|
4,053 |
|
Deferred tax (benefit) provision |
|
|
920 |
|
|
|
(359 |
) |
|
|
350 |
|
|
|
|
|
|
|
|
|
|
|
|
|
|
|
|
|
$1,225 |
|
|
|
$2,523 |
|
|
|
$4,403 |
|
|
|
|
|
|
|
|
|
|
|
|
|
|
The items accounting for the difference between income taxes computed at the
Federal statutory tax rate and the provision for income taxes are as follows:
|
|
|
|
|
|
|
|
|
|
|
|
|
|
|
|
2008 |
|
2007 |
|
2006 |
U.S. statutory rate |
|
|
34.0 |
% |
|
|
34.0 |
% |
|
|
34.4 |
% |
State taxes, net of Federal tax benefit |
|
|
4.6 |
|
|
|
2.6 |
|
|
|
3.1 |
|
State refund claim recovery |
|
|
|
|
|
|
(3.1 |
) |
|
|
(7.1 |
) |
Foreign sales benefit |
|
|
|
|
|
|
(4.2 |
) |
|
|
|
|
Foreign Subsidiaries |
|
|
(8.1 |
) |
|
|
(4.9 |
) |
|
|
(3.9 |
) |
Other |
|
|
(3.2 |
) |
|
|
(.8 |
) |
|
|
(.4 |
) |
|
|
|
|
|
|
|
|
|
|
|
|
|
27.3 |
% |
|
|
23.6 |
% |
|
|
26.1 |
% |
|
|
|
|
|
|
|
|
|
|
The 2008 and 2007 income tax provisions include favorable tax benefits related to the
operation of our Mexican subsidiaries as Maquiladora entities. The 2007 income tax
provision includes a state refund claim recovery. The 2007 claim recovery, net of the
Federal income tax impact, was approximately $329,000. The 2006 income tax provision
includes a state refund claim recovery and a favorable state income tax adjustment. The
2006 claim recovery and tax adjustment, net of the Federal income tax impact, was
approximately $1.2 million. The 2006 income tax provision also includes a favorable foreign tax adjustment
related to the operation of our Mexican subsidiaries of $664,000.
NOTES TO FINANCIAL STATEMENTS
The components of deferred tax assets and (liabilities) are as follows (thousands of dollars):
|
|
|
|
|
|
|
|
|
|
|
June 29, 2008 |
|
July 1, 2007 |
Deferred income taxescurrent: |
|
|
|
|
|
|
|
|
Repair and maintenance supply parts reserve |
|
|
$ 247 |
|
|
|
$ 243 |
|
Payroll-related accruals |
|
|
850 |
|
|
|
475 |
|
Environmental reserve |
|
|
1,006 |
|
|
|
1,009 |
|
Accrued customer pricing |
|
|
1,245 |
|
|
|
1,245 |
|
Other |
|
|
(96 |
) |
|
|
(243 |
) |
|
|
|
|
|
|
|
|
|
|
|
|
$ 3,252 |
|
|
|
$ 2,729 |
|
|
|
|
|
|
|
|
|
|
|
|
|
|
|
|
|
|
|
|
|
|
|
|
|
|
|
|
Deferred income taxesnoncurrent: |
|
|
|
|
|
|
|
|
Accrued pension obligations |
|
|
$(6,513 |
) |
|
|
$(4,588 |
) |
Unrecognized pension and postretirement
benefit plan liabilities |
|
|
9,661 |
|
|
|
7,290 |
|
Accumulated depreciation |
|
|
(2,319 |
) |
|
|
(2,863 |
) |
Stock-based compensation |
|
|
806 |
|
|
|
564 |
|
Postretirement obligations |
|
|
1,721 |
|
|
|
1,714 |
|
Other |
|
|
328 |
|
|
|
|
|
|
|
|
|
|
|
|
|
|
|
|
|
$ 3,684 |
|
|
|
$ 2,117 |
|
|
|
|
|
|
|
|
|
|
Deferred income tax balances reflect the effects of temporary differences between
the carrying amounts of assets and liabilities and their tax bases and are stated at
enacted tax rates expected to be in effect when taxes are actually paid or recovered.
Foreign income before the provision for income taxes was $1.6 million in 2008, $1.5
million in 2007 and $1.8 million in 2006. No provision for Federal income taxes was made
on earnings of foreign subsidiaries and joint ventures that are considered permanently
invested or that would be offset by foreign tax credits upon distribution. Such
undistributed earnings at June 29, 2008 were $9.7 million.
We adopted the provisions for FASB Interpretation No. 48 (FIN 48), Accounting for
Uncertainty in Income Taxes, on July 2, 2007. As a result of the implementation of FIN 48,
we recognized a decrease of $346,000 in accrued income taxes and a corresponding
adjustment to the beginning balance of retained earnings on the Consolidated Balance
Sheet. The total liability for unrecognized tax benefits was $1.1 million and $1.2 million
as of July 2, 2007 and June 29, 2008. This liability includes approximately $87,000 of
accrued interest at July 2, 2007 and $113,000 of accrued interest at June 29, 2008. The
liability does not include an amount for accrued penalties. The amount of unrecognized tax
benefits that, if recognized, would affect the effective tax rate was approximately
$760,000 at July 2, 2007 and $886,000 at June 29, 2008. We recognize interest and
penalties related to unrecognized tax benefits in the provision for income taxes.
A reconciliation of the beginning and ending amount of unrecognized tax
benefits is as follows (thousands of dollars):
|
|
|
|
|
Unrecognized tax benefits July 2, 2007 |
|
$ |
1,063 |
|
Gross increases tax positions in prior years |
|
|
131 |
|
Gross decreases tax positions in prior years |
|
|
|
|
Gross increases current period tax positions |
|
|
251 |
|
Lapse of statute of limitations |
|
|
(267 |
) |
|
|
|
|
Unrecognized tax benefits June 30, 2008 |
|
$ |
1,178 |
|
|
|
|
|
NOTES TO FINANCIAL STATEMENTS
We or one of our subsidiaries files income tax returns in the United States
(Federal), Wisconsin (state), Michigan (state) and various other states, Mexico and other
foreign jurisdictions. We are not currently subject to income tax examinations in any of
our significant tax jurisdictions. Tax years open to examination by tax authorities under
the statute of limitations include fiscal 2005 through 2008 for Federal, fiscal 2003
through 2008 for most states and calendar 2003 through 2007 for foreign jurisdictions.
RETIREMENT PLANS AND POSTRETIREMENT COSTS
We have a noncontributory defined benefit pension plan covering substantially all
U.S. associates. Benefits are based on years of service and final average compensation.
Our policy is to fund at least the minimum actuarially computed annual contribution
required under the Employee Retirement Income Security Act of 1974 (ERISA). Plan assets
consist primarily of listed equity and fixed income securities.
We have a noncontributory supplemental executive retirement plan (SERP), which is a
nonqualified defined benefit plan. The SERP will pay supplemental pension benefits to
certain key employees upon retirement based upon the employees years of service and
compensation. The SERP is being funded through a Rabbi Trust with M&I Trust Company. The
trust assets had a value of $3.9 million at June 29, 2008 and $4.1 million at July 1,
2007. These assets are included in other current assets in the Consolidated Balance
Sheets. The projected benefit obligation was $2.7 million at June 29, 2008 and $3.0
million at July 1, 2007. The SERP liabilities are included in the pension tables below.
However, the trust assets are excluded from the table as they do not qualify as plan
assets.
We also sponsor a postretirement health care plan for all U.S. associates hired prior
to June 2, 2001. The expected cost of retiree health care benefits is recognized during
the years that the associates who are covered under the plan render service. In June 2005,
amendments were made to the postretirement plan including a change in the number of years
of allowed benefit and a change in the medical plan providing the benefit coverage. The
maximum number of years of benefit was reduced from 10 to 5 for unionized associates
retiring after June 27, 2005 and for non-unionized associates retiring after October 1,
2005. Effective with these dates in 2005, eligibility for the benefit requires 30 years of
service and the benefit ends at age 65. The postretirement health care plan is unfunded.
Amounts included in accumulated other comprehensive income, net of tax, at June 29,
2008, which have not yet been recognized in net periodic benefit cost are as follows
(thousands of dollars):
|
|
|
|
|
|
|
|
|
|
|
Pension and SERP Benefits |
|
Postretirement Benefits |
Prior service cost (credit) |
|
|
$ 450 |
|
|
|
$(2,457 |
) |
Net actuarial loss |
|
|
11,381 |
|
|
|
6,388 |
|
|
|
|
|
|
|
|
|
|
|
|
|
$11,831 |
|
|
|
$ 3,931 |
|
|
|
|
|
|
|
|
|
|
Included in accumulated other comprehensive loss at June 29, 2008 are prior service costs of
$79,000
($49,000 net of tax) and unrecognized net actuarial losses of $255,000 ($158,000 net
of tax) expected to be recognized in pension and SERP net periodic benefit cost
during 2009.
Included in accumulated other comprehensive loss at June 29, 2008 are prior service credits of
$388,000
($241,000 net of tax) and unrecognized net actuarial losses of $695,000 ($431,000 net
of tax) expected to be recognized in postretirement net periodic benefit cost during
2009.
The following tables summarize the pension, SERP and postretirement plans
income and expense, funded status and actuarial assumptions for the years indicated
(thousands of dollars). We use a June 30 measurement date for our pension and
postretirement plans.
NOTES TO FINANCIAL STATEMENTS
|
|
|
|
|
|
|
|
|
|
|
|
|
|
|
|
|
|
|
|
|
|
|
|
|
|
|
Pension and SERP Benefits |
|
|
Postretirement Benefits |
|
|
|
2008 |
|
|
2007 |
|
|
2006 |
|
|
2008 |
|
|
2007 |
|
|
2006 |
|
COMPONENTS OF NET PERIODIC
BENEFIT COST: |
|
|
|
|
|
|
|
|
|
|
|
|
|
|
|
|
|
|
|
|
|
|
|
|
Service cost |
|
$ |
2,018 |
|
|
$ |
1,974 |
|
|
$ |
2,540 |
|
|
$ |
221 |
|
|
$ |
219 |
|
|
$ |
232 |
|
Interest cost |
|
|
4,680 |
|
|
|
4,348 |
|
|
|
3,924 |
|
|
|
718 |
|
|
|
688 |
|
|
|
491 |
|
Expected return on plan assets |
|
|
(6,210 |
) |
|
|
(5,348 |
) |
|
|
(4,989 |
) |
|
|
|
|
|
|
|
|
|
|
|
|
Amortization of prior service cost |
|
|
64 |
|
|
|
64 |
|
|
|
20 |
|
|
|
(378 |
) |
|
|
(378 |
) |
|
|
(378 |
) |
Amortization of unrecognized net loss |
|
|
643 |
|
|
|
473 |
|
|
|
1,275 |
|
|
|
702 |
|
|
|
641 |
|
|
|
528 |
|
|
|
|
|
|
|
|
|
|
|
|
|
|
|
|
|
|
|
|
Net periodic benefit cost |
|
$ |
1,195 |
|
|
$ |
1,511 |
|
|
$ |
2,770 |
|
|
$ |
1,263 |
|
|
$ |
1,170 |
|
|
$ |
873 |
|
|
|
|
|
|
|
|
|
|
|
|
|
|
|
|
|
|
|
|
|
|
|
|
|
|
|
|
|
|
|
|
|
|
|
|
|
|
|
|
|
|
|
|
|
|
|
Pension and SERP Benefits |
|
|
Postretirement Benefits |
|
|
|
June 29, |
|
|
|
|
|
July 1, |
|
June 29, |
|
|
|
|
|
July 1, |
|
|
2008 |
|
|
|
|
|
|
2007 |
|
|
2008 |
|
|
|
|
|
|
2007 |
|
WEIGHTED-AVERAGE ASSUMPTIONS |
|
|
|
|
|
|
|
|
|
|
|
|
|
|
|
|
|
|
|
|
|
|
|
|
Benefit Obligations: |
|
|
|
|
|
|
|
|
|
|
|
|
|
|
|
|
|
|
|
|
|
|
|
|
Discount rate |
|
|
7.13% |
|
|
|
|
|
|
|
6.41% |
|
|
|
7.13% |
|
|
|
|
|
|
|
6.41% |
|
Expected return on plan assets |
|
|
8.25% |
|
|
|
|
|
|
|
8.5% |
|
|
|
n/a |
|
|
|
|
|
|
|
n/a |
|
Rate of compensation increases |
|
|
3.5% |
|
|
|
|
|
|
|
3.5% |
|
|
|
n/a |
|
|
|
|
|
|
|
n/a |
|
Net Periodic Benefit Cost: |
|
|
|
|
|
|
|
|
|
|
|
|
|
|
|
|
|
|
|
|
|
|
|
|
Discount rate |
|
|
6.41% |
|
|
|
|
|
|
|
6.62% |
|
|
|
6.41% |
|
|
|
|
|
|
|
6.62% |
|
Expected return on plan assets |
|
|
8.5% |
|
|
|
|
|
|
|
8.5% |
|
|
|
n/a |
|
|
|
|
|
|
|
n/a |
|
Rate of compensation increases |
|
|
3.5% |
|
|
|
|
|
|
|
3.5% |
|
|
|
n/a |
|
|
|
|
|
|
|
n/a |
|
|
|
|
|
|
|
|
|
|
|
|
|
|
|
|
|
|
|
|
|
|
|
|
|
|
|
|
2008 |
|
|
|
|
|
|
2007 |
|
|
2008 |
|
|
|
|
|
|
2007 |
|
|
|
|
|
|
|
|
|
|
|
|
|
|
|
|
|
|
|
|
|
|
|
|
|
|
CHANGE IN PROJECTED
BENEFIT OBLIGATION: |
|
|
|
|
|
|
|
|
|
|
|
|
|
|
|
|
|
|
|
|
|
|
|
|
Benefit obligation at beginning of year |
|
$ |
74,494 |
|
|
|
|
|
|
$ |
66,953 |
|
|
$ |
11,748 |
|
|
|
|
|
|
$ |
10,851 |
|
Service cost |
|
|
2,018 |
|
|
|
|
|
|
|
1,974 |
|
|
|
221 |
|
|
|
|
|
|
|
219 |
|
Interest cost |
|
|
4,680 |
|
|
|
|
|
|
|
4,348 |
|
|
|
718 |
|
|
|
|
|
|
|
688 |
|
Plan amendments |
|
|
167 |
|
|
|
|
|
|
|
32 |
|
|
|
(131 |
) |
|
|
|
|
|
|
|
|
Actuarial (gain) loss |
|
|
(5,399 |
) |
|
|
|
|
|
|
3,773 |
|
|
|
(441 |
) |
|
|
|
|
|
|
1,221 |
|
Benefits paid |
|
|
(3,021 |
) |
|
|
|
|
|
|
(2,586 |
) |
|
|
(1,244 |
) |
|
|
|
|
|
|
(1,231 |
) |
|
|
|
|
|
|
|
|
|
|
|
|
|
|
|
|
|
|
|
Benefit obligation at end of year |
|
$ |
72,939 |
|
|
|
|
|
|
$ |
74,494 |
|
|
$ |
10,871 |
|
|
|
|
|
|
$ |
11,748 |
|
|
|
|
|
|
|
|
|
|
|
|
|
|
|
|
|
|
|
|
|
|
|
|
|
|
|
|
|
|
|
|
|
|
|
|
|
|
|
|
|
|
|
|
|
CHANGE IN PLAN ASSETS: |
|
|
|
|
|
|
|
|
|
|
|
|
|
|
|
|
|
|
|
|
|
|
|
|
Fair value of plan assets at beginning of year |
|
$ |
75,881 |
|
|
|
|
|
|
$ |
61,989 |
|
|
$ |
|
|
|
|
|
|
|
$ |
|
|
Actual return on plan assets |
|
|
(6,864 |
) |
|
|
|
|
|
|
9,478 |
|
|
|
|
|
|
|
|
|
|
|
|
|
Employer contribution |
|
|
5,000 |
|
|
|
|
|
|
|
7,000 |
|
|
|
1,244 |
|
|
|
|
|
|
|
1,231 |
|
Benefits paid |
|
|
(3,021 |
) |
|
|
|
|
|
|
(2,586 |
) |
|
|
(1,244 |
) |
|
|
|
|
|
|
(1,231 |
) |
|
|
|
|
|
|
|
|
|
|
|
|
|
|
|
|
|
|
|
Fair value of plan assets at end of year |
|
|
70,996 |
|
|
|
|
|
|
|
75,881 |
|
|
|
|
|
|
|
|
|
|
|
|
|
|
|
|
|
|
|
|
|
|
|
|
|
|
|
|
|
|
|
|
|
|
|
|
|
|
|
|
|
|
|
|
|
|
|
|
|
|
|
|
|
|
|
|
|
Funded status prepaid (accrued) benefit
obligations |
|
$ |
(1,943 |
) |
|
|
|
|
|
$ |
1,387 |
|
|
$ |
(10,871 |
) |
|
|
|
|
|
$ |
(11,748 |
) |
|
|
|
|
|
|
|
|
|
|
|
|
|
|
|
|
|
|
|
|
|
|
|
|
|
|
|
|
|
|
|
|
|
|
|
|
|
|
|
|
|
|
|
|
AMOUNTS RECOGNIZED IN
CONSOLIDATED BALANCE SHEETS: |
|
|
|
|
|
|
|
|
|
|
|
|
|
|
|
|
|
|
|
|
|
|
|
|
Accrued payroll and benefits (current
liabilities) |
|
$ |
(95 |
) |
|
|
|
|
|
$ |
(143 |
) |
|
$ |
(1,088 |
) |
|
|
|
|
|
$ |
(1,172 |
) |
Accrued benefit obligations (long-term
liabilities) |
|
|
(2,606 |
) |
|
|
|
|
|
|
(2,855 |
) |
|
|
(9,783 |
) |
|
|
|
|
|
|
(10,576 |
) |
Prepaid pension obligations (long-term
assets) |
|
|
758 |
|
|
|
|
|
|
|
4,385 |
|
|
|
|
|
|
|
|
|
|
|
|
|
|
|
|
|
|
|
|
|
|
|
|
|
|
|
|
|
|
|
|
Net amount recognized |
|
$ |
(1,943 |
) |
|
|
|
|
|
$ |
1,387 |
|
|
$ |
(10,871 |
) |
|
|
|
|
|
$ |
(11,748 |
) |
|
|
|
|
|
|
|
|
|
|
|
|
|
|
|
|
|
|
|
NOTES TO FINANCIAL STATEMENTS
|
|
|
|
|
|
|
|
|
|
|
|
|
|
|
|
|
|
|
Pension and SERP Benefits |
|
Postretirement Benefits |
|
|
June 29, |
|
|
|
June 29, |
|
|
|
|
2008 |
|
|
|
2008 |
|
|
|
|
CHANGES IN PLAN ASSETS
AND BENEFIT OBLIGATIONS
RECOGNIZED IN OTHER
COMPREHENSIVE INCOME: |
|
|
|
|
|
|
|
|
|
|
|
|
|
|
|
|
Net periodic benefit cost |
|
|
$1,195 |
|
|
|
|
|
|
|
$1,263 |
|
|
|
|
|
|
|
|
|
|
|
|
|
|
|
|
|
|
|
|
|
|
Net actuarial (gain) loss |
|
|
7,675 |
|
|
|
|
|
|
|
(441 |
) |
|
|
|
|
Prior service cost |
|
|
167 |
|
|
|
|
|
|
|
(131 |
) |
|
|
|
|
Amortization of prior service (cost) credits |
|
|
(64 |
) |
|
|
|
|
|
|
378 |
|
|
|
|
|
Amortization of unrecognized net loss |
|
|
(643 |
) |
|
|
|
|
|
|
(702 |
) |
|
|
|
|
|
|
|
|
|
|
|
|
|
|
|
|
|
|
|
|
|
Total recognized in other comprehensive income,
before tax |
|
|
7,135 |
|
|
|
|
|
|
|
(896 |
) |
|
|
|
|
|
|
|
|
|
|
|
|
|
|
|
|
|
|
|
|
|
Total recognized in net periodic benefit cost and
other comprehensive income |
|
|
$8,330 |
|
|
|
|
|
|
|
$ 367 |
|
|
|
|
|
|
|
|
|
|
|
|
|
|
|
|
|
|
|
|
|
|
The pension benefits have a separately determined accumulated benefit obligation,
which is the actuarial present value of benefits based on service rendered and current and
past compensation levels. This differs from the projected benefit obligation in that it
includes no assumptions about future compensation levels. The following table summarizes
the accumulated benefit obligations and projected benefit obligations for the pension and
SERP (thousands of dollars):
|
|
|
|
|
|
|
|
|
|
|
|
|
|
|
|
|
|
|
Pension |
|
SERP |
|
|
June 29, 2008 |
|
July 1, 2007 |
|
June 29, 2008 |
|
July 1, 2007 |
Accumulated benefit obligation |
|
$ |
65,626 |
|
|
$ |
65,385 |
|
|
$ |
2,434 |
|
|
$ |
2,998 |
|
Projected benefit obligation |
|
$ |
70,238 |
|
|
$ |
71,496 |
|
|
$ |
2,701 |
|
|
$ |
2,998 |
|
For measurement purposes, a 9 percent annual rate increase in the per capita cost of
covered health care benefits was assumed for 2009; the rate was assumed to decrease
gradually to 5 percent by the year 2016 and remain at that level thereafter.
The health care cost trend assumption has a significant effect on the postretirement
benefit amounts reported. A 1% change in the health care cost trend rates would have the
following effects (thousands of dollars):
|
|
|
|
|
|
|
|
|
|
|
1% Increase |
|
1% Decrease |
Effect on total of service and interest cost components in fiscal 2008
|
|
$ |
80 |
|
|
$ |
(71 |
) |
Effect on postretirement benefit obligation as of June 29, 2008
|
|
$ |
716 |
|
|
$ |
(643 |
) |
We employ a total return investment approach whereby a mix of equities and fixed
income investments are used to maximize the long-term return of plan assets for a prudent
level of risk. Risk tolerance is established through careful consideration of short- and
long-term plan liabilities, plan funded status and corporate financial condition. The
investment portfolio contains a diversified blend of equity and fixed income investments.
Furthermore, equity investments are diversified across U.S. and non-U.S. stocks, as well
as growth and
value style managers, and small, mid and large market capitalizations. The investment
portfolio does not include any real estate holdings. The investment policy of the plan
prohibits investment in STRATTEC stock. Investment risk is measured and monitored on an
ongoing basis through periodic investment portfolio reviews, annual liability measurements
and periodic asset/liability studies. The pension plan weighted-average asset allocations
by asset category are as follows:
|
|
|
|
|
|
|
|
|
|
|
|
|
|
|
Target Allocation |
|
June 29, 2008 |
|
July 1, 2007 |
Equity investments |
|
|
65% |
|
|
|
59% |
|
|
|
64% |
|
Fixed-income investments |
|
|
35% |
|
|
|
41% |
|
|
|
36% |
|
|
|
|
|
|
|
|
|
|
|
|
|
|
Total |
|
|
100% |
|
|
|
100% |
|
|
|
100% |
|
|
|
|
|
|
|
|
|
|
|
|
|
|
The expected long-term rate of return on U.S. pension plan assets used to calculate
the 2008 net periodic benefit cost was 8.5%. The target asset allocation is 65% public
equity and 35% fixed income. The 8.5% is approximated by applying returns of 10% on public
equity and 6% on fixed income to the target allocation. The actual historical returns are
also relevant. Annualized returns for periods ended June 29, 2008 were 5.58% for 10 years,
8.46% for 15 years and 9.32% for 20 years. Effective June 30, 2008, the expected long-term
rate of return was reduced to 8.25%.
We expect to contribute approximately $3 million to our qualified pension plan,
$95,000 to our SERP and $1.1 million to our postretirement health care plan in 2009. The
following benefit payments, which reflect expected future service, as appropriate, are
expected to be paid (thousands of dollars):
|
|
|
|
|
|
|
|
|
|
|
Pension and SERP Benefits |
|
Postretirement Benefits |
|
|
|
|
|
|
|
|
|
2009 |
|
$ |
3,346 |
|
|
$ |
1,087 |
|
2010 |
|
|
3,695 |
|
|
|
1,206 |
|
2011 |
|
|
6,304 |
|
|
|
1,380 |
|
2012 |
|
|
4,316 |
|
|
|
1,434 |
|
2013 |
|
|
4,649 |
|
|
|
1,478 |
|
2014-2018 |
|
|
27,317 |
|
|
|
4,913 |
|
NOTES TO FINANCIAL STATEMENTS
All U.S. associates may participate in a 401(k) Plan. We contribute a fixed
percentage up to the first 6 percent of eligible compensation that a participant
contributes to the plan. Our contributions totaled approximately $613,000 in 2008,
$603,000 in 2007 and $574,000 in 2006.
SHAREHOLDERS EQUITY
We have 12,000,000 shares of authorized common stock, par value $.01 per share, with
3,443,209 and 3,519,138 shares issued and outstanding at June 29, 2008 and July 1, 2007,
respectively. Holders of our common stock are entitled to one vote for each share on all
matters voted on by shareholders.
Our Board of Directors authorized a stock repurchase program to buy back up to
3,639,395 outstanding shares as of June 29, 2008. On August 19, 2008 our Board of
Directors authorized an additional 200,000 shares for repurchase under this program. As of
June 29, 2008, 3,461,333 shares have been repurchased under this program at a cost of
approximately $130.2 million. Subsequesnt to June 29, 2008 an additional 172,500 shares
were repurchased at a cost of approximately $5.7 million.
EARNINGS PER SHARE (EPS)
Basic earnings per share is computed on the basis of the weighted average number of
shares of common stock outstanding during the period. Diluted earnings per share is
computed on the basis of the weighted average number of shares of common stock plus the
dilutive potential common shares outstanding during the period using the treasury stock
method. Dilutive potential common shares include outstanding stock options and restricted
stock awards. A reconciliation of the components of the basic and diluted per share
computations follows (in thousands, except per share amounts):
|
|
|
|
|
|
|
|
|
|
|
|
|
|
|
|
|
|
|
|
|
|
|
|
|
|
|
|
|
|
|
|
|
|
|
|
|
|
|
2008 |
|
2007 |
|
2006 |
|
|
Net |
|
|
|
|
|
Per Share |
|
Net |
|
|
|
|
|
Per Share |
|
Net |
|
|
|
|
|
Per Share |
|
|
Income |
|
Shares |
|
Amount |
|
Income |
|
Shares |
|
Amount |
|
Income |
|
Shares |
|
Amount |
Basic EPS |
|
|
$3,267 |
|
|
|
3,487 |
|
|
|
$0.94 |
|
|
|
$8,183 |
|
|
|
3,552 |
|
|
|
$2.30 |
|
|
|
$12,477 |
|
|
|
3,716 |
|
|
|
$3.36 |
|
|
|
|
|
|
|
|
|
|
|
|
|
|
|
|
|
|
|
|
|
|
|
|
|
|
|
|
|
|
|
|
|
|
|
|
|
|
Stock-based
compensation |
|
|
|
|
|
|
7 |
|
|
|
|
|
|
|
|
|
|
|
3 |
|
|
|
|
|
|
|
|
|
|
|
4 |
|
|
|
|
|
|
|
|
|
|
|
|
|
|
|
|
|
|
|
|
|
|
|
|
|
|
|
|
|
|
|
|
|
|
|
|
|
|
|
|
|
|
Diluted EPS |
|
|
$3,267 |
|
|
|
3,494 |
|
|
|
$0.94 |
|
|
|
$8,183 |
|
|
|
3,555 |
|
|
|
$2.30 |
|
|
|
$12,477 |
|
|
|
3,720 |
|
|
|
$3.35 |
|
|
|
|
|
|
|
|
|
|
|
|
|
|
|
|
|
|
|
|
|
|
|
|
|
|
|
|
|
|
|
|
|
|
|
|
|
|
As of June 29, 2008, options to purchase 184,680 shares of common stock at a
weighted-average exercise price of $59.13 were excluded from the calculation of diluted
earnings per share because their inclusion would have been anti-dilutive. As of July 1,
2007, options to purchase 230,320 shares of common stock at a weighted-average exercise
price of $59.14 were excluded from the calculation of diluted earnings per share because
their inclusion would have been anti-dilutive. As of July 2, 2006, options to purchase
273,130 shares of common stock at a weighted-average exercise price of $57.70 were
excluded from the calculation of diluted earnings per share because their inclusion would
have been anti-dilutive.
STOCK OPTION AND PURCHASE PLANS
A summary of stock option activity under the plan is as follows:
|
|
|
|
|
|
|
|
|
|
|
|
|
|
|
|
|
|
|
|
|
|
|
Weighted |
|
Weighted Average |
|
Aggregate |
|
|
|
|
|
|
Average |
|
Remaining |
|
Intrinsic Value |
|
|
Shares |
|
Exercise Price |
|
Contractual Term (in years) |
|
(in thousands) |
Balance at July 3, 2005 |
|
|
281,860 |
|
|
$ |
54.80 |
|
|
|
|
|
|
|
|
|
|
|
|
|
|
|
|
|
|
|
|
|
|
|
|
|
|
Granted |
|
|
40,000 |
|
|
$ |
61.22 |
|
|
|
|
|
|
|
|
|
Exercised |
|
|
(24,220 |
) |
|
$ |
43.30 |
|
|
|
|
|
|
|
|
|
Expired |
|
|
(5,000 |
) |
|
$ |
54.99 |
|
|
|
|
|
|
|
|
|
Terminated |
|
|
(9,110 |
) |
|
$ |
59.59 |
|
|
|
|
|
|
|
|
|
|
|
|
|
|
|
|
|
|
|
|
|
|
|
|
|
|
Balance at July 2, 2006 |
|
|
283,530 |
|
|
$ |
56.53 |
|
|
|
|
|
|
|
|
|
|
|
|
|
|
|
|
|
|
|
|
|
|
|
|
|
|
Granted |
|
|
|
|
|
$ |
|
|
|
|
|
|
|
|
|
|
Exercised |
|
|
(7,300 |
) |
|
$ |
21.74 |
|
|
|
|
|
|
|
|
|
Expired |
|
|
(35,810 |
) |
|
$ |
49.24 |
|
|
|
|
|
|
|
|
|
Terminated |
|
|
(5,000 |
) |
|
$ |
56.72 |
|
|
|
|
|
|
|
|
|
|
|
|
|
|
|
|
|
|
|
|
|
|
|
|
|
|
Balance at July 1, 2007 |
|
|
235,420 |
|
|
$ |
58.71 |
|
|
|
|
|
|
|
|
|
|
|
|
|
|
|
|
|
|
|
|
|
|
|
|
|
|
Granted |
|
|
|
|
|
$ |
|
|
|
|
|
|
|
|
|
|
Exercised |
|
|
|
|
|
$ |
|
|
|
|
|
|
|
|
|
|
Expired |
|
|
(47,640 |
) |
|
$ |
58.59 |
|
|
|
|
|
|
|
|
|
Terminated |
|
|
|
|
|
$ |
|
|
|
|
|
|
|
|
|
|
|
|
|
|
|
|
|
|
|
|
|
|
|
|
|
|
|
Balance at June 29, 2008 |
|
|
187,780 |
|
|
$ |
58.74 |
|
|
|
3.3 |
|
|
$ |
3 |
|
|
|
|
|
|
|
|
|
|
|
|
|
|
|
|
|
|
|
|
|
|
|
|
|
|
|
|
|
|
|
|
|
|
|
Exercisable as of: |
|
|
|
|
|
|
|
|
|
|
|
|
|
|
|
|
June 29, 2008 |
|
|
148,440 |
|
|
$ |
58.09 |
|
|
|
3.6 |
|
|
$ |
3 |
|
July 1, 2007 |
|
|
181,080 |
|
|
$ |
58.05 |
|
|
|
3.2 |
|
|
$ |
39 |
|
July 2, 2006 |
|
|
157,350 |
|
|
$ |
52.78 |
|
|
|
4.0 |
|
|
$ |
361 |
|
|
Available for grant as of June 29, 2008 |
|
|
380,463 |
|
NOTES TO FINANCIAL STATEMENTS
A summary of restricted stock activity under the plan is as follows:
|
|
|
|
|
|
|
|
|
|
|
|
|
|
|
Weighted Average |
|
|
|
|
|
|
Grant Date |
|
|
Shares |
|
Fair Value |
Nonvested Balance at July 3, 2005 |
|
|
|
|
|
$ |
|
|
Granted |
|
|
9,900 |
|
|
$ |
51.24 |
|
Vested |
|
|
|
|
|
$ |
|
|
Forfeited |
|
|
(300 |
) |
|
$ |
51.24 |
|
|
|
|
|
|
|
|
|
|
Nonvested Balance at July 2, 2006 |
|
|
9,600 |
|
|
$ |
51.24 |
|
|
|
|
|
|
|
|
|
|
Granted |
|
|
10,000 |
|
|
$ |
40.00 |
|
Vested |
|
|
|
|
|
$ |
|
|
Forfeited |
|
|
(200 |
) |
|
$ |
40.00 |
|
|
|
|
|
|
|
|
|
|
Nonvested Balance at July 1, 2007 |
|
|
19,400 |
|
|
$ |
45.56 |
|
|
|
|
|
|
|
|
|
|
Granted |
|
|
10,000 |
|
|
$ |
47.78 |
|
Vested |
|
|
|
|
|
$ |
|
|
Forfeited |
|
|
|
|
|
$ |
|
|
|
|
|
|
|
|
|
|
|
Nonvested Balance at June 29, 2008 |
|
|
29,400 |
|
|
$ |
46.32 |
|
|
|
|
|
|
|
|
|
|
Options granted at a price greater than the market value on the date of grant included above
total 40,000 at an exercise price of $61.22 in 2006.
We have an Employee Stock Purchase Plan to
provide substantially all U.S. full-time associates an opportunity to purchase shares of STRATTEC
common stock through payroll deductions. A participant may contribute a maximum of $5,200 per
calendar year to the plan. On the last day of each month, participant account balances are used to
purchase shares of stock at the average of the highest and lowest reported sales prices of a share
of STRATTEC common stock on the NASDAQ Global Market. A total of 100,000 shares may be issued under
the plan. Shares issued from treasury stock under the plan totaled 704 at an average price of
$41.62 during 2008, 771 at an average price of $43.15 during 2007 and 822 at an average price of
$44.70 during 2006. A total of 83,215 shares are available for purchase under the plan as of June
29, 2008.
EXPORT SALES
Export sales are summarized below (thousands of dollars):
|
|
|
|
|
|
|
|
|
|
|
|
|
|
|
2008 |
|
2007 |
|
2006 |
Export Sales |
|
$ |
25,714 |
|
|
$ |
30,643 |
|
|
$ |
34,244 |
|
Percent of Net Sales |
|
|
16% |
|
|
|
18% |
|
|
|
19% |
|
These sales were primarily to automotive manufacturing assembly plants in Canada and Mexico.
SALES AND RECEIVABLE CONCENTRATION
Sales to our largest customers were as follows (thousands of dollars and percent of total net
sales):
|
|
|
|
|
|
|
|
|
|
|
|
|
|
|
|
|
|
|
|
|
|
|
|
|
|
|
2008 |
|
2007 |
|
2006 |
|
|
Sales |
|
|
% |
|
Sales |
|
|
% |
|
Sales |
|
|
% |
|
|
|
|
|
|
|
General Motors Corporation |
|
$ |
45,039 |
|
|
|
28 |
% |
|
$ |
35,687 |
|
|
|
21 |
% |
|
$ |
32,887 |
|
|
|
18 |
% |
Ford Motor Company |
|
|
19,419 |
|
|
|
12 |
% |
|
|
21,013 |
|
|
|
13 |
% |
|
|
27,295 |
|
|
|
15 |
% |
Chrysler LLC |
|
|
40,209 |
|
|
|
25 |
% |
|
|
58,099 |
|
|
|
35 |
% |
|
|
58,603 |
|
|
|
32 |
% |
Delphi Corporation |
|
|
14,872 |
|
|
|
9 |
% |
|
|
18,398 |
|
|
|
11 |
% |
|
|
26,721 |
|
|
|
15 |
% |
|
|
|
|
|
|
|
|
|
|
|
|
|
|
|
|
|
|
|
|
|
|
|
|
$ |
119,539 |
|
|
|
75 |
% |
|
$ |
133,197 |
|
|
|
80 |
% |
|
$ |
145,506 |
|
|
|
80 |
% |
|
|
|
|
|
|
|
|
|
|
|
|
|
|
|
|
|
|
|
|
|
|
Receivables from our largest customers were as follows (thousands of dollars and
percent of gross receivables):
|
|
|
|
|
|
|
|
|
|
|
|
|
|
|
|
|
|
|
June 29, 2008 |
|
July 1, 2007 |
|
|
Receivables |
|
|
% |
|
Receivables |
|
|
% |
|
|
|
|
|
General Motors Corporation |
|
|
$ 8,367 |
|
|
|
35 |
% |
|
|
$ 8,174 |
|
|
|
30 |
% |
Ford Motor Company |
|
|
2,030 |
|
|
|
9 |
% |
|
|
3,022 |
|
|
|
11 |
% |
Chrysler LLC |
|
|
6,582 |
|
|
|
28 |
% |
|
|
9,965 |
|
|
|
37 |
% |
Delphi Corporation |
|
|
830 |
|
|
|
3 |
% |
|
|
1,116 |
|
|
|
4 |
% |
|
|
|
|
|
|
|
|
|
|
|
|
|
|
|
|
|
|
|
|
$17,809 |
|
|
|
75 |
% |
|
|
$22,277 |
|
|
|
82 |
% |
|
|
|
|
|
|
|
|
|
|
|
|
|
|
|
|
|
REPORTS
REPORT ON MANAGEMENTS ASSESSMENT OF INTERNAL
CONTROL OVER FINANCIAL REPORTING
STRATTEC SECURITY CORPORATION is responsible for the preparation, integrity and fair
presentation of the Consolidated Financial Statements included in this annual report. The
Consolidated Financial Statements and Notes included in this annual report have been
prepared in conformity with accounting principles generally accepted in the United States
of America and necessarily include some amounts that are based on managements best
estimates and judgments.
We, as management of STRATTEC SECURITY CORPORATION, are responsible for establishing
and maintaining effective internal control over financial reporting that is designed to
produce reliable financial statements in conformity with United States generally accepted
accounting principles. The system of internal control over financial reporting as it
relates to the financial statements is evaluated for effectiveness by management and
tested for reliability through a program of internal audits. Actions are taken to correct
potential deficiencies as they are identified. Any system of internal control, no matter
how well designed, has inherent limitations, including the possibility that a control can
be circumvented or overridden and misstatements due to error or fraud may occur and not
be detected. Also, because of changes in conditions, internal control effectiveness may
vary over time. Accordingly, even an effective system of internal control will provide
only reasonable assurance with respect to financial statement preparation.
The Audit Committee, consisting entirely of independent directors, meets regularly
with management and the independent registered public accounting firm, and reviews audit
plans and results, as well as managements actions taken in discharging responsibilities
for accounting, financial reporting, and internal control. Grant Thornton LLP, independent
registered public accounting firm, has direct and confidential access to the Audit
Committee at all times to discuss the results of their examinations.
Management assessed the Corporations system of internal control over financial
reporting as of June 29, 2008, in relation to criteria for effective internal control over
financial reporting as described in Internal Control Integrated Framework, issued by
the Committee of Sponsoring Organizations of the Treadway Commission (COSO). Based on the
assessment, management concludes that, as of June 29, 2008, its system of internal control
over financial reporting is effective and meets the criteria of the Internal Control
Integrated Framework. Grant Thornton LLP, independent registered public accounting
firm, has issued an attestation report on managements assessment of the Corporations
internal control over financial reporting, which is included herein.
|
|
|
|
|
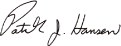 |
Harold M. Stratton II
|
|
Patrick J. Hansen |
Chairman, President and
|
|
Senior Vice President and |
Chief Executive Officer
|
|
Chief Financial Officer |
REPORTS
REPORT OF INDEPENDENT REGISTERED
PUBLIC ACCOUNTING FIRM
Board of Directors and Shareholders of STRATTEC SECURITY CORPORATION:
We have audited STRATTEC SECURITY CORPORATIONS (a Wisconsin Corporation) and subsidiaries, collectively the
Company, internal control over financial reporting as of June 29, 2008, based on criteria established in Internal
ControlIntegrated Framework issued by the Committee of Sponsoring Organizations of the Treadway Commission (COSO).
The Companys management is responsible for maintaining effective internal control over financial reporting and for its
assessment of the effectiveness of internal control over financial reporting, included in the accompanying Report on
Managements Assessment of Internal Control over Financial Reporting. Our responsibility is to express an opinion on the
Companys internal control over financial reporting based on our audit.
We conducted our audit in accordance with the standards of the Public Company Accounting Oversight Board (United States).
Those standards require that we plan and perform the audit to obtain reasonable assurance about whether effective internal
control over financial reporting was maintained in all material respects. Our audit included obtaining an understanding of
internal control over financial reporting, assessing the risk that a material weakness exists, testing and evaluating the design
and operating effectiveness of internal control based on the assessed risk, and performing such other procedures as we considered
necessary in the circumstances. We believe that our audit provides a reasonable basis for our opinion.
A companys internal control over financial reporting is a process designed to provide reasonable
assurance regarding the reliability of financial reporting and the preparation of financial
statements for external purposes in accordance with generally accepted accounting principles. A companys
internal control over financial reporting includes those policies and procedures that (1) pertain to the
maintenance of records that, in reasonable detail, accurately and fairly reflect the transactions and
dispositions of the assets of the company; (2) provide reasonable assurance that transactions are recorded
as necessary to permit preparation of financial statements in accordance with generally accepted accounting
principles, and that receipts and expenditures of the company are being made only in accordance with authorizations
of management and directors of the company; and (3) provide reasonable assurance regarding prevention or timely
detection of unauthorized acquisition, use, or disposition of the companys assets that could have a material effect on the financial statements.
Because of its inherent limitations, internal control over financial reporting may not prevent or detect
misstatements. Also, projections of any evaluation of effectiveness to future periods are subject to the
risk that controls may become inadequate because of changes in conditions, or that the degree of compliance
with the policies or procedures may deteriorate.
In our opinion, the Company maintained, in all material respects, effective internal control over financial
reporting as of June 29, 2008, based on criteria established in Internal ControlIntegrated Framework issued by COSO.
We also have audited, in accordance with the standards of the Public Company Accounting Oversight Board
(United States), the consolidated balance sheets of STRATTEC SECURITY CORPORATION and subsidiaries as of
June 29, 2008 and July 1, 2007 and the related consolidated statements of income, shareholders equity and cash
flows for the three years ended June 29, 2008 and our report dated August 19, 2008 expressed an unqualified opinion on those financial statements.

Grant Thornton LLP
Milwaukee, Wisconsin
August 19, 2008
REPORTS
REPORT OF INDEPENDENT REGISTERED
PUBLIC ACCOUNTING FIRM
Board of Directors and Shareholders of STRATTEC SECURITY CORPORATION:
We have audited the accompanying consolidated balance sheets of STRATTEC SECURITY
CORPORATION (a Wisconsin corporation) and subsidiaries, collectively the Company, as of
June 29, 2008 and July 1, 2007, and the related statements of income, shareholders
equity and cash flows for each of the three years in the period ended June 29, 2008.
These financial statements are the responsibility of the Companys management. Our
responsibility is to express an opinion on these financial statements based on our
audits.
We conducted our audits in accordance with the standards of the Public Company
Accounting Oversight Board (United States). Those standards require that we plan and
perform the audit to obtain reasonable assurance about whether the financial statements
are free of material misstatement. An audit includes examining, on a test basis,
evidence supporting the amounts and disclosures in the financial statements. An audit
also includes assessing the accounting principles used and significant estimates made by
management, as well as evaluating the overall financial statement presentation. We
believe that our audits provide a reasonable basis for our opinion.
In our opinion, the financial statements referred to above present fairly, in all
material respects, the consolidated financial position of STRATTEC SECURITY CORPORATION
and subsidiaries as of June 29, 2008 and July 1, 2007, and the results of its operations
and its cash flows for each of the three years in the period ended June 29, 2008 in
conformity with accounting principles generally accepted in the United States of
America.
As discussed in Notes to Financial Statements under Income Taxes, the Company adopted
FASB Interpretation No. 48 (FIN 48), Accounting for Uncertainty in Income Taxes, as of
July 2, 2007. As discussed in Notes to Financial Statements under Retirement Plans and
Postretirement Costs, the Company adopted Statement No.158, Employers Accounting for
Defined Benefit Pension and Other Postretirement Plans, as of July 1, 2007.
We also have audited, in accordance with the standards of the Public Company
Accounting Oversight Board (United States), STRATTEC SECURITY CORPORATIONS internal
control over financial reporting as of June 29, 2008, based on criteria established in
Internal ControlIntegrated Framework issued by the Committee of Sponsoring Organizations
of the Treadway Commission (COSO) and our report dated August 19, 2008 expressed an
unqualified opinion on the effectiveness of internal control over financial reporting.

Grant Thornton LLP
Milwaukee, Wisconsin
August 19, 2008
FINANCIAL SUMMARY
FIVE-YEAR FINANCIAL SUMMARY
The financial data for each period presented below reflects the consolidated results
of STRATTEC SECURITY CORPORATION and its wholly owned subsidiaries. The information below
should be read in conjunction with Managements Discussion and Analysis, and the
Financial Statements and Notes thereto included elsewhere herein. The following data are
in thousands of dollars except per share amounts.
|
|
|
|
|
|
|
|
|
|
|
|
|
|
|
|
|
|
|
|
|
|
|
Fiscal Years |
|
|
2008 |
|
|
2007 |
|
|
2006 |
|
|
2005 |
|
|
2004 |
|
INCOME STATEMENT DATA |
|
|
|
|
|
|
|
|
|
|
|
|
|
|
|
|
|
|
|
|
Net sales |
|
$ |
159,642 |
|
|
$ |
167,707 |
|
|
$ |
181,197 |
|
|
$ |
190,314 |
|
|
$ |
195,646 |
|
Gross profit |
|
|
25,551 |
|
|
|
26,494 |
|
|
|
37,046 |
|
|
|
42,776 |
|
|
|
47,513 |
|
Engineering, selling, and
administrative expenses |
|
|
23,962 |
|
|
|
20,189 |
|
|
|
22,067 |
|
|
|
20,688 |
|
|
|
20,624 |
|
Provision for doubtful
accounts, net |
|
|
|
|
|
|
|
|
|
|
1,622 |
|
|
|
80 |
|
|
|
26 |
|
Income from operations |
|
|
1,589 |
|
|
|
6,305 |
|
|
|
13,357 |
|
|
|
22,008 |
|
|
|
26,863 |
|
Interest income |
|
|
2,749 |
|
|
|
3,611 |
|
|
|
2,563 |
|
|
|
1,169 |
|
|
|
426 |
|
Interest expense |
|
|
|
|
|
|
|
|
|
|
|
|
|
|
|
|
|
|
|
|
Other income, net |
|
|
230 |
|
|
|
715 |
|
|
|
960 |
|
|
|
320 |
|
|
|
362 |
|
Minority interest |
|
|
(76 |
) |
|
|
75 |
|
|
|
|
|
|
|
|
|
|
|
|
|
|
|
|
|
|
|
|
|
|
|
|
|
|
|
|
|
Income before taxes |
|
|
4,492 |
|
|
|
10,706 |
|
|
|
16,880 |
|
|
|
23,497 |
|
|
|
27,651 |
|
Provision for income taxes |
|
|
1,225 |
|
|
|
2,523 |
|
|
|
4,403 |
|
|
|
8,459 |
|
|
|
10,369 |
|
|
|
|
|
|
|
|
|
|
|
|
|
|
|
|
|
Net income |
|
$ |
3,267 |
|
|
$ |
8,183 |
|
|
$ |
12,477 |
|
|
$ |
15,038 |
|
|
$ |
17,282 |
|
|
|
|
|
|
|
|
|
|
|
|
|
|
|
|
|
|
|
|
|
|
|
|
|
|
|
|
|
|
|
|
|
|
|
|
|
|
Earnings per share: |
|
|
|
|
|
|
|
|
|
|
|
|
|
|
|
|
|
|
|
|
Basic |
|
$ |
0.94 |
|
|
$ |
2.30 |
|
|
$ |
3.36 |
|
|
$ |
3.97 |
|
|
$ |
4.56 |
|
Diluted |
|
|
0.94 |
|
|
|
2.30 |
|
|
|
3.35 |
|
|
|
3.94 |
|
|
|
4.49 |
|
|
|
|
|
|
|
|
|
|
|
|
|
|
|
|
|
|
|
|
|
|
Cash dividends delcared
per share: |
|
$ |
1.60 |
|
|
|
|
|
|
|
|
|
|
|
|
|
|
|
|
|
|
|
|
|
|
|
|
|
|
|
|
|
|
|
|
|
|
|
|
|
|
BALANCE SHEET DATA |
|
|
|
|
|
|
|
|
|
|
|
|
|
|
|
|
|
|
|
|
Net working capital |
|
$ |
70,327 |
|
|
|
$81,083 |
|
|
$ |
80,264 |
|
|
$ |
74,619 |
|
|
$ |
68,682 |
|
Total assets |
|
|
141,713 |
|
|
|
148,446 |
|
|
|
154,292 |
|
|
|
138,090 |
|
|
|
137,190 |
|
Long-term liabilities |
|
|
12,389 |
|
|
|
13,431 |
|
|
|
10,510 |
|
|
|
16,271 |
|
|
|
12,054 |
|
Shareholders Equity |
|
|
95,432 |
|
|
|
102,960 |
|
|
|
110,275 |
|
|
|
91,751 |
|
|
|
89,852 |
|
QUARTERLY FINANCIAL DATA (UNAUDITED)
The following data are in thousands of dollars except per share amounts.
|
|
|
|
|
|
|
|
|
|
|
|
|
|
|
|
|
|
|
|
|
|
|
|
|
|
|
|
|
|
|
|
|
|
|
|
|
|
|
|
|
|
|
|
|
|
|
|
|
|
|
|
|
|
|
|
|
|
|
Cash |
|
|
|
|
|
|
|
|
|
|
|
|
|
|
|
|
|
|
Earnings Per Share |
|
Dividends |
Market Price Per Share |
|
|
|
|
|
|
|
|
|
|
|
Net Income |
|
|
|
|
|
|
|
|
Declared |
|
|
|
|
|
|
Quarter |
|
Net Sales |
|
Gross Profit |
(Loss) |
Basic |
|
Diluted |
|
Per Share |
|
High |
|
Low |
|
|
|
|
|
|
|
|
|
|
|
|
|
|
|
|
|
|
|
|
|
|
|
|
|
|
|
|
|
|
|
|
|
|
|
2008 |
|
First |
|
|
$ 42,739 |
|
|
|
$ 8,394 |
|
|
|
$ 2,419 |
|
|
|
$ 0.69 |
|
|
|
$ 0.69 |
|
|
|
$ 1.15 |
|
|
|
$51.04 |
|
|
|
$45.03 |
|
|
|
Second |
|
|
39,908 |
|
|
|
6,906 |
|
|
|
1,323 |
|
|
|
0.38 |
|
|
|
0.38 |
|
|
|
0.15 |
|
|
|
49.18 |
|
|
|
42.00 |
|
|
|
Third |
|
|
38,428 |
|
|
|
6,267 |
|
|
|
446 |
|
|
|
0.13 |
|
|
|
0.13 |
|
|
|
0.15 |
|
|
|
44.87 |
|
|
|
35.06 |
|
|
|
Fourth |
|
|
38,567 |
|
|
|
3,984 |
|
|
|
(921 |
) |
|
|
(0.27 |
) |
|
|
(0.27 |
) |
|
|
0.15 |
|
|
|
43.95 |
|
|
|
34.57 |
|
|
|
|
|
|
|
|
|
|
|
|
|
|
|
|
|
|
|
|
|
|
|
|
|
|
|
|
|
|
|
|
|
|
|
|
|
|
TOTAL |
|
|
$159,642 |
|
|
|
$ 25,551 |
|
|
|
$ 3,267 |
|
|
|
$ 0.94 |
|
|
|
$ 0.94 |
|
|
|
$ 1.60 |
|
|
|
|
|
|
|
|
|
|
|
|
|
|
|
|
|
|
|
|
|
|
|
|
|
|
|
|
|
|
|
|
|
|
|
|
|
|
|
|
|
|
|
|
|
|
|
|
|
|
|
|
|
|
|
|
|
|
|
|
|
|
|
|
|
|
|
|
|
|
|
|
|
|
|
|
|
|
|
2007 |
|
First |
|
|
$38,050 |
|
|
|
$ 5,282 |
|
|
|
$ 741 |
|
|
|
$ 0.21 |
|
|
|
$ 0.21 |
|
|
|
$ |
|
|
|
$48.51 |
|
|
|
$37.50 |
|
|
|
Second |
|
|
37,913 |
|
|
|
5,040 |
|
|
|
1,094 |
|
|
|
0.31 |
|
|
|
0.31 |
|
|
|
|
|
|
|
47.11 |
|
|
|
33.85 |
|
|
|
Third |
|
|
45,647 |
|
|
|
8,354 |
|
|
|
2,914 |
|
|
|
0.82 |
|
|
|
0.82 |
|
|
|
|
|
|
|
51.40 |
|
|
|
41.31 |
|
|
|
Fourth |
|
|
46,097 |
|
|
|
7,818 |
|
|
|
3,434 |
|
|
|
0.97 |
|
|
|
0.97 |
|
|
|
|
|
|
|
49.89 |
|
|
|
40.49 |
|
|
|
|
|
|
|
|
|
|
|
|
|
|
|
|
|
|
|
|
|
|
|
|
|
|
|
|
|
|
|
|
|
|
|
|
|
|
TOTAL |
|
|
$167,707 |
|
|
|
$ 26,494 |
|
|
|
$ 8,183 |
|
|
|
$ 2.30 |
|
|
|
$ 2.30 |
|
|
|
$ |
|
|
|
|
|
|
|
|
|
|
|
|
|
|
|
|
|
|
|
|
|
|
|
|
|
|
|
|
|
|
|
|
|
|
|
|
|
|
|
|
|
|
|
|
Registered shareholders of record at June 29, 2008, were 2,311.
PERFORMANCE GRAPH
The chart below shows a comparison of the cumulative return since June 27, 2003 had
$100 been invested at the close of business on June 27, 2003 in STRATTEC Common Stock,
the NASDAQ Composite Index (all issuers), and the Dow Jones U.S. Auto Parts Index. The
graph assumes reinvestment of all dividends since June 27, 2003.
|
|
|
|
|
|
|
|
|
|
|
|
|
|
|
|
|
|
|
|
|
|
|
|
|
|
|
6/27/03 |
|
6/25/04 |
|
7/1/05 |
|
6/30/06 |
|
6/29/07 |
|
6/27/08 |
|
|
|
|
|
|
|
|
|
|
|
|
|
|
|
|
|
|
|
|
|
|
|
|
|
|
|
|
|
|
|
|
|
|
|
|
|
|
|
|
STRATTEC** |
|
|
100 |
|
|
|
128 |
|
|
|
102 |
|
|
|
94 |
|
|
|
89 |
|
|
|
69 |
|
NASDAQ Composite Index |
|
|
100 |
|
|
|
129 |
|
|
|
128 |
|
|
|
136 |
|
|
|
164 |
|
|
|
143 |
|
Dow Jones U.S. Auto Parts Index |
|
|
100 |
|
|
|
131 |
|
|
|
115 |
|
|
|
115 |
|
|
|
157 |
|
|
|
117 |
|
|
|
|
*
$100 invested on June 27, 2003 in stock or index-including reinvestment of dividends. Indexes
calculated on a month-end basis. |
|
** The fiscal year end closing price of STRATTEC Common Stock on June 27, 2003 was $52.87,
the closing price on June 25, 2004 was $67.57, the closing price on July 1, 2005 was
$53.82, the closing price on June 30, 2006, was $49.81, the closing price on June 29,
2007 was $46.97, and the closing price on June 27, 2008 was $34.99. |
DIRECTORS/OFFICERS/SHAREHOLDERS INFORMATION
STRATTEC Board of Directors:
(Left to Right) Frank J. Krejci, Michael J. Koss,
Robert Feitler, Harold M. Stratton II, David R. Zimmer
BOARD OF DIRECTORS
Harold M. Stratton II, 60
Chairman, President and Chief Executive Officer
Robert Feitler, 77
Former President and Chief Operating Officer
of Weyco Group, Inc.
Chairman of the Executive Committee and
Director of Weyco Group, Inc.
Michael J. Koss, 54
President and Chief Executive Officer
of Koss Corporation Director of Koss
Corporation
Frank J. Krejci, 58
President and Chief Executive Officer
of Wisconsin Furniture, LLC
David R. Zimmer, 62
Managing Partner of
Stonebridge Business Partners
CORPORATE OFFICERS
Harold M. Stratton II,
60 Patrick J. Hansen, 49
Senior Vice President-Chief
Financial Officer, Treasurer and
Secretary
Donald J. Harrod, 64
Vice President-Engineering
and Product
Dennis A. Kazmierski, 56
Vice President-Marketing and Sales
Kathryn E. Scherbarth, 52
Vice President-Milwaukee Operations
Rolando J. Guillot, 40
Vice President-Mexican Operations
Milan R. Bundalo, 57
Vice President-Materials
Brian J. Reetz, 50
Vice President-Security Products
SHAREHOLDERS
INFORMATION
Annual Meeting
The Annual Meeting of Shareholders
will convene at 8:00 a.m. (CST) on
October 7, 2008, at the Radisson
Hotel, 7065 North Port Washington
Road, Milwaukee, WI 53217
Common Stock
STRATTEC SECURITY CORPORATION common
stock is traded on the NASDAQ Global
Market under the symbol: STRT.
Form 10-K
You may receive a copy of the
STRATTEC SECURITY CORPORATION Form
10-K, filed with the Securities and
Exchange Commission, by writing to
the Secretary at STRATTEC SECURITY
CORPORATION, 3333 W. Good Hope Road,
Milwaukee, WI 53209.
Corporate Governance
To review the Companys corporate
governance, board committee charters
and code of business ethics, please
visit the Corporate Governance
section of our Web site at
www.strattec.com.
Shareholder Inquiries
Communications concerning the
transfer of shares, lost
certificates or changes of address
should be directed to the Transfer
Agent.
Transfer Agent and Registrar
Wells Fargo Bank, N.A.
Shareholder Services
P.O. Box 64854 St.
Paul, MN 55164-0854
1.800.468.9716
|
The Trusted Leader in Automotive
Access Control Products
STRATTEC SECURITY CORPORATION
3333 WEST GOOD HOPE ROAD
MILWAUKEE, WI53209
PHONE 414.247.3333 FAX 414.247.3329
www.strattec.com |
exv23w1
EXHIBIT
23.1
CONSENT OF INDEPENDENT
REGISTERED PUBLIC ACCOUNTANTS
We have issued our reports dated August 19, 2008, with respect to the consolidated financial
statements, schedules and internal control over financial reporting included in the Annual Report
of STRATTEC SECURITY CORPORATION on Form 10-K for the year ended June 29, 2008. We hereby consent
to the incorporation by reference of said reports in the Registration Statements of STRATTEC
SECURITY CORPORATION on Forms S-8 (File No. 333-140715, effective February 14, 2007; 333-103219,
effective February 14, 2003; 333-31002, effective February 24, 2000; 333-45221, effective January
30, 1998; and 333-4300, effective April 29, 1996).
/s/ GRANT THORNTON LLP
GRANT THORNTON LLP
Milwaukee, Wisconsin
August 19, 2008
exv31w1
Exhibit 31.1
CERTIFICATION OF CHIEF EXECUTIVE OFFICER
PURSUANT TO SECTION 302 OF THE SARBANES-OXLEY ACT OF 2002
I, Harold M. Stratton II, certify that:
1. I have reviewed this annual report on Form 10-K of STRATTEC SECURITY CORPORATION;
2. Based on my knowledge, this report does not contain any untrue statement of a material fact
or omit to state a material fact necessary to make the statements made, in light of the
circumstances under which such statements were made, not misleading with respect to the period
covered by this report;
3. Based on my knowledge, the financial statements, and other financial information included
in this report, fairly present in all material respects the financial condition, results of
operations and cash flows of the registrant as of, and for, the periods presented in this report;
4. The registrants other certifying officer and I are responsible for establishing and
maintaining disclosure controls and procedures (as defined in Exchange Act Rules 13a-15(e) and
15d-15(e)) and internal control over financial reporting (as defined in Exchange Act Rules
13a-15(f) and 15d-15(f)) for the registrant and have:
(a) designed such disclosure controls and procedures, or caused such disclosure controls and
procedures to be designed under our supervision, to ensure that material information relating to
the registrant, including its consolidated subsidiaries, is made known to us by others within those
entities, particularly during the period in which this report is being prepared;
(b) designed such internal control over financial reporting, or caused such internal control
over financial reporting to be designed under our supervision, to provide reasonable assurance
regarding the reliability of financial reporting and the preparation of financial statements for
external purposes in accordance with generally accepted accounting principles;
(c) evaluated the effectiveness of the registrants disclosure controls and procedures and
presented in this report our conclusions about the effectiveness of the disclosure controls and
procedures, as of the end of the period covered by this report based on such evaluation; and
(d) disclosed in this report any change in the registrants internal control over financial
reporting that occurred during the registrants most recent fiscal quarter (the registrants fourth
fiscal quarter in the case of an annual report) that has materially affected, or is reasonably
likely to materially affect, the registrants internal control over financial reporting; and
5. The registrants other certifying officer and I have disclosed, based on our most recent
evaluation of internal control over financial reporting, to the registrants auditors and the audit
committee of registrants board of directors (or persons performing the equivalent functions):
(a) all significant deficiencies and material weaknesses in the design or operation of
internal control over financial reporting which are reasonably likely to adversely affect the
registrants ability to record, process, summarize and report financial information; and
(b) any fraud, whether or not material, that involves management or other employees who have a
significant role in the registrants internal control over financial reporting.
Date: August 29, 2008
|
|
|
|
|
|
|
|
|
/s/ Harold M. Stratton II
|
|
|
Harold M. Stratton II, |
|
|
Chief Executive Officer |
|
|
exv31w2
Exhibit 31.2
CERTIFICATION OF CHIEF FINANCIAL OFFICER
PURSUANT TO SECTION 302 OF THE SARBANES-OXLEY ACT OF 2002
I, Patrick J. Hansen, certify that:
1. I have reviewed this annual report on Form 10-K of STRATTEC SECURITY CORPORATION;
2. Based on my knowledge, this report does not contain any untrue statement of a material fact
or omit to state a material fact necessary to make the statements made, in light of the
circumstances under which such statements were made, not misleading with respect to the period
covered by this report;
3. Based on my knowledge, the financial statements, and other financial information included
in this report, fairly present in all material respects the financial condition, results of
operations and cash flows of the registrant as of, and for, the periods presented in this report;
4. The registrants other certifying officer and I are responsible for establishing and
maintaining disclosure controls and procedures (as defined in Exchange Act Rules 13a-15(e) and
15d-15(e)) and internal control over financial reporting (as defined in Exchange Act Rules
13a-15(f) and 15d-15(f)) for the registrant and have:
(a) designed such disclosure controls and procedures, or caused such disclosure controls and
procedures to be designed under our supervision, to ensure that material information relating to
the registrant, including its consolidated subsidiaries, is made known to us by others within those
entities, particularly during the period in which this report is being prepared;
(b) designed such internal control over financial reporting, or caused such internal control
over financial reporting to be designed under our supervision, to provide reasonable assurance
regarding the reliability of financial reporting and the preparation of financial statements for
external purposes in accordance with generally accepted accounting principles;
(c) evaluated the effectiveness of the registrants disclosure controls and procedures and
presented in this report our conclusions about the effectiveness of the disclosure controls and
procedures, as of the end of the period covered by this report based on such evaluation; and
(d) disclosed in this report any change in the registrants internal control over financial
reporting that occurred during the registrants most recent fiscal quarter (the registrants fourth
fiscal quarter in the case of an annual report) that has materially affected, or is reasonably
likely to materially affect, the registrants internal control over financial reporting; and
5. The registrants other certifying officer and I have disclosed, based on our most recent
evaluation of internal control over financial reporting, to the registrants auditors and the audit
committee of registrants board of directors (or persons performing the equivalent functions):
(a) all significant deficiencies and material weaknesses in the design or operation of
internal control over financial reporting which are reasonably likely to adversely affect the
registrants ability to record, process, summarize and report financial information; and
(b) any fraud, whether or not material, that involves management or other employees who have a
significant role in the registrants internal control over financial reporting.
Date: August 29, 2008
|
|
|
|
|
|
|
|
|
/s/ Patrick J. Hansen
|
|
|
Patrick J. Hansen, |
|
|
Chief Financial Officer |
|
exv32
Exhibit 32
Certification of Periodic Financial Report
Pursuant to 18 U.S.C. Section 1350
Pursuant to 18 U.S.C. Section 1350, as adopted pursuant to Section 906 of the Sarbanes-Oxley
Act of 2002, each of the undersigned officers of STRATTEC SECURITY CORPORATION (the Company)
certifies that the Annual Report on Form 10-K of the Company for the year ended June 29, 2008 fully
complies with the requirements of Section 13(a) of the Securities Exchange Act of 1934 and
information contained in that Form 10-K fairly presents, in all material respects, the financial
condition and results of operations of the Company.
|
|
|
|
|
|
|
|
Dated: August 29, 2008 |
/s/ Harold M. Stratton II
|
|
|
Harold M. Stratton II, |
|
|
Chief Executive Officer |
|
|
|
|
|
Dated: August 29, 2008 |
/s/ Patrick J. Hansen
|
|
|
Patrick J. Hansen, |
|
|
Chief Financial Officer |
|
|
This certification is made solely for purpose of 18 U.S.C. Section 1350, subject to the
knowledge standard contained therein, and not for any other purpose.